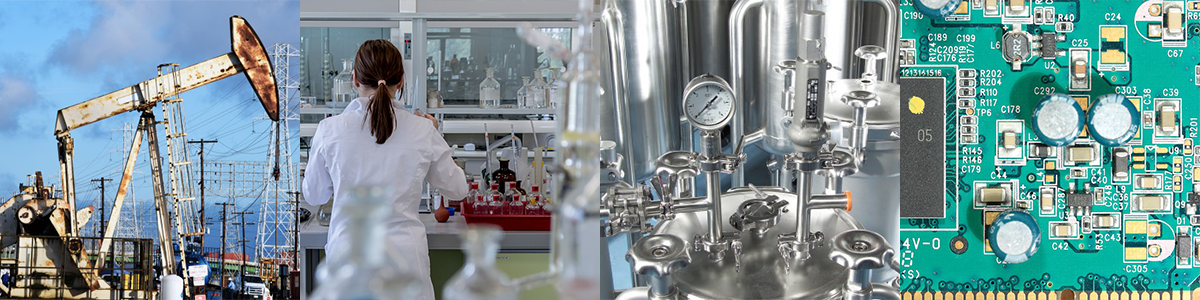
Corrosion in sample transfer, process monitoring, GC or HPLC sample flow paths can cause contamination, chemical adsorption, or test failures. Let's take a deep dive into how to improve corrosion resistance of analytical flow paths.
Analytical testing involving corrosives can damage interior flow path surfaces resulting in pitting, particulate generation and system failures. Corrosion not only shortens the life of analytical systems, it can be a source of adsorption, reactivity, analyte loss, and particulates.
In this blog post your will learn:
- How corrosion can impact analytical test results and cause product contamination problems.
- How inert corrosion resistant CVD coatings can improve test results.
- How CVD coatings can improve the performance of analytical system components like filters.
- How coatings like Dursan, Dursox, and Silcolloy perform under severe corrosive conditions.
|
Corrosion can cause peak distortion and lost peaks which can distort results. This can cost the lab time, money and can cause severe process control problems or even excessive yield loss or product quality problems. Testing for trace compounds like H2S or environmental contaminants in stack, process or air quality monitoring systems can result in eventual corrosion of stainless steel sample transfer components like valves, fittings, tubing, and sample cylinders. This can lead to product contamination problems.
Solving product contamination problems
Corrosion can also damage sensitive instrumentation or probes which can lead to down time or excessive maintenance. A highly reactive surface can result in test failures or poor test results. The left hand graph below demonstrates how a reactive surface caused by corrosion can result in poor peak shape and lost peaks. Protecting the surface with an inert corrosion resistant coating improves peak shape, sensitivity, and test reliability (right chromatogram).
How SilcoTek® coatings change the material properties to solve corrosion problems in analytical flow paths
SilcoTek employs a process called chemical vapor deposition (CVD) to apply anti fouling, inert or corrosion resistant coatings to stainless steel, ceramic, or alloy filter surfaces. The benefit of a CVD coating is that the process will allow the coating vapor to penetrate the difficult to reach areas like filter media and coat the internal surfaces of the entire flow path. Because the deposition is so thin, coated parts aren't clogged or restricted by the coating.

The coated fritted filter cross section below shows how the filter surface is penetrated by the silicon CVD coating. The outer coating layer has the thickest coating which is indicated by a green surface color. The interior surfaces are also coated but with a thinner layer (pink and gold colors). The thinner coating continues to be an effective barrier while allowing the filter to perform without a significant increase in back pressure. SilcoTek applies its coatings via chemical vapor deposition (CVD), which allows all of the filter surface to be covered throughout the entire turbulent flow path. We have performed cross-sectional SEM/EDS analysis of SilcoTek coated metal frits to prove this.
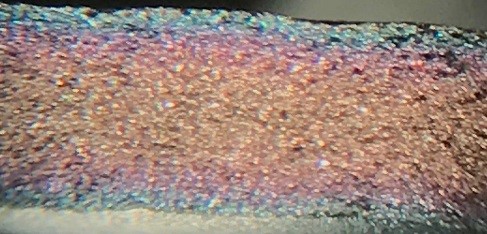
Learn more about how our coating process works and how we coat filters. Read our blog post:
A Dursan coated flow path will significantly extend the life of analytical system components and help to reduce the differential pressure of fritted filter media. The comparative graph below demonstrates how the Dursan coated filter (bottom plot) significantly outperformed the uncoated filters and had less than 1/2 the differential pressure of the uncoated filters after over 10,000 hours of operation.
Corrosion Data for High Temperature Corrosion Resistant Coatings
Dursan® and Silcolloy® are both proven to improve filter corrosion resistance. Silcolloy is a multilayer amorphous silicon deposition that is highly effective at preventing acid corrosion, as well as providing a pure silicon barrier coating, thereby reducing interaction between the metallic filter substrate and the media flowing through the filter. This improves product quality while reducing filter replacement cost.
