This week, we're talking about the 4th and final book in our Ultimate Guide E-Book series, entitled Troubleshooting and Protecting the Sampling System. Over the last few months, we've done blog posts on book 1, book 2, and book 3. In this book, we're going to talk about the impacts of corrosion, contamination, particulates, and cleaning your inert sample system.
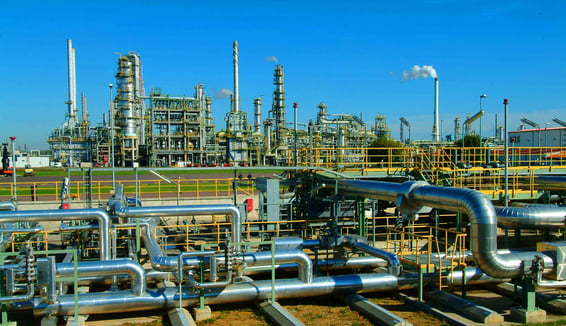
Download and read the entire book:
Tips for Solving Sample Cylinder Inertness Problems
Tip 1: Check for Corrosion 
Here are a few signs that the sample cylinder may have a corrosion problem.
- Loss of analyte. Test results or calibration test is showing lower than expected test results.
- Qualification sample not consistent.
- Particulates in sample stream.
- Liquid in what should be a dry gas sample stream. This could be condensation or acid build-up in the sample cylinder. Both can result in corrosion.
- “Off color” liquid flowing from the sample cylinder.
Tip 2: Check for Contamination 
Here are a few signs that indicate the sample cylinder may have a particulate problem:
- Loss of analyte, adsorption. Test results or calibration test is showing lower than expected test results.
- Qualification sample not consistent.
- Particulates in sample stream. Particulates found in filters.
- Sample cylinder valves are not operating smoothly or have particulate build-up.
- Reduced sample cylinder flow or clogging. Extreme particulate build-up!
Tip 3: Cleaning may be the Culprit 
Signs a sample cylinder may have a surface film problem:
- Loss of analyte, adsorption. Test results or calibration test is showing lower than expected test results.
- Film on interior of sample cylinder valve.
- Extremely dull appearance on interior surface of sample cylinder. Note that interior surfaces are rough, so the surface will inherently not be shiny.
- Film on sample cylinder swab.
Tip 4: Avoid Steam Cleaning 
Steam will not necessarily damage a SilcoTek-coated surface, but it can change the surface chemistry and render the coating less inert. Steam particles can adsorb compounds, causing unreliable results. Try mild sonication in water or an appropriate solvent or flushing the surface/flow path with a solvent or inert gas like nitrogen to remove particulates.
Tip 5: Stainess Steel is Reactive! 
Assuming you coated the sample cylinder with SilcoNert® or Dursan® inert coatings, the problem may be other exposed stainless steel surfaces. Did you coat the entirety of the valve’s flow path? Maybe you missed coating the fritted filter? Or, was it that short length of uncoated transfer tubing? Even the smallest uncoated surface area can impact sample integrity, especially when testing trace amounts of a reactive compound like H2S or mercaptans.
Solving Sample Transfer Problems
Stack and flare emission monitoring can be a challenge. Changing sampling environmental conditions, exposure to corrosives, and high temperatures lead to frequent system failures and data quality problems. Often the failure can be traced to the sample transfer flow path. Here are tips on how to improve reliability and solve emission monitoring problems in stack and flare sample transfer systems.
The first step in mitigating the effects of a reactive surface is to be sure the sample flow path is inert. Inspect and confirm all components in the flow path are coated with an inert surface like SilcoNert or Dursan. A single uncoated reactive component can distort sample results or cause complete loss of the sample at part-per-million levels.
The test comparison below demonstrates the rapid loss of a reactive sample when exposed to stainless steel. The uncoated 300cc sample cylinder quickly loses the H2S sample while the Dursan coated sample cylinder does not adsorb the H2S sample over the duration of the test.
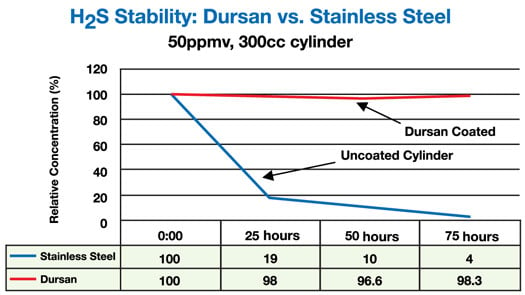
Check for Contamination
If all surfaces are coated, confirm the flow path is free of particulates, corrosion and moisture. Rust particles can quickly adsorb reactive substances. Moisture can solvate the analyte and distort test results and can facilitate system corrosion. Finally check the cleaning protocol. Some solvents can leave a reactive film or damage the SilcoNert or Dursan surface. Steam cleaning can contaminate the system with particulates and also damage the surface under some conditions.
