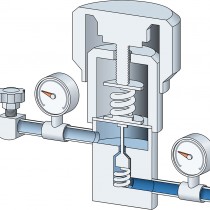
We discuss tips on how to prevent gas regulator failures in spec gas and chemical process gas delivery systems.
Tips for Preventing Gas Regulator Failures
Gas regulators are at the forefront of process control. Engineers and technicians rely on them to maintain precise pressure control often under severe conditions. Here are tips on how to prevent regulator failures, improve corrosion resistance, and keep your calibration or process gas system running at it's best.
In this blog post you will learn:
- Steps to take to maintain regulator performance and gas process control.
- How to improve the chemical inertness and corrosion resistance of gas regulators.
- How to manage moisture and particulate contamination in regulators.
|
Regulators may seem simple, but there's a lot going on inside that block of steel that can go wrong. Take a regulator apart and you'll see lots of parts, all of which are precision engineered components that, when not properly maintained, can cause loss of pressure control and result in increased maintenance or a potentially hazardous condition.
Learn how SilcoTek Coatings Can
Improve Analytical Results and Process Control
How to Prevent Gas Regulator Failures
The single stage regulator section drawing below shows that a typical regulator consists of lots of components parts. The wetted flow path (area below the diaphragm) can be compromised by environmental and internal process gases. The regulator body is not the only component to worry about. The diaphragm, poppet, seat, closing spring, and filters can all be problem areas if regulators are not properly maintained and specified.
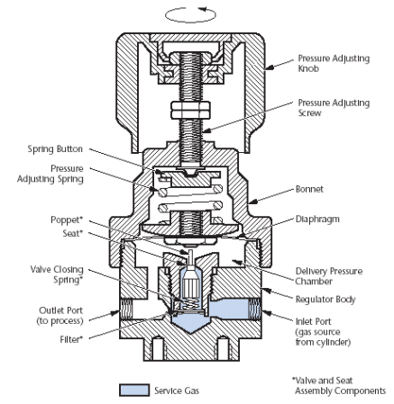
Preventing Regulator Failures
There are lots of potential problem components in regulators, what can I do to be sure I don't have a gas regulator failure? Stick to a defined maintenance plan.
Set up a maintenance plan to manage and prevent issues like calibration failures or gas pressure problems. Companies like Air Liquide, or Concoa offer general maintenance guidelines that are a good starting point for crafting your own gas regulator maintenance plan. The maintenance schedule from Air Liquide (below) is a good example of a general maintenance plan. Your plan should be tailored to your process environment and flow path conditions.
Maintenance Schedule
SERVICE
|
LEAK CHECK
|
CREEP TEST
|
INERT PURGE
|
OVERHAUL
|
REPLACE
|
Noncorrosive |
Monthly
|
annually
|
Not Applicable
|
5 years
|
10 years
|
Mildly corrosive |
2x Month
|
6 months
|
at shutdown
|
2 years
|
4 years
|
Corrosive |
2x Month
|
3 months
|
at shutdown
|
1-2 years
|
3-4 years
|
Taking Additional Steps
Chemical process, oil & gas, semiconductor, and analytical laboratories face problems specific to their industries, but all can benefit from taking some additional steps to improve regulator performance. Wise material selection, including inert, corrosion resistant coatings can improve regulator corrosion resistance, inertness, and moisture management. Here are some examples:
To get more information about how coatings can improve the performance of your products, subscribe to our emails and blogs by clicking the box below.

Preventing Process Corrosion
Often compressed corrosive gases like hydrochloric acid, ammonia, H2S, or HBr are anhydrous which generally reduces the risk of corrosive attack. Unfortunately, internal flow paths can be exposed to ambient moisture during cylinder changes which can dramatically increase corrosion and pitting which can impair performance or lead to failure. Pitted surfaces can be great hiding places for analytes or corrosives which can lead to carry-over. Selecting a corrosion resistant material like Dursan® to line the flow path will extend the life of surfaces by 10x or more. The hydrochloric acid example below demonstrates the improved corrosion resistance of a Silcolloy® or Dursan® coated surface. After 24 hours of immersion in 6M HCl, the stainless steel coupon is severely corroded with a very high 160 mpy corrosion rate. The Dursan coated test coupon shows minimal corrosion after the same exposure.
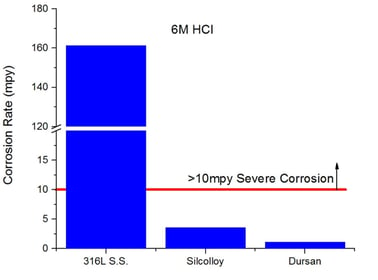
Inertness
Gases move through a somewhat tortuous regulator flow path which includes exposure to filters, seats, bodies, chambers, and diaphragms; all of which can adsorb reactive calibration gasses. VOC's, H2S, ammonia, and others can react with and be adsorbed by stainless steel or other alloy surfaces. This can impact calibration results, especially when calibrating low level or trace gas samples.
