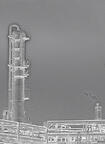
Customers experiencing material contamination and sampling reliability issues frequently ask: “Is there any data concerning the life span of the effectiveness of inert, SilcoNert 2000 coating (i.e. does its efficiency decay over time)? Replacing chromatograph columns isn’t a big job, but replacing 100 metres of sample tubing routed high up among the pipe-work would be a major headache.”
The biggest consideration regarding contamination and sampling reliability would be how “dirty” the sample materials are.
If there is a lot of particulate coming into the line, then cleaning would be needed to remove contaminants. If these particulates build up, they could be adsorptive. Once, they are rinsed out, the SilcoNert 2000 coating will be fine and sampling accuracy and reliability will be restored (unless there is abrasion/erosion that has compromised the coating).
Another area of potential poor reliability is the accumulation of moisture in sampling systems. If there is any point of condensation in the system and there are acids or bases that form in water from the sample stream/water contact; the subsequent corrosive attack and reactivity of the acid/base will decrease the coating life and adversely impact sample reliability. We have seen systems in which the SilcoNert 2000 coating is performing well but a cold spot in the heat trace tubing resulted in moisture condensation and HCl or Sulfuric acid formation. The acid then attacked the coating and tube surface, eventually eating a hole (in the layer and the tubing) and creating active iron particulates.
For most applications sample lines will last many years. A study by BP, presented at the 2011 ISA-AD Conference in Houston, TX, highlighted a SilcoNert 2000 coated flare gas sampling line that had been working great for 2 years. This is a very dirty application with the potential of many contaminants and failures; however, with first-rate design and maintenance, the system continues to provide accurate, reliable sampling results. Keys to reliable sampling are:
- Eliminate potential cold spots in heat trace tube.
- Proper installation, avoid dips or areas for moisture accumulation in tubing.
- Install filtration, avoid build up of active particulates.
- Proper material selection for the environment.
- Inert coatings
- Materials specified for the sampling environment.
- Proper coating selection for the sampling application:
- SilcoNert 2000 for low level sulfur/H2S sampling.
- Dursan for extreme environments (acid/base exposure, particulate abrasion, etc).
For design and installation pointers, ask the heat trace companies about their experiences with installing and servicing lines used in your application. SilcoTek works extensively with O’Brien Corporation www.obcorp.com and Thermon Manufacturing Company www.thermon.com . They are the market leaders and have a great deal of technical expertise and experience with installation and maintenance of reliable sampling systems.