Dursan is a high durability coating that offers both acid and base corrosion resistance. Both coatings can withstand extreme temperatures and "industrial scale" abuse without failure.
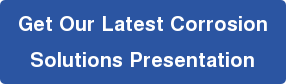
316 stainless steel, Silcolloy coated stainless steel, and Dursan coated stainless steel coupons were immersed into various corrosive liquids for 24 hours. The corrosion rate in mils per year (mpy) was then measured and compared. The Dursan and Silcolloy coated coupons dramatically improved corrosion performance and prevented contamination of the acid. The photo below compares the appearance of the test coupons and acid after immersion. The coated coupons (below center and right) show very little pitting and corrosion and the acid remains clear and uncontaminated.
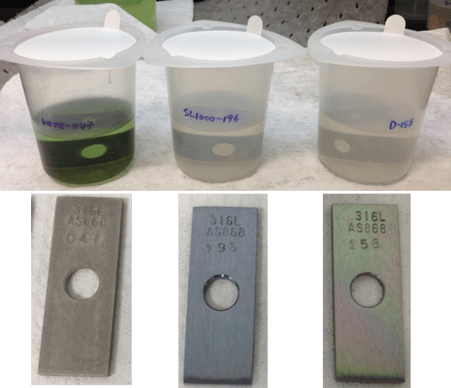
Comparative Data
Corrosion data shows improvement in corrosion resistance by orders of magnitude. We recommend testing our coatings in your application to best assess how our coatings will perform in your application and to apply the best corrosion solution to your problem.
HCL Corrosion Comparison (50C 24 hr immersion per ASTM G31)
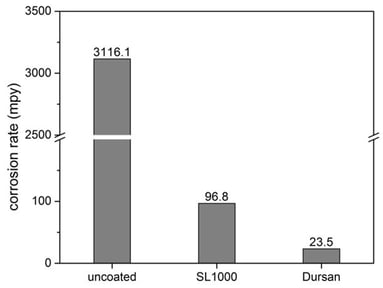
Sulfuric Acid Corrosion Resistance (24 hr ASTM G31)
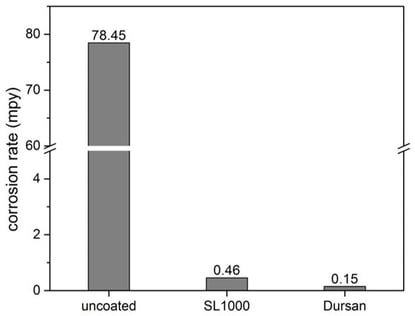
Bleach Corrosion Resistance (per ASTM G31)
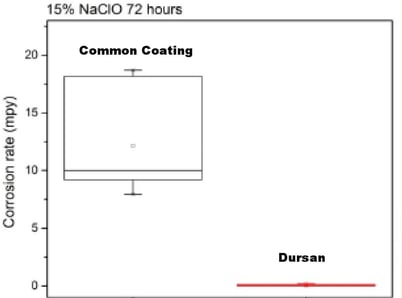
Thick or thin high purity inert CVD coatings like Dursox™ offer exceptional corrosion resistance even under extreme conditions.
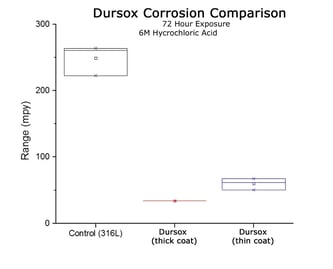
What kind of analytical system components can SilcoTek coat?
The SilcoTek® coating process can accommodate small sintered frits up to filter lengths of approximately 6 feet long in varying diameters. If you have large filters or have large quantities of filters, you'll need to contact our Technical Service staff to discuss the application, dimensions and quantity in order for us to specify the most efficient process parameters for your application.
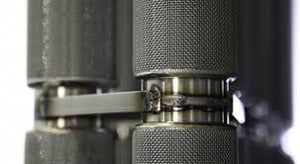 |
SilcoTek is able to coat a wide range of products and materials including:
- Sintered metal filters
- Valves, fittings and tubing
- Sensors and probes
- Regulators, calibration gas flow paths
- GC liners, jets, columns and other GC flow path components
- HPLC filters, tubing, and columns
- Sample cylinders and other high pressure sample containers
|
Summary
A precision CVD coating will improve the corrosion performance of analytical flow path components anywhere from 2x to 50x or more (depending on application and coating). Environmental factors like filtrate concentration, temperature and vibration can significantly impact the ultimate corrosion resistance of a protective coating. Contact our Technical Service Team to discuss your application. Or join us on LinkedIn to ask the experts about your coating needs.