Get Our Ammonia Presentation
Lining the flow path and filter surfaces with SilcoNert or other inert coatings will minimize adsorption. Even sintered metal filters can be coated without significant impact to filtration or flow. The comparative ammonia adsorption study below shows that SilcoNert® 2000 coated stainless steel is less adsorptive and more inert than PTFE and PFA. Stainless steel surfaces are extremely reactive which can distort calibration results.*** Read the complete ammonia adsorption presentation.
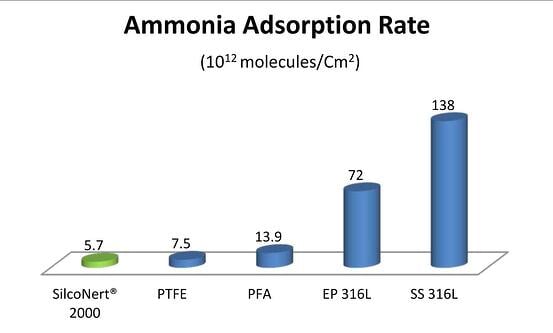
Freezing and Moisture Management
High flow, low ambient temperatures and moisture can result in freezing and failure of the regulator. Heated regulators or heat jackets will prevent freezing but won't address the underlying moisture contamination. Moisture can build up in flow paths, exacerbating freezing and increasing failure potential. Hydrophobic coatings like Dursan repel moisture and prevent build-up on the regulator body or other components, reducing purge time and making regular purge cycles more effective. The graph below compares stainless steel vs. hydrophobic Dursan moisture purge time. Saturated surfaces were dried at the same rate. The Dursan surface released moisture over 3x faster than the uncoated stainless steel surface.
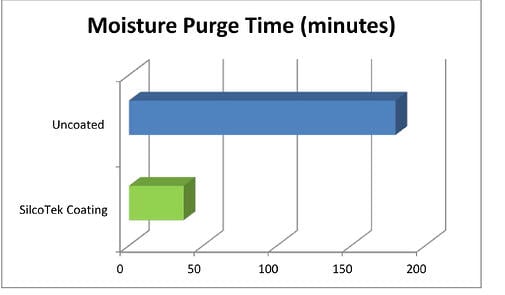
An Additional Layer of Ice Protection for Regulators
Like water repelling surfaces, icephobic surfaces can repel ice or slow the accumulation of ice and may add an additional protection against regulator icing. A surface ice repelling property can be attributed to the structure of the surface or low surface energy which results in low adhesion and easy removal of ice.
Low energy surfaces that prevent ice adhesion may provide substantial benefits for applications utilizing heat exchangers, as well as applications that are negatively affected by the accumulation of ice, such as regulators or instrumentation. SilcoTek® works with customers to solve adhesion problems. Our Dursan® and Notak® coating technologies lower surface energy, increase hydrophobicity and water repelling properties. Read our surface adhesion case study.
Evaluating surfaces using commercially available instrumentation is feasible but can be expensive, especially when initially screening surfaces for icephobicity. Although we do not have specific instrumentation to quantitatively test this property, we were able to devise a simple qualitative proof of concept test.
Testing the Surface
Using a standard food storage freezer (at 0°F / -18°C), a variety of SilcoTek® surfaces were placed in the freezer and 1-2ml of DI water dropped added to the middle of each room-temperature coupon. The coupons were enclosed within the freezer overnight. The next morning, a metal pick was used to laterally remove each ice ball from the coupon surfaces. The degree of removal difficulty was subjectively rated on a scale of 1-10 (1 = easy, 10 = difficult) with accompanying observations.
Notak® has a low surface energy of approximately 10.5 mN/m compared to an untreated 316 SS surface of approximately 45.8 mN/m. This low surface energy may allow ice to release from a Notak surface with little effort. Additional SilcoTek surfaces will be evaluated for comparative analysis.
SilcoTek's Technical Service and Research and Development Team are here to advise and help customers select and test coatings that best fit your application. Contact our team to discuss your application it's free!

Data and Discussion:
Coupons of various SilcoTek surfaces (and an uncoated control) were placed on a rack within a commercial freezer at 0°F / -18°C. Upon placement, approximately 1-2ml of DI water was dropped on to the center of a coupon. The coupons resided in the freezer with the door closed for 16 hours.
