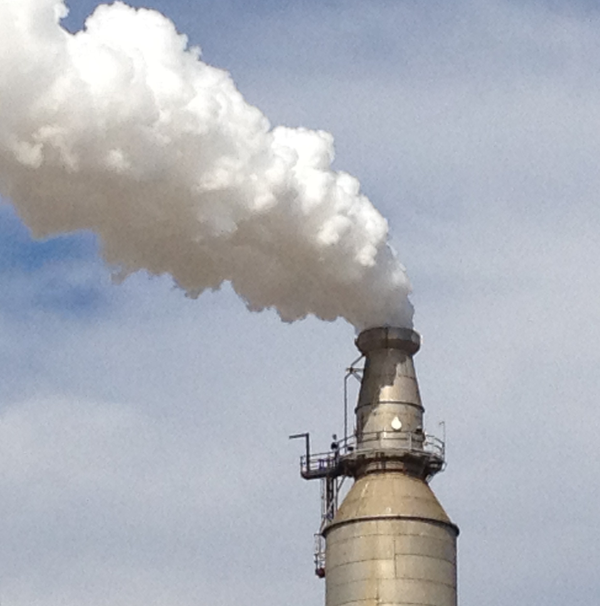
Want to improve your product, process sampling or emission monitoring (CEMS) process? Here are some ideas on solving contamination and reliability problems.
Customers experiencing material contamination and sampling reliability problems frequently ask: How can I improve flow path inertness and sample system reliability? Replacing chromatograph columns isn’t a big job, but replacing 100 meters of sample tubing routed high up among the pipe-work would be a major headache.” In this blog we'll discuss factors that improve process sampling and CEMS emissions monitoring.
In this blog post you will learn:
- How maintaining sample flow path integrity, inertness, and cleanliness prevents test and process failures
- How moisture contamination can impact sample quality
- Learn about keys to reliable sampling
- Get sources on proper heat trace tubing installation
|
1. Sample integrity
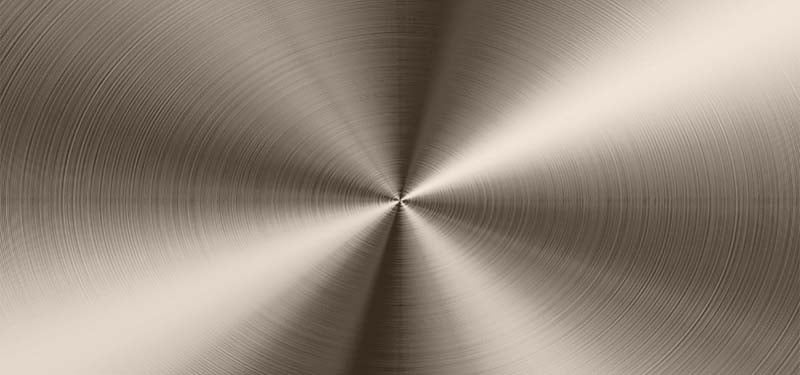
The biggest consideration regarding contamination and sampling reliability would be sample condition. How dirty or clean is the sample stream? If there is a lot of particulate coming into the line, then cleaning would be needed to remove contaminants and sample filtration is needed. If sample particulates build up, they could become adsorptive and degrade test results. Once particulates are removed, an inert coating should be applied to the entire flow path to minimize particulate stiction and sample adsorption. Never clean an analytical sample flow path with steam. Steam, especially process steam systems, contain particulates that will adsorb test samples and disrupt system calibration. Particulates can also damage inert coatings if used in the flow path.
