Chronic flare and stack sampling issues in petrochemical and refining operations can have significant consequences, affecting not only the efficiency of the processes but also posing potential risks to the environment, worker safety, and compliance with regulatory standards. These issues often stem from a combination of factors, including the selection of poorly specified sampling equipment, budgetary constraints limiting investment in advanced technologies, and a lack of regular maintenance and inspection.
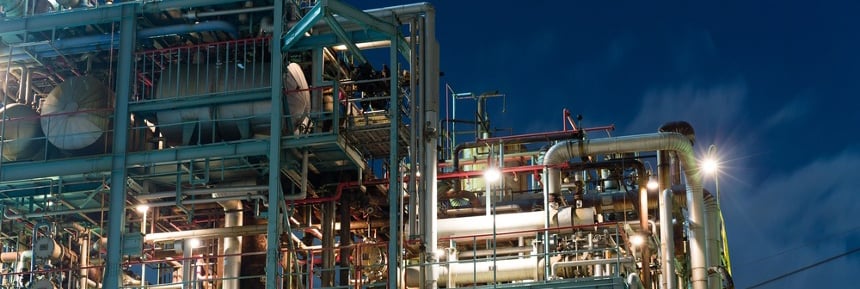
One of the key challenges in addressing these sampling issues is the reluctance to embrace new techniques and concepts that could enhance sample reliability and lower detection limits. Traditionally, industries might have relied on methods that were successful in the past, but with changing regulations and more demanding customers, there is a need to adapt to the "new reality" of stringent part-per-million or even part-per-billion sampling requirements.
1. Assuming that priming the system will yield good sample results, when extremely low sulfur detection limits require extensive passivation of stainless steel flowpaths.
One common misconception among sampling teams is the belief that they can simply prime the system and achieve accurate sample results. However, in today's regulatory environment, extremely low sulfur detection limits are mandated, necessitating meticulous passivation of millions of active sites in stainless steel sampling flowpaths. This process alone can take days to weeks, and subsequent desorption of sulfur can lead to random spikes, making the measurement process complex and unreliable. To address this, coating the sample flowpath with inert materials like Dursan® or SilcoNert® can eliminate adsorption, preventing interaction between the reactive sulfur sample and the adsorptive stainless steel, thus guaranteeing an inert flowpath and accurate results.
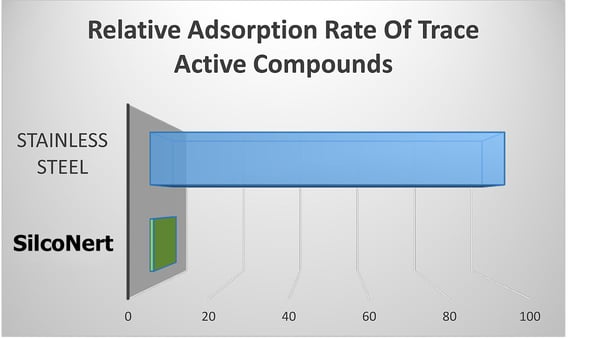
2. Neglecting to coat all parts of the system, leading to sulfur adsorption on uncoated surfaces and producing inaccurate test results.
Another misconception is that it is acceptable to avoid coating all parts of the sampling system to save costs. However, neglecting to coat surfaces such as filters or fittings can result in sulfur sticking to uncoated areas, leading to contaminated samples and compromised results. Even a single uncoated component, such as a sintered metal filter, can adsorb a significant portion of the sample, impacting product quality and potentially leading to non-compliance with regulations and unhappy customers.
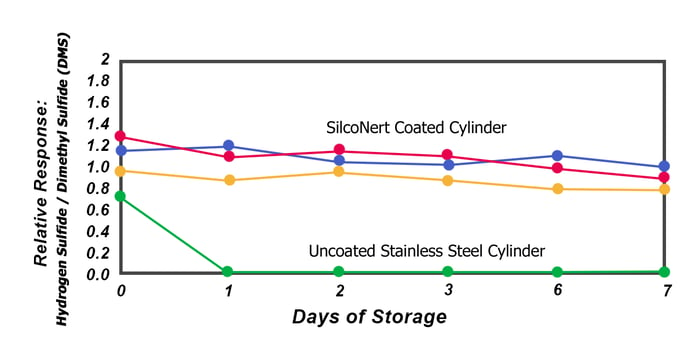
3. Ignoring moisture, which can lead to increased sulfur adsorption and corrosion, affecting low-level sample readings.
Moisture is another critical factor that is often overlooked in sampling systems. Even small amounts of water stagnated in sample cylinders, fittings, or tubing can adsorb sulfur and increase corrosion, thereby compromising low-level sample readings. Proper system design, along with the use of inert/hydrophobic coatings like Dursan can enable rapid purging of moisture from the sampling system, reducing sulfur adsorption and giving the sampling team greater control over moisture-related issues.
