SilcoTek commissioned Massachusetts Materials Research, Inc. to conduct a comprehensive evaluation of our Dursan® coating process on the bulk metallurgical properties of 316 stainless steel. This initiative aimed to address customer inquiries regarding potential alterations to stainless steel substrate properties induced by the Dursan process. Dursan coating was selected for testing due to it being our hottest processing temperature (450°C), so all coatings would be equal to or less than Dursan's results.
Testing Procedure:
The study involved comparative testing on three types of samples: untreated 316 stainless steel (referred to as "Control"), 316 stainless steel subjected to the same thermal exposure as the Dursan process in a nitrogen atmosphere ("Heat Sample"), and 316 stainless steel coated with the standard Dursan process ("Dursan"). Tensile Properties (at Room Temperature and 450°C), Charpy Impact, and Rockwell Hardness tests were performed in triplicate for each sample.
Figure 1: Illustration if Tensile Strength test coupon.
Tensile Properties (ASTM E8-16a) at Room Temp |
Control |
Heat Sample |
Dursan Coated |
Ultimate Strength (psi) |
93,000 |
96,000 |
96,000 |
0.2% Yield Strength (psi) |
49,600 |
52,000 |
52,000 |
% Elongation |
56 |
54 |
53 |
% Reduction of Area |
78 |
79 |
77 |
Break Location |
Gage |
Gage |
Gage |
Tensile Properties (ASTM E8-16a) at 450°C |
Control |
Heat Sample |
Dursan Coated |
Ultimate Strength (psi) |
71,500 |
70,000 |
76,500 |
0.2% Yield Strength (psi) |
31,500 |
30,800 |
32,600 |
% Elongation |
37 |
36 |
40 |
% Reduction of Area |
74 |
73 |
71 |
Break Location |
Gage |
Gage |
Gage |
Charpy Impact (ASTM E23-12c) Energy of Rupture (Ft/lbs) |
Control |
Heat Sample |
Dursan Coated |
Sample 1 |
264 |
264 |
264 |
Sample 2 |
264 |
264 |
264 |
Sample 3 |
264 |
264 |
264 |
Average |
264 |
264 |
264 |
NONE OF THE SAMPLES BROKE |
|
|
|
Rockwell Hardness (RBW) |
Control |
Heat Sample |
Dursan Coated |
|
94 |
93 |
94 |
Results Overview:
The Tensile Properties tests, which included Ultimate Strength, 0.2% Yield Strength, % Elongation, and % Reduction of Area, indicated no significant variation among the three sample types at both room temperature and 450°C. Charpy Impact tests revealed consistent Energy of Rupture for all samples, with none experiencing breakage. Rockwell Hardness measurements displayed minimal differences among the Control, Heat Sample, and Dursan-coated stainless steel.
Conclusion:
The comprehensive metallurgical testing comparison demonstrated that the Dursan coating process did not produce noteworthy changes in the physical properties of 316 stainless steel. The comparison of untreated stainless steel, Dursan-coated stainless steel, and stainless steel exposed to the Dursan heat profile under a nitrogen atmosphere revealed no significant variance. Notably, there were slight improvements in tensile properties for the Dursan and Heat Sample test pieces.
Moving Forward:
SilcoTek's Research and Development Team continues to subject coatings to rigorous testing under demanding conditions. This ongoing commitment aims to understand both the benefits and limitations of chemical vapor deposition processes, providing customers with relevant and reliable coating performance data.
Think you have an application that SilcoTek's coatings can help with? Reach out to our coating experts today!
Subscribe for updates on our latest research findings and coating developments.
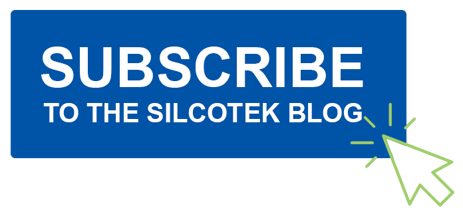