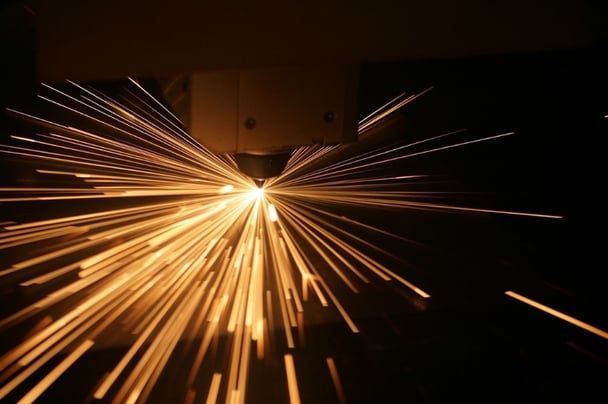
Are Brazed, soldered, or welded joints able to be coated? Are there compatibility problems with the coating? Let’s discuss each of these questions in detail.
Coating Joined Parts
First let’s discuss brazing and soldering. Customers usually have 3 concerns about processing solder and braze joints in customer-supplied parts:
- Will the joint physically survive the heat exposure of our process?
- Will the solder/braze material contaminate SilcoTek processing systems (vessels / lines / other customer parts)?
- Will the joint area pass SilcoTek’s visual inspection criteria?
In this blog post you will learn:
- Recommended joining methods that are compatible with the SilcoTek coating process.
- Steps to take to assure a high quality coated brazed or welded joint.
- How to avoid joint failures during the silicon barrier coating process.
|
Let’s discuss the third concern first. It is common for the coated solder/ braze joint area to appear “hazy” after processing. Though the coating performance should not be negatively affected, the customer can expect a different visual appearance in the brazed or soldered areas.
Brazing and Process Concerns: Process Heat exposure and Contamination
Brazing is a joining process where metals are bonded together using a filler metal with a lower melting point than the base material. Heat, via torch or furnace, is used to liquefy and allow the flow of filler metal (via capillary action), which then cools, solidifies, and joins the base material. Additional materials, such as flux, may be used to prevent the accumulation of oxides and other undesirable contaminants in the filler metal.
Brazing and soldering are typically defined by the melting temperature of the filler material, with brazing joints rated to withstand temperatures over 450°C whereby solder joints can fail above 370°C. Most braze joints will survive our process, however it’s our experience that vacuum nickel brazing yields the best coating appearance.
Recommendations for braze joints:
- Most braze joints are compatible with our process temperatures
- Most braze joints will not cause contamination issues
- The most preferred braze method is Vacuum Nickel Brazing. This joining method is highly compatible with our process and does not show cosmetic hazing. Titanium brazing, although not as popular, also coats well.
- For high copper-containing filler material, a general recommendation is to follow our current existing guidelines on copper-containing base materials.

Soldering and Process Contamination Concerns
Solder filler material may have some of the same components as found in braze materials, such as silver and copper, but it is also alloyed with metals such as tin, bismuth, indium, zinc, antimony, and gold. Solder is applied at a lower temperature than brazing and typically contains metals with a lower melting temperature. The lower application temperature of solder means that the joint will likely fail when exposed to our elevated process temperature. The resulting joint failure may also contaminate the process and result in compromised coating quality.
Recommendations for solder joints:
- Because of their low melting temperature, it is not recommended to process parts with soldered areas, especially those with high percentages of tin, lead, and zinc.
- However, the presence of the above materials may not disqualify the use of a specific solder. It is best to know the specific temperature limitations of the solder material and contact our Technical Service Team to discuss the application.
A note about silver soldering. Silver soldered components are typically not soldered, but rather brazed. Most “silver solder” joints will survive SilcoTek’s processing but may appear hazy after the coating deposition.
Learn how to get the most out of your products and our coatings. Get our Coating Properties Quick Reference Guide.
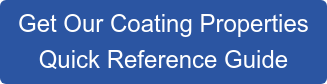
Welding
Welding is a high temperature joining of 2 parts. The process usually involves using a welding stick composed of various alloys to join 2 components. The extreme temperature associated with welding will remove the SilcoTek coating approximately 2-4mm in all directions from the heat affected zone. When possible, it is recommended to first weld parts, then send them to SilcoTek for coating. Go to our FAQ Page to learn more about coating capability and part size.
SilcoTek can coat over high-quality welds, such as those listed in our material compatibility guide, without process contamination and with excellent coating appearance
Joining Summary
SilcoTek is able to coat over welded and brazed parts if the joining process involves a TIG/ MIG weld, vacuum-nickel brazing, or a silver solder that can withstand up to 450°C. Please see our Technical Insight, “Recommendations for Coating Components with Braze and Solder Joints” to learn more. Contact our Technical Service Team if you have questions about process compatibility or coating performance. We're here to contribute to solving your product contamination problems.
Stay current with the latest in coating technology. Subscribe to our email and blog or follow us on LinkedIn.