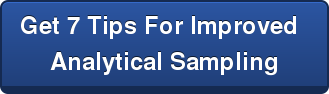
2. Manage Moisture
Another area of potential poor reliability is the accumulation of moisture in sampling systems. If there is any point of condensation in the system and there are acids or bases that form in water from the sample stream/water contact, the subsequent corrosive attack and reactivity of the acid/base will decrease the coating life and adversely impact sample reliability. Poorly designed or installed systems can form a cold spot or dip in the heat trace tubing which resulted in moisture condensation and accumulation. HCl or Sulfuric acid formation can result. The acid can attack the tube surface, eventually eating a hole (in the inert coating layer and the tubing) and creating active iron particulates and ultimately tube failure. Manage moisture by coating the surface with an inert, hydrophobic coating to reduce the surface energy and increase moisture repelling properties. The graph below compared H2S stability of wet vs. dry sample environment. After 14 days, the wet environment had 18% less H2S in the sample.
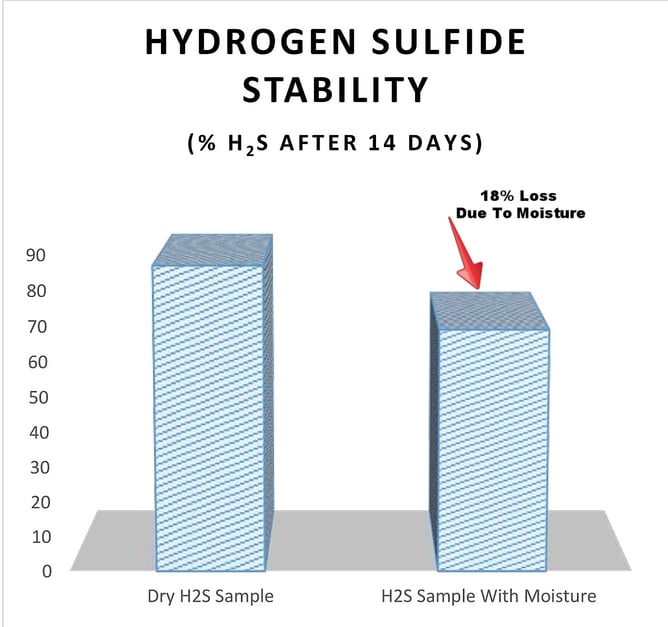
3. Keys to Reliable Sampling
For most applications a well-designed sample system featuring an inert coating will last many years without issue. A study by BP, presented at the 2011 ISA-AD Conference in Houston, TX, highlighted a SilcoNert® 2000 coated flare gas sampling line that had been delivering accurate results without issue for 2 years. This is a very dirty application with the potential of many contaminants and failures; however, with first-rate design and maintenance, the system continues to provide accurate, reliable sampling results.
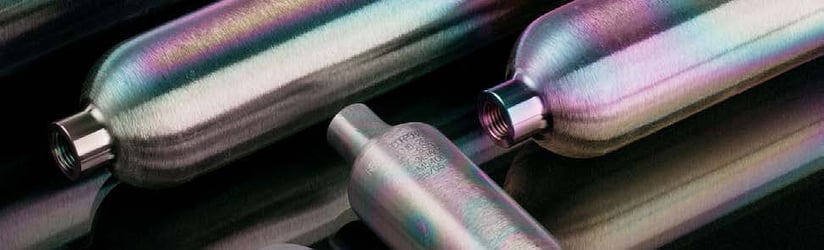
Keys to reliable sampling are:
• Eliminate potential cold spots in heat trace tube.
• Proper installation, avoid dips or areas for moisture accumulation in tubing.
• Install filtration, avoid build-up of active particulates.
• Proper material selection for the environment
- Inert coatings
- Materials specified for the sampling environment
• Proper coating selection for the sampling application:
- SilcoNert® 2000 for low level sulfur/H2S sampling
- Dursan® for extreme environments (acid/base exposure, particulate abrasion, etc)
3. Heat Trace References
For design and installation pointers, ask the heat trace companies about their experiences with installing and servicing lines used in your application. SilcoTek® works extensively with O’Brien Corporation and Thermon Manufacturing Company. They are the market leaders and have a great deal of technical expertise and experience with installation and maintenance of reliable sampling systems.
There's lots more to learn about process monitoring, sampling and sample transfer. Get our e-book series.
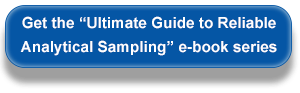