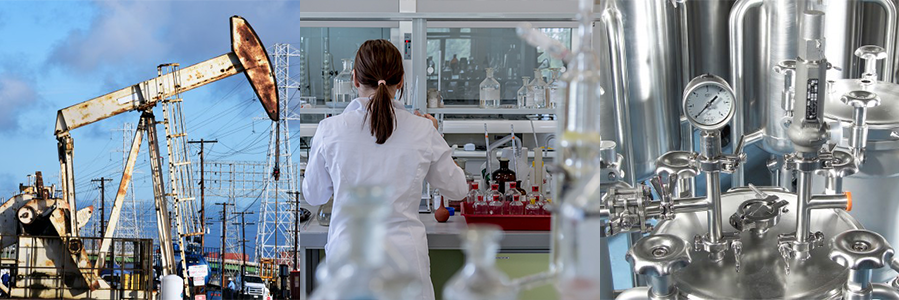
In this blog post we'll discuss the various types of surface defects that contribute to an imperfect stainless steel appearance, and how to correct or prevent imperfections.
In this blog post you will learn:
- How various surface imperfections can affect the appearance of stainless steel.
- Identify various imperfections commonly found on stainless steel surfaces.
- How to mitigate and correct common stainless steel surface imperfections.
|
Addressing Common Stainless Steel Surface Imperfections
Most common stainless steel surface defects that are difficult to remove are produced during fabrication. For some processes, surface imperfections aren't a problem but for CVD coating processes those imperfections can lead to coating quality problems, analytical test problems, or process contamination issues.
Figure 1 illustrates the common types of surface defects arising during steel fabrication.1
Common stainless steel surface imperfections include:
Embedded iron particles Sulfide inclusions Heat tint Arc strikes |
Grind marks Weld spatter Scratches Organic contamination Electropolish frosting |
Solutions to improve or prevent stainless steel surface problems range from:
- Acid treatment
- Inert gas shielding
- Employing prudent cleaning methods
- High temperature oxidation
- Polishing
- Establishing strict electropolish specifications
Continue reading to get details on how to improve stainless steel surface quality. If you want to learn more about how to improve surfaces in analytical and high purity applications, read our e-book, "Managing Challenging Sampling Enviromnents" .
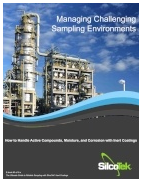
Identifying and Correcting Common Stainless Steel Imperfections
Let's address techniques for identifying and correcting some of the more common imperfections found in stainless steel in more detail.
Embedded Iron
Embedded iron is the most common surface defect that arises during fabrication. Iron particles as a result of wear and tear, as well as grinding dust and showers of sparks during carbon steel grinding, can burn into and contaminate a stainless steel surface. Iron is also easily embedded during handling and layout unless stainless steel is protected from contact with wire slings, clamps, layout tables and rolls. Iron embedment is more common in shops that fabricate carbon steel as well as stainless steel parts. This is why stainless steel needs to be protected from carbon steel and must be processed separately from carbon steel.2
Iron particles embedded in the stainless steel surface will cause rust when they are exposed to a moist atmosphere, and if not addressed, can produce additional pitting corrosion. If a customer’s parts have a high risk of iron embedment, SilcoTek recommends a simple water test or a more sensitive ferroxyl test as described in ASTM A380 to detect and remove embedded iron before sending to SilcoTek for coating.
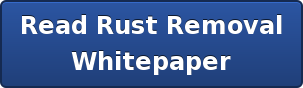
In cases where SilcoTek receives iron embedded parts and detect minor rust spots after our standard surface prep process (as shown in Figure 2 below), we typically employ a mild acid treatment to remove the rust spots before subjecting the parts to our CVD silicon barrier coating process. For details of common rust removal process, refer to our blog post “Removing rust from Stainless Steel”.
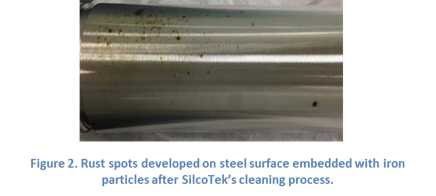
For parts that show severe rust or large rust areas, we recommend employing pickling treatments. Pickling is a more aggressive treatment that requires elimination of the surface layers with embedded defects, up to 25 – 40 mm of the substrate metal may be removed, and is usually done in a nitric-hydrofluoric acid (HNO3 – HF) bath.3 Pickling should be done by a qualified vendor, SilcoTek is not equipped to handle pickling treatments.
