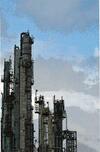
A recent article in Hydrocarbon Processing, "10 Sure Ways To Substandard Reliability Performance" by H. P. Block discussed attitudes and factors contributing to poor plant reliability. The article cited a culture of bias, tolerance, a buy on the cheap attitude, and an overall permissive environment combining to assure poor plant reliability. Refiners can't afford to take short cuts in H2S sampling reliability, but all too often they do.
SilcoTek® Technical Service staff often encounter customer opinions and beliefs that contribute to poor H2S sample reliability and ultimately to poor refinery performance. Here are our top 10....
I can prime the system and avoid using coatings.
Forget it, in this day and age regulations dictate very low sulfur detection limits. Attempting to saturate active sites in sampling systems with low part-per-million levels of sulfur will take days to weeks to stabilize. Subsequent sulfur desorption will make accurate measurements impossible.
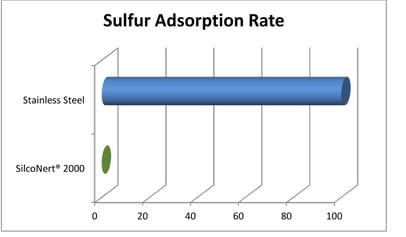
We don't have to coat all the parts in the system.
Attempting to save a few bucks by not coating fittings or filters is penny wise and pound foolish. Sulfurs will stick to the uncoated surfaces and render test results to the garbage.
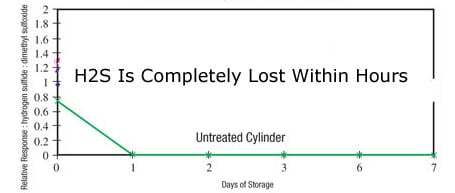
We don't have to worry about moisture.
Failure to manage moisture in sample transfer systems will result in pockets of sulfur adsorbing water. The water will increase corrosion and significantly reduce sulfur readings. Robust system design and use of hydrophobic/inert coatings help to quickly purge moisture from sampling systems, ultimately minimizing sulfur adsorption.
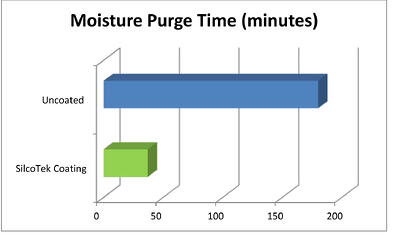
We don't need to have accurate monitoring, if we don't detect sulfur, it's not there, right?
This strategy works until your downstream customer detects high levels of sulfur from your plant; then the paltry savings from not coating sample surfaces will be more than lost in damages paid to your customer.
Internal surface rust isn't a problem, I can keep using that sample cylinder.
Reusing corroded sampling components will adsorb sulfur; making sampling a useless exercise.
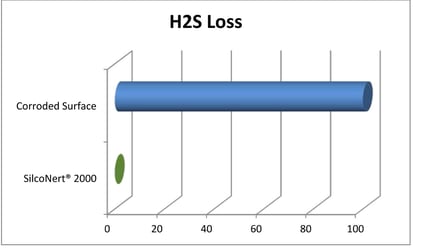
All coatings are the same, I'll get the cheapest.
Not all inert coatings are the same. SilcoTek® coatings are the most inert coatings in the industry. Results can vary significantly when using cheap alternatives.
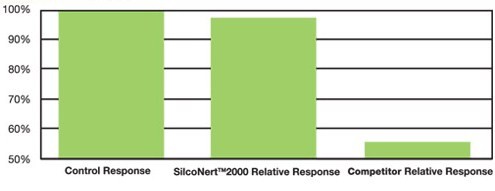
We don't need to have fast response in our system. We can save a few dollars and go with stainless steel.
Waiting hours for H2S readings to stabilize can be dangerous and expensive. No refiner wants to run for hours or days in an upset condition; or send feed stock to a downstream processor only to realize the supply was contaminated. SilcoTek® coatings improve system response by orders of magnitude compared to uncoated stainless steel. Adsorption can significantly delay sulfur transfer, resulting in potential refinery upset conditions for many hours or days.
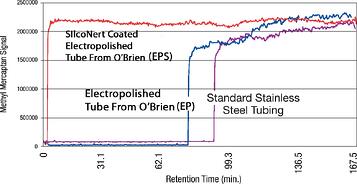
We don't need to coat the high side of our H2S calibration system.
Low calibration or high calibration adsorption will have the same effect, a long and tedious calibration. Do you want to spend days bringing your system in calibration when it can be done in minutes?
There's no return on my investment if we coat our system.
A process upset can cost your plant big-time. An ethylene plant can lose $50,000 dollars per hour or more due to a single shutdown. The return on a coated system equates to minutes saved in a single upset.
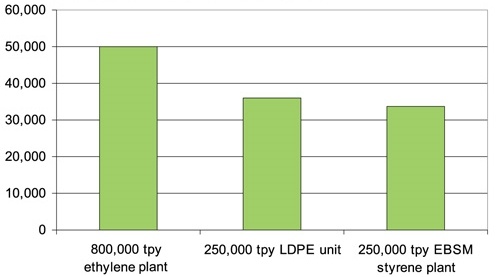
We can't afford to wait for custom coatings. Yes some projects are on a tight schedule, but that's no excuse for not assuring H2S sampling reliability. Need coated parts now? You can buy coated products direct from the manufacturer.
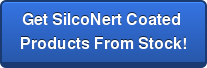