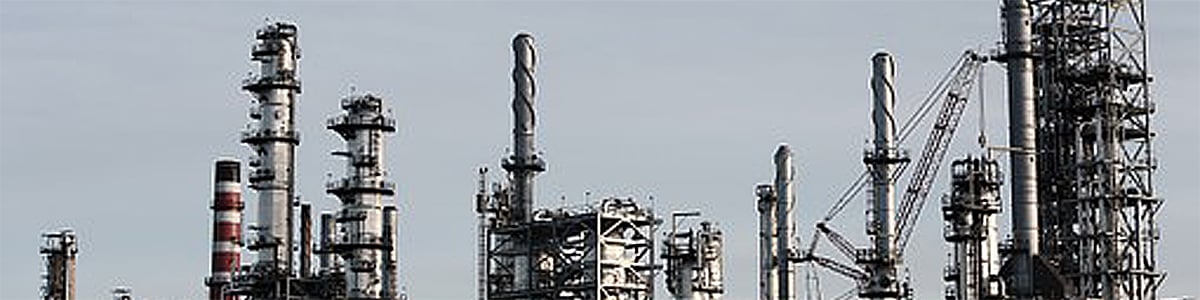
Get tips on preventing analyzer sampling system failures and learn how to keep process analytical and sampling systems running at peak performance and save money!
Preventing Analyzer Sampling System Failures (CEMS)
Sample transfer systems may seem to be a relatively straightforward affair. After all you're only transporting a sample from point A to point B through either tubing or some container such as a sample cylinder. Unfortunately the reality is that "simple" transport system can hold a lot of potential for analytical quality problems. Let's discuss how to minimize those problems and improve the effectiveness and reliability of sample transport systems.
In this blog post you will learn:
- Get tips on steps you can take to prevent analyzer flow path system failures
- Learn how to improve flow path corrosion resistance
- Learn how to prevent flow path adsorption and reactivity
- Learn how inert nano coatings can improve flow path inertness and corrosion resistance and prevent analyzer sample system failures.
|
Examples of Sample Transport Problems
Sample transport problems can be caused by multiple issues. Dips in heat trace tubing can cause pooling and sample loss. Reactive metal filters can trap and hold onto a sample by reacting with compounds. Corrosion and particulates can adsorb analytes. Other transport problems can range from probe or tube fouling, unintended sample phase change (condensation, freezing, etc.), low flow problems, surface reactivity and adsorption, moisture contamination, damage to system components due to corrosion and the list goes on! That's why there are lots of systems that are in critical condition and require frequent maintenance or replacement. Especially systems located in coastal areas or systems exposed to corrosive environments.
Robust system design, a solid maintenance plan, and proper material selection will improve performance and process control while assuring regulatory compliance. Working with specialists in heat trace installation will help to avoid common design errors. But material selection can't be dictated by a software program, proper selection will require input from in house process engineers, technicians and sample system design engineers; the people who know the plant conditions the best.
Get our e-book: 7 Tips For Improved Analytical Sampling
Selecting the right material for the application.
Moving a sample from point A to Point B requires some form of conveyance be it a sample cylinder carried by your feet to the GC or via tubing connected to a continuous emissions monitoring system (CEMS). No matter the transport method, the material a sample comes in contact with during that trip matters. The go-to materials for sample transport are PTFE and stainless steel, but before reaching for those options, you need to consider the sample environment, the nature of the sample being taken, the desired result and cost.
Need help selecting the right coating for your analytical or process application? Go to our coating selector. The automated selector will ask you a few questions about your application and will then suggest a coating that best fits your need. The whole process will only take less than a minute. Give it a try!

Environmental Considerations
Many sample transport systems utilize PTFE components, tubing, or liners to assure an inert flow path. However PTFE may not be the best choice in many process analytical environments. Plant conditions to consider range from the temperature of the sample environment, exposure to corrosives, potential for damage or abrasion, and the potential for cold shock or rapid temperature swings.
Some sample systems must maintain a steady temperature that comes very close to the maximum temperature of PTFE (250°C). Even if temperatures are relatively cool, say 120°C, PTFE can become soft and deform or "cold flow", resulting in collapse of flow path liners or tubing failure. Extreme cold can embrittle PTFE which can also lead to failures. Super inert coatings like SilcoNert® and Dursan® can withstand high temperature exposure up to 450°C while silicon coatings like Silcolloy® remain intact at temperatures over 1000°C.
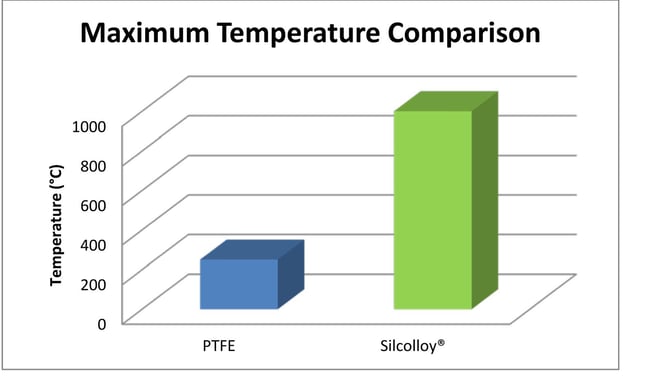
Corrosion resistance
Stack and flare Industrial process samples (like from stack and flare emissions) often contain acids such as sulfuric acid or hydrochloric acid. Even low level exposure can pit tube or sample cylinder surfaces and eventually lead to system failure. Pitted surfaces can also be great places for trace amounts of moisture and analyte to hide. This can result in sample carryover or moisture solvation of the sample.