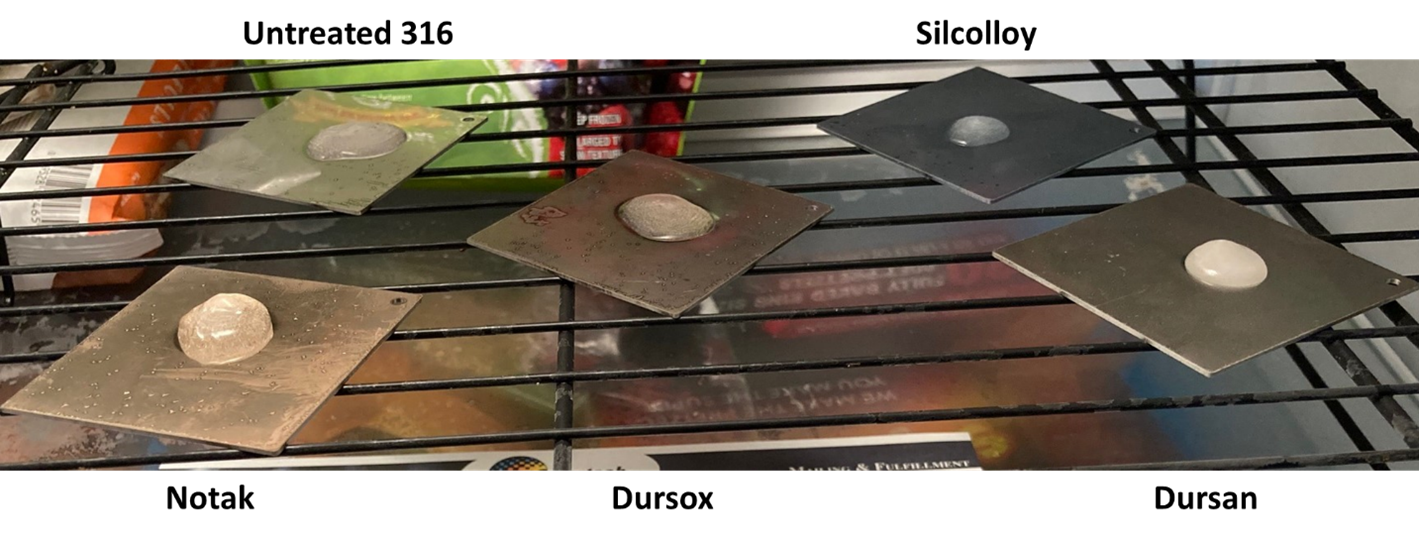
Upon opening the freezer door (see photo), each coupon was individually removed and rapidly tested to avoid the potential impact of thawing. A metal pick inserted at the point of ice attachment to the coupon was used to laterally remove the ice. The effort required (1 = easy, 10 = difficult) to remove the ice and associated observations are listed in the table below.
316 SS Coupon Surface
|
Effort (1-10)
|
Observations
|
Notak
|
2
|
complete removal with little effort
|
Dursan
|
6
|
partial removal from surface with effort
|
Silcolloy 1000
|
7
|
partial removal from surface with greater effort
|
Dursox
|
8
|
difficult, bulk chipped with minimal surface separation
|
Uncoated
|
8
|
difficult, bulk chipped with minimal surface separation
|
How do I get a surface to match my desired moisture level of moisture resistance?
You don't have to make a super radical change to material or product construction in order to change the moisture performance. Fortunately we offer silicon barrier coatings with a wide range of water management capabilities.
Want a more corrosion resistant or inert coating with a low surface contact angle? Try SilcoNert® 1000 or Silcolloy®. If you're looking for an inert coating that's not too moisture repelling, go with SilcoNert® 2000. Need a hydrophobic coating or superhydrophobic coating? Dursan® or our new Notak surface may do the trick. Have a fouling problem? Learn more about solving fouling problems.

Note, our Notak coating is in pre-production Beta testing so we have limited capacity for that coating. Contact our Technical Service Team to discuss your application and we'll be happy to make a coating recommendation.
Particulate management
Particles in the flow path can interfere with gas regulation. The solution is to install a fritted metal filter in the flow to capture particles. Unfortunately the extreme surface area in filters can react and adsorb calibration gas samples and distort calibration results. Don't throw out that filter and risk particulate damage, treat the filter with SilcoNert® or Dursan® to prevent adsorption, improve corrosion resistance and keep the flow path particulate free.
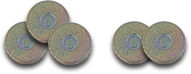
Get coated products
SilcoTek® offers coating services but we also team up with manufacturers to make it easy for the customer to buy coated products. Go to our web page to find manufacturers offering coated products. Or contact our Technical Service Team to discuss your application.
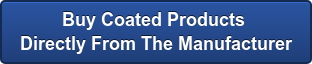
*Image credit: Air Liquide. https://industry.airliquide.us/single-stage-versustwo-stage-regulators
** Image credit: ASGE. http://www.asge-online.com/Regpg21.html
***Data credit: Olavi Vaittinen1,Markus Metsälä1, Stefan Persijn2, Markku Vainio1,3 and Lauri Halonen1
1 University of Helsinki, Finland
2 VSL, The Netherlands
3 MIKES, Finland