Check for Stack and Flare Probe Damage
Probes are exposed to high temperatures, corrosives and abrasion, making them a source of continuous maintenance and possibly sample loss due to adsorption. Coating the probe with an inert, high durability coating like Silcolloy® or Dursan® will improve high temperature oxidation resistance, abrasion resistance, and corrosion resistance. An inert, corrosion resistant coating can protect the probe and improve corrosion resistance by 10x or more. The example below shows the Dursan- and Silcolloy- coated surfaces resist sulfuric acid damage, while the uncoated stainless steel quickly corrodes. A coated probe will reduce maintenance and prevent sample adsorption, making a more reliable sample system.
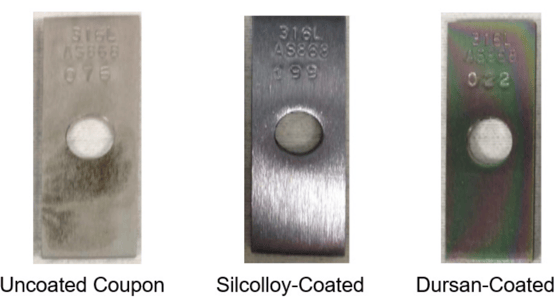
Comparing the acid color after 312 hours of immersion is an easy-to-tell indicator of potential process contamination from metal leaching into the acid solution. The uncoated coupon acid solution (left) is green, showing severe metal contamination from the coupon. The Silcolloy acid solution (center) is clear, showing little contamination. The Dursan acid solution (right) shows some attack and contamination, but at a rate significantly less than the uncoated coupon.
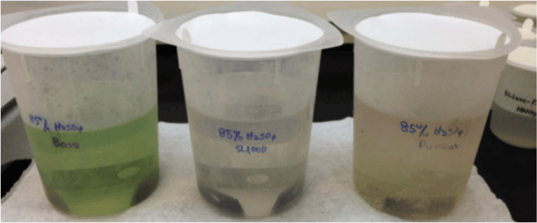
Comparing the data (below), the uncoated coupon corrosion rate, 3.53 mills per year, is 20x greater than the Silcolloy-coated coupon. The Dursan coupon showed a slightly higher corrosion rate, but significantly less than the uncoated coupon.
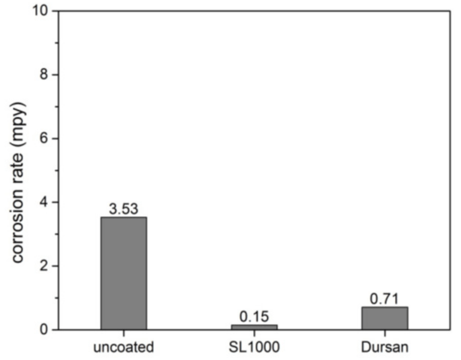
Improve Sample and Transfer Reliability in Process and Analytical Systems
Process analyzers and process sampling systems are exposed to challenging environments both internally and externally. Many sample streams are corrosive or contain active compounds that reduce equipment lifetime or require extended preventative maintenance. Instrumentation and sample flow paths can be exposed to extreme temperatures, rough handling by operators and abrasive materials; all can severely damage the analyzer flow path.
The combined extreme environments found in refinery, petrochemical, and process monitoring can lead to frequent system failures and costly maintenance; ultimately leading to poor yield, off spec product, or regulatory compliance issues. Improving sample system reliability is a key factor in the success of plant processes, making the right material selection and optimizing sample system performance all the more critical.
Improving Heat Resistance
Heat trace sample lines, reactors, regulators and other sample system components are often run at elevated temperatures in order to prevent condensation and preserve analyte integrity. Unfortunately, common inert materials like PTFE are not appropriate for elevated temperature applications. The graph below demonstrates how increasing temperature above 464° F will result in outgassing of fluoropolymers into the flow path.*
*Chart courtesy of http://www.mindfully.org/Plastic/Teflon/Canary-Teflon-ToxicosisAug03.htm
Additionally, PTFE can “cold flow” at temperatures well below the outgassing temperature, causing flow path obstructions and sample system failure.
