Gas regulators play a crucial role in maintaining precise pressure control across various industries, with engineers and technicians relying on them to operate flawlessly, even under challenging conditions. While these regulators may seem straightforward, there is complex componentry within that demands attention. In this blog post, we'll explore key insights on preventing gas regulator failures and enhancing corrosion resistance, offering 8 valuable tips to keep your calibration or process gas system running at its best.
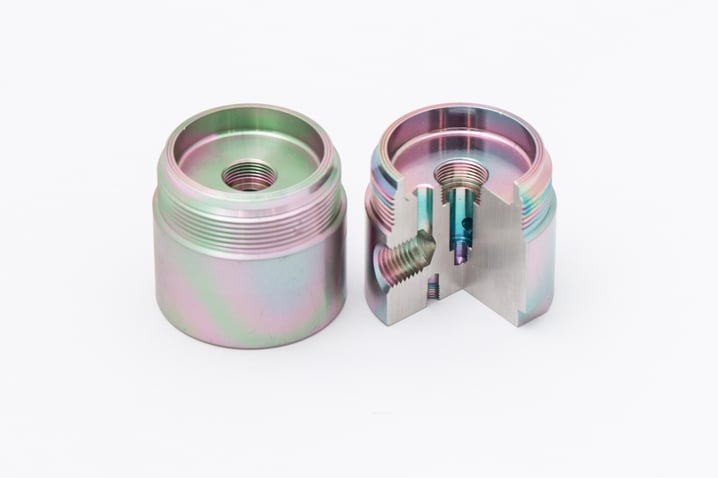
-
Understanding Gas Regulator Components:
Gas regulators consist of numerous precision components, and any failure within these parts can lead to a loss of process control and potentially hazardous conditions. Components such as the diaphragm, poppet, seat, closing spring, and filters all require careful maintenance to ensure optimal performance.
-
Setting Up a Maintenance Plan:
To manage potential issues, it's crucial to establish a maintenance plan tailored to your specific process environment and flow path conditions. Considerations such as leak checks, creep tests, inert purges, overhauls, and component replacements should be part of a routine maintenance schedule.
Maintenance Schedule
SERVICE
|
LEAK CHECK
|
CREEP TEST
|
INERT PURGE
|
OVERHAUL
|
REPLACE
|
Noncorrosive |
Monthly
|
annually
|
Not Applicable
|
5 years
|
10 years
|
Mildly corrosive |
2x Month
|
6 months
|
at shutdown
|
2 years
|
4 years
|
Corrosive |
2x Month
|
3 months
|
at shutdown
|
1-2 years
|
3-4 years
|
-
Combatting Contamination and Maintaining Purity:
Contamination poses a serious threat to gas regulators. Implementing measures to prevent contamination is crucial. Careful material selection, regular inspections, and proper handling will certainly increase the longevity of your equipment and ensure the purity of your sample.
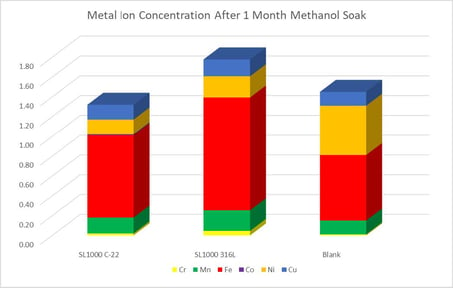
Test results after 1 month Methanol soak. Image to the right is a closer look at the "Low Metal Ion Contamination" section of the left image.
-
Corrosion Resistance:
Corrosive gases pose a threat to regulator components. Choosing corrosion-resistant materials or applying coatings such as Siltride can extend the life of surfaces, offering up to 10 times more corrosion resistance.
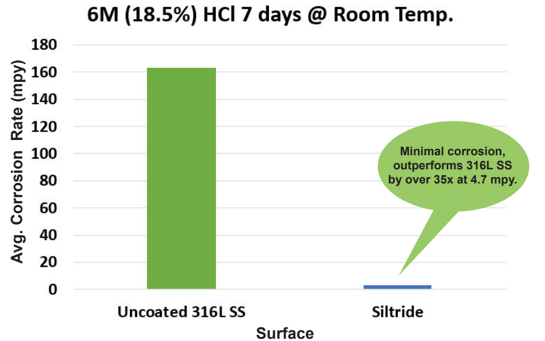
-
Inertness:
Gases passing through the regulator can react with and be adsorbed by various surfaces, impacting calibration results. Coating flow paths with inert materials like SilcoNert® can minimize adsorption, ensuring accurate calibration, especially for low-level or trace gas samples.
-
Freezing and Moisture Management:
High flow, low temperatures, and moisture can lead to freezing and regulator failure. While heated regulators or heat jackets can prevent freezing, hydrophobic coatings like Notak play a crucial role in repelling moisture, reducing build-up, and enhancing purge effectiveness.
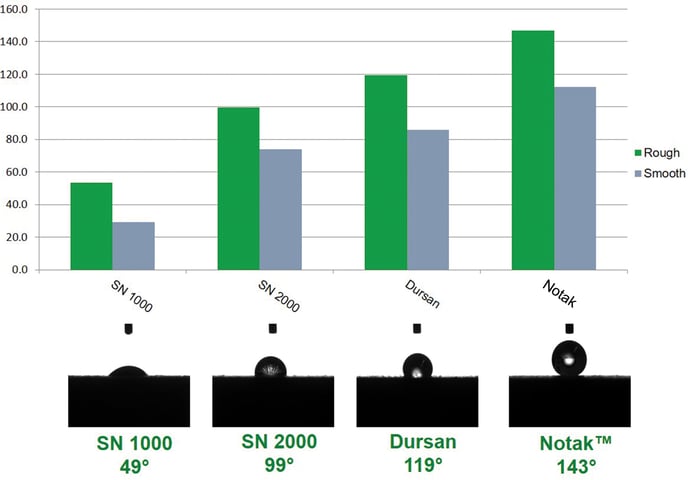
-
Particulate Management:
Particles in the flow path can interfere with gas regulation. Using fritted metal filters is a solution, but these filters can react with calibration gases. Coating filters with Siltride or Silcolloy prevents adsorption, improves corrosion resistance, and keeps the flow path particulate-free.
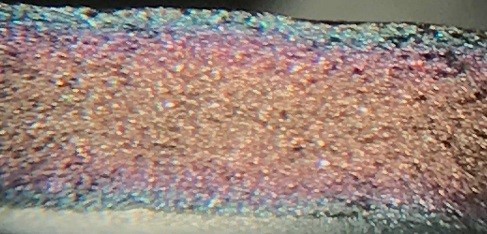
SilcoTek coated filter and zoomed in cross section of a coated frit.
-
Coated Products:
SilcoTek® offers coating services, collaborating with manufacturers to provide coated products. This simplifies the process for customers looking to integrate advanced coatings into their gas regulation systems. In particular, SilcoTek's approved regulator partners, CONCOA, Air Liquide, Tescom, and Restek.
Other Commonly Coated Items
- Sintered metal filters
- Valves, fittings, and tubing
- Sensors and probes
- Regulators, calibration gas flow paths
- GC liners, jets, columns, and other GC flow path components
- HPLC filters, tubing, and columns
- Sample cylinders and other high pressure sample containers
Gas regulator reliability is paramount for maintaining process control and preventing potentially hazardous conditions. By implementing a robust maintenance plan and incorporating advanced coatings, such as Siltride and Silcolloy, industries can significantly enhance the longevity and performance of their gas regulators, ensuring smooth operations and accurate results.
Would you like to discuss your application with our coating experts?