How to fix the problem?
Inert coatings can improve corrosion resistance of stainless steel, helping to achieve an affordable, high durability, corrosion resistant and inert surface. Comparative analysis of immersion studies of stainless steel, and SilcoTek coated stainless steel coupons in 25% sulfuric acid show an order of magnitude decrease in corrosion for the Dursan coated surface.
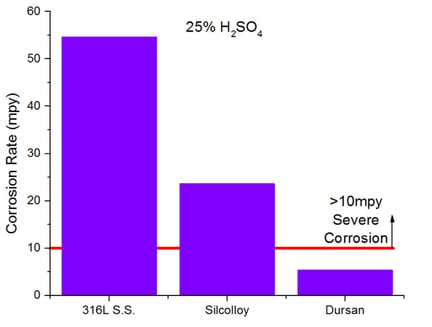
Abrasion and Wear Resistance
Abrasive samples can quickly damage PTFE and other soft surfaces. Filtration of the sample can help protect the tube or sample cylinder surface but designers should be mindful of potential damage caused by abrasion or simple rough handling by installers and technicians.
Watch our video and see how abrasion can damage flow path surfaces.
Know the Sample
It sounds obvious, you're sampling for whatever is specified say VOC's or H2S. That's all I need to know right? Sorry, you'll need to know lots more including:
- Sample phase (don't change from gas to liquid during sampling, or visa versa...)
- Corrosive compounds in the sample
- Moisture content
- Sample temperature and pressure
- Can potential compounds in the sample react with the flow path materials, including seals?
Know the expected concentration range of the sample when sampling in analytical applications. For example a 20% H2S sample will need a more robust flow path vs. a 20 ppb sample. Conversely, surface reactivity will have a greater relative impact on the 20ppb sample. A 10 ppb loss due to flow path adsorption results in a 50% loss to the trace sample but a negligible impact to the 20% sample.
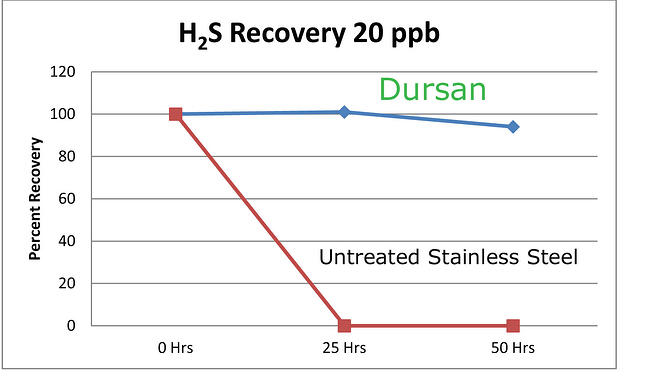
Desired results
Are you taking a quick grab sample for a maximum allowable value? Are you calibrating the system for ultra low level analysis? Or are you speciating a sulfur sample? Knowing where you're going with the sample system performance is key to the material selection and ultimate system performance. Conversely, don't expect a sample system designed for sampling 20% H2S to magically be capable of accurately and reliably sampling H2S at 20ppb. Hint, you'll never see the 20ppb sample. In fact reactive samples can be adsorbed by stainless steel, alloy, glass, ceramic or elastomer surfaces on contact. Often a trace sample when held in an untreated sample cylinder will be completely lost due to adsorption.
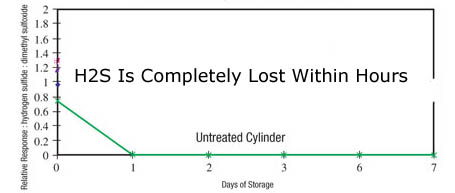
Cost
Cost control is always a major factor in when considering flow path material options. Designers should consider not only the initial system cost, but also the total operating cost over the life of the system or project. A quick calculation will prove that frequent repairs to a system or calibration problems resulting from sample adsorption will quickly eat up any potential short term savings realized by utilizing less expensive, more reactive materials.

Material Reference
Confused about choosing the best material for an analytical flow path? Here's a quick comparison of material advantages and limitations for sample transfer applications. Or you can contact our Technical Service Team and we'll be happy to discuss your application. Or try our Product Selector Guide.
Material |
Advantages |
Limitations |
Stainless Steel |
Low cost, durable, high/low temperature capable |
Reactive, lower corrosion resistance |
PTFE |
Corrosion resistant, inert, low cost |
Permeable, easily damaged, low melting point |
Super Alloys |
Corrosion resistant |
Expensive, limited availability, reactive surface |
Inert Coating, Dursan, SilcoNert |
Corrosion resistant, inert, durable, temperature capable |
Can be damaged by severe base exposure. Abrasives can damage over time. |
Want more tips on improved surface inertness and better analytical results?
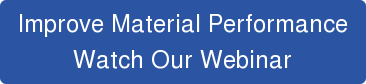