Sulfide Inclusions
Sulfide inclusions, especially manganese sulfide (MnS) inclusions, are believed to be the predominant sites for the initiation of pit corrosion in stainless steel. Manganese is added in the fabrication of stainless steel to make the steel easier to machine, but it was recently discovered that during the cooling of the stainless steel, the MnS inclusions suck chromium atoms from the surrounding area, leaving behind a chromium-deficient region. This Chromium-deficient region becomes a weak point for corrosion to initiate (pit), and deteriorates the steel surface.4
Such inclusions in stainless steel may be difficult to detect with the naked eye, but show up as dark spots or strings under SEM (scanning electron microscope), as shown in Figure 3 below.5 These inclusion sites can appear as local abnormalities post SilcoTek’s coating deposition, as our thin CVD coating (sub- micron) often highlights substrate imperfections. If not addressed, these inclusion sites can compromise the protective properties offered by SilcoTek coating at these local areas, as these weak points serve as initiation sites for pit corrosion.
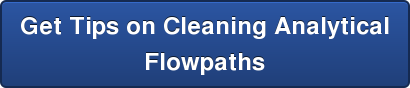
For best coating appearance and performance, SilcoTek recommends the customer to remove any inclusions prior to sending their parts to us for coating. An acid treatment in nitric acid or a heat treatment of the steel to allow Cr atoms to diffuse from the inclusion back into the surrounding area is recommended to remove inclusion sites.5
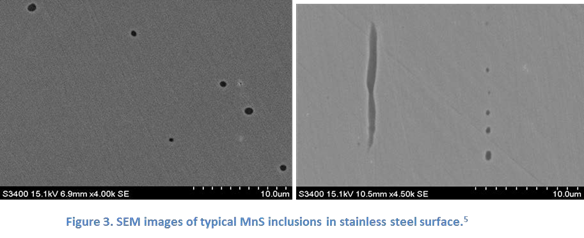
Heat tint, arc strikes and weld spatter
These are all surface defects produced during the steel welding process (illustrated in Figure 4 below), and are easier to avoid through prevention measures than through removal procedures.
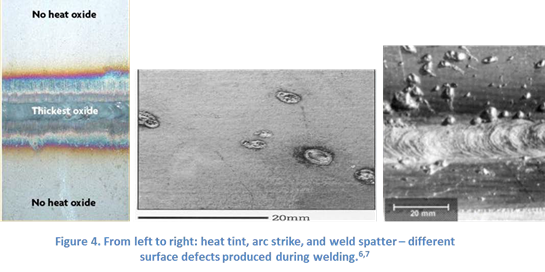
Heat tint (also known as weld discoloration) is a thicker-than-normal chromium oxide film on the surface of the stainless steel. Heat tint films range in color from light brown to black. Figure 4 above shows the typical heat tint on the welded side if stainless steel is welded without inert gas protection.6 As more chromium is consumed to form the heavier film; the surface beneath the heat tint is depleted in chromium and therefore reduced in its inherent corrosion resistance.
Arc strikes and weld spatter both produce small pinpoint surface defects that penetrate through the surface oxide layer and extend into the substrate steel. They form sites where corrosion can initiate.
These surface defects (heat tint, arc strikes and weld spatter) will show through SilcoTek coatings if they are not addressed, and will compromise the coating’s local anti-corrosion properties at the defect sites.
It is costly and difficult to completely remove welding related defects, and the best way to address them is by taking prevention measures, such as employing proper welding techniques, using inert gas shielding during welding, and using anti-spatter paint (note to remove paint after welding is completed).8
Organic contamination
SilcoTek’s alkaline-based surface preparation process is designed to remove any oil, grease and other organic residues on the stainless steel surface prior to the CVD coating being applied. Alkaline surface cleaning is a highly effective approach for the majority of the parts received by SilcoTek, but exceptions do exist.