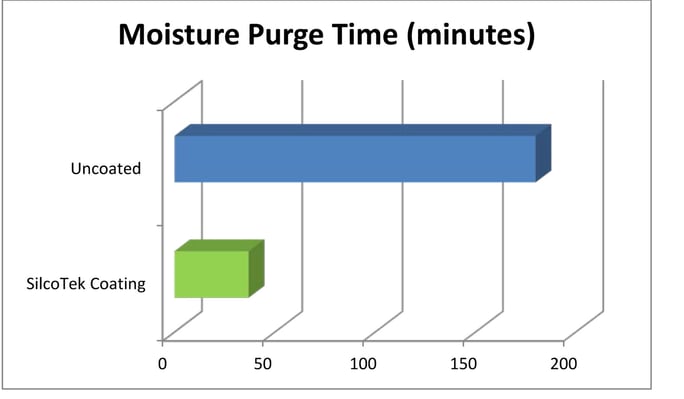
4. Overlooking internal surface rust in sample cylinders, which can absorb a significant amount of H2S, leading to unreliable sampling.
Internal surface rust within sample cylinders is another concern that is sometimes disregarded. Corroded sampling components are capable of absorbing a significant portion of the H2S sample, leading to inaccurate and artificially low readings. To avoid this problem, regular inspection and maintenance of sample cylinders are necessary to ensure that the interior surfaces are free of rust particulates and corrosion.
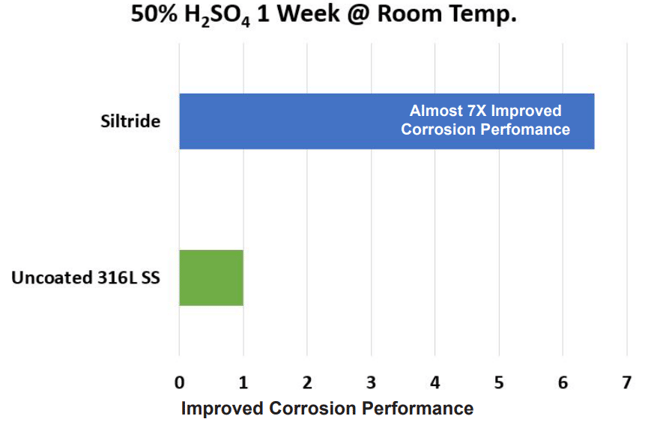
5. Underestimating the need for a fast response system, as uncoated stainless steel can delay sulfur transfer and cause potential refinery upset conditions.
Lastly, some operators may underestimate the importance of a fast response system and opt for stainless steel components without coatings to save costs. Waiting hours for H2S readings to stabilize can result in costly downtime and potential hazards. A delayed response in sulfur transfer can lead to upset conditions in the refinery, affecting operations for several days or even hours. Coatings like SilcoTek significantly enhance the response of the system, enabling faster and more accurate measurements compared to uncoated stainless steel.
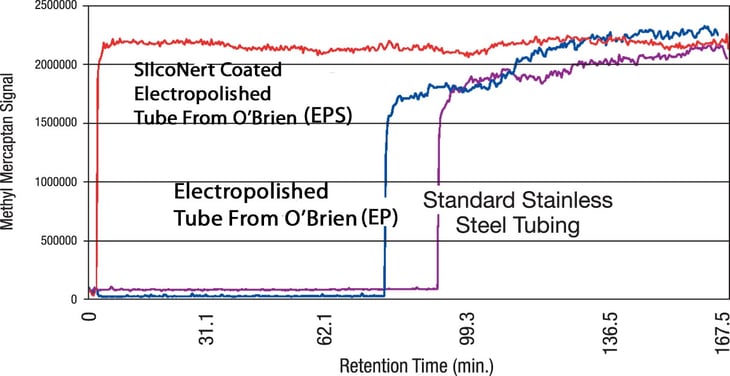
In conclusion, addressing chronic flare and stack sampling issues requires a shift in mindset and practices within the industry. Embracing new techniques, investing in proper sampling equipment, and utilizing inert coatings can lead to improved sample reliability, compliance with regulations, and overall operational efficiency in petrochemical and refining operations. By dispelling these misconceptions and adopting innovative approaches, industries can overcome sampling challenges and ensure a safer, more sustainable future.