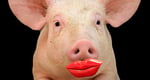
Stainless steel should be stainless right? Untrue. If you're in the chemical process, refining or anayltical business you'll be the first to dispel that notion. On occasion, SilcoTek will receive rusted stainless steel components from customers who hope we can remove rust and improve the corrosion resistance by applying one of our coatings like Dursan® or Silcolloy®. Can we put lipstick on that pig? Maybe, read on to find out.
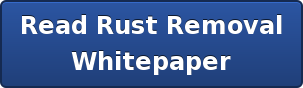
Some background
Stainless steel part before rust removal
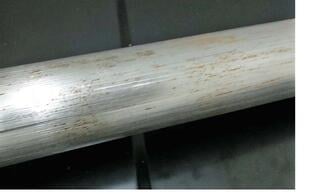
Stainless steel is typically specified because of its ability to resist corrosion in a variety of environments. Unfortunately, stainless steel is not fully stain- or rust-proof, it is just more resistant to attack. Exposure to high salinity environments such as sea water can remove the native protective layer (chromium oxide) and allow oxidation/corrosion to occur at the substrate.
Silcolloy® or Dursan® coatings are applied to improve the corrosion resistance of stainless steel and other alloys. The effectiveness of the coating as a barrier to corrosive attack can be compromised if the substrate surface has pre-existing rust spots/stains. Read more about SilcoTek coating solutions.
So what is the most effective way to remove surface rust from stainless steel?
Stainless steel part after rust removal.
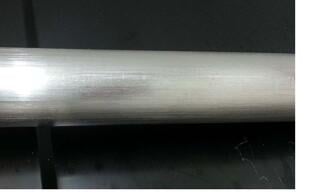
The best method will effectively remove surface rust, but minimize impact to the bulk stainless steel substrate. Two methods used by SilcoTek® to remove surface rust employ weak acids.
Phosphoric Acid
Phosphoric acid will dissolve iron oxide without attacking the other components of the steel (chromium and chromium oxide, nickel, and iron). Phosphoric acid is readily available from a number of commercial suppliers (SilcoTek uses 85% ‘food grade’) and it can be used with no dilution because of its non-aggressive nature. Clean up after acid treatment is done by rinsing parts in deionized water thoroughly and then returned to the coating process.
Acetic Acid
The reaction with acetic acid is often slower than phosphoric acid and can be a better choice when the underlying corrosion/staining affects a larger percentage of the substrate. Acetic acid is also available commercially (SilcoTek uses glacial acetic acid which is greater than 99.7% pure) and requires no dilution prior to use as a rust remover. Following the acid exposure, parts must be rinsed thoroughly with deionized water prior to re-entry into the coating process.
Conclusion:
The best substrate to coat is one that is clean and does not show rust. If there is a potential for free iron on your part’s surface, SilcoTek recommends addressing it prior to shipping to us.
If it is not possible to apply the removal techniques in-house, SilcoTek’s sales group can provide a quote for the acid cleaning process upon request.
Have a question about the surface of your part? Contact our Technical Service Team and speak with an expert.
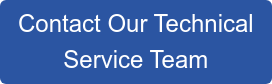