We have experienced difficulties in removing certain glycol-based or Krytox® fluorinated cutting fluids in the past, especially when the oil was left to dry on hot parts before rinsing. To learn more about cleaning techniques, go to our whitepaper “How clean is clean”.
Figure 5 shows a part contaminated with organic residues that cannot be completely removed by SilcoTek’s pre-deposition procedures. In such cases, SilcoTek will contact the customer to learn more about the handling and manufacture of the parts prior to our receipt, and we'll discuss/ recommend process changes as appropriate.
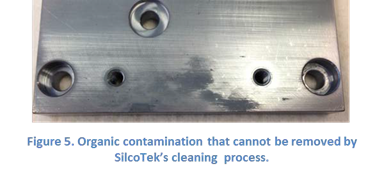
If the organic residue is “burnt into” the steel substrate, such as from pyrolysis of lint contamination, it usually manifests itself as black spots or blemishes on the surface. The lint can originate from cotton gloves or cotton gauze used to handle and clean parts prior to welding. Pyrolysis of other hydrocarbons can also create black spots. If this is the case, SilcoTek typically employs a high temperature oxidation process to eliminate the carbon contamination prior to application of the CVD coating.
Scratches and other physical damage
SilcoTek technicians conduct an inspection at the receipt of customer parts. If any scratches or physical damage are noticed on the parts at arrival, we will contact the customer to find out whether the scratched/damaged area is a critical area to their specific applications, and will either continue with processing or return parts to the customer for replacement based on the customer’s feedback. An example of scratched part identified by SilcoTek receiving technician is shown below in Figure 6.
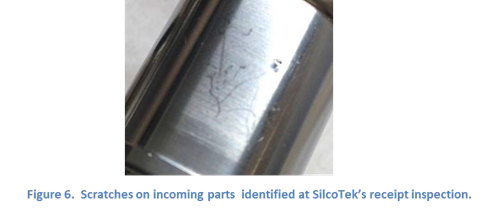
To minimize surface damage, SilcoTek recommends following a strict packaging methodology to prevent damage in transit. To learn more about how to prevent packaging issues, read our packaging blog post.
Electropolished surfaces
When a superior surface finish is desired, sometimes a final electropolishing process is applied to metal parts to achieve a desired aesthetic appearance or optimized corrosion resistance. However, there are certain pitfalls in the electropolishing process to watch out for, such as an effect referred to as electropolish “frosting”. Please refer to our white paper “Coating electropolished surfaces” for detailed discussion on this subject.
Conclusion
SilcoTek receives and processes hundreds of customer parts daily, and these parts may have seen hundreds of different handling techniques and surface treatments before they reach us. We strive to coat each and every piece consistently and beautifully every time, in our commitment of plus 1 service to all our customers. However, various imperfections present in the substrate materials as discussed above may contribute to an imperfect appearance on a small percentage of the parts. When this happens, SilcoTek will reach out and collaborate with our customers to find a solution together. It is always our goal to provide the best quality coating and service to every customer every time, with zero disappointments.
To stay current with the latest in surface science, subscribe to our blog. Or follow us on LinkedIn.

References
1. http://www.assda.asn.au/technical-info/surface-finishes/stainless-fabrication-common-traps- to-avoid.
2. W. Buijs, “How do you remove and prevent flash rust on stainless steel?” Stainless Steel World November 2008 issue.
3. H. Tuthill and R. E. Avery, “Specifying stainless steel surface treatments”, Advanced Materials & Processes 1992, 142 (6), 1.
4. P. Ryan, D. E. Williams, R. J. Chater, B. M. Hutton & D. S. McPhail, “Why stainless steel corrodes”, Nature 2002, 415, 770.
5. W. Gjonnes, “Effect of sulfide inclusions in austenitic stainless steel on the initiation of pitting in base metal and heat affected zone after welding”, Master thesis 2012.
6. http://www.foodprocessing.com.au/articles/40976-Purge-welding-stainless-steel-for- cleanability-and-corrosion-resistance.
7. J. Helliwell, “Defects and discontinuities”, ESC defects training QA/QC.
8/ H. Tuthill, “Stainless steel: surface cleanliness”, Pharmaceutical Engineering 1994, 14 (6).