The Solution
Use a high temperature silicon coating to improve high temperature durability. Use the recommended maximum temperature table below to select the right coating for the right temperature. Inert silicon coatings can withstand temperatures up to 800° C, making silicon coatings ideal for stack and flare sampling applications.

High Pressure Capability
Sampling oil & gas upstream and downstream systems often expose system components to high pressure gas and liquids. High pressure sampling can stress and expand sample cylinder and tube walls. Consequently, inert flow path surfaces must be flexible in order to withstand the stress of expansion cycles and remain intact.
Improving Corrosion Resistance
Sampling systems in coastal locations can be exposed to sea water or salt spray which causes rapid deterioration of equipment, requiring more money to keep them operating. For systems that are required to give accurate, reliable and repeatable data in such conditions, the cost of upkeep and maintenance is much larger than systems in more benign environments.
The exceptional chloride resistance of silicon CVD coatings like Dursan® can prevent salt-related corrosive attack. The 4000 hour salt spray comparison below demonstrates the improvement a protective coating can have on sample transfer systems. The uncoated test coupons (left) show significant corrosion while the Silcolloy®-coated coupon shows very light rust spots. Dursan®-coated coupons remain corrosion-free.
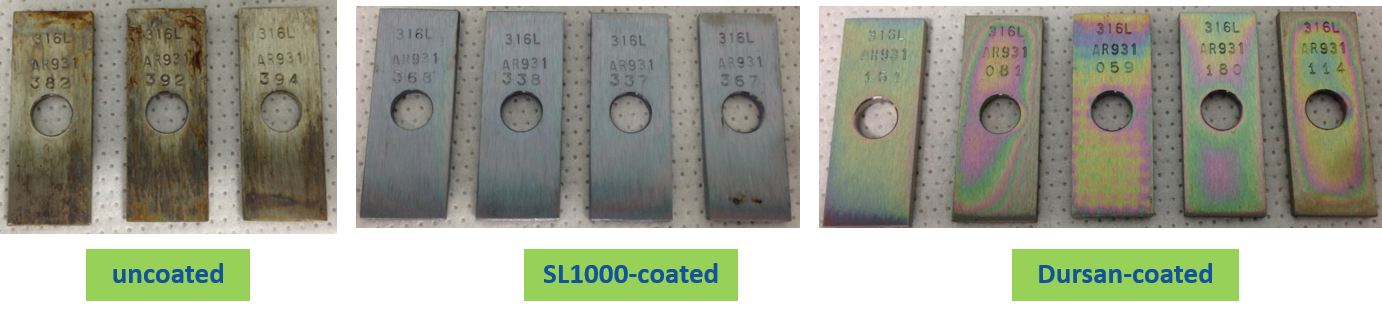
Other chloride containing streams can greatly reduce the lifetime of process systems. The corrosion graph below provides the results obtained from ASTM G31 testing of common sample flow path materials. The immersion test in a 6M HCl (18%) solution at 50° C and atmospheric pressure can quickly damage stainless steel surfaces. Dursan-coated stainless steel performs at levels comparable to high-quality super alloys, reducing corrosion rate from 3116 mills per year to 23 mpy.
After immersion, differential weighing allows the amount of material loss to be determined. The amorphous silicon-coated stainless steel shows greater than 20 times the resistance of non-treated stainless steel in these environments.
Improving Wear Resistance
The table below summarizes the data obtained from wear studies conducted on both non-treated and treated surfaces. Data was generated using a pin-on-disk tribometer (Nanovea, Irvin, CA). The experiment uses a flat plate loaded onto the test rig and an indenter which applies a precise force to the surface. The plate is then rotated and forces are measured between the pin and the disc.
Pin on Disc; 2.0N |
316 Stainless Steel |
Carboxysilane Coating 316SS |
Silicon Coated 316SS |
Wear rate (x10-5 mm3/Nm) |
13.810 |
6.129 |
2 |
Improvement Factor over SS |
--- |
2 times |
1/3 times |
Results from this experimental method can produce wear behavior and friction coefficients of the plate surface 1. Results from this study demonstrate that the carboxysilane coatings (Dursan®) wear less than untreated steel and silicon coated surface. The improved wear resistance as a result of the coating will lead to longer lifetimes of system components in extreme environments.
Reducing Leak Rate
SilcoTek surfaces maximize the performance of vacuum systems. Comparative studies show how SilcoTek-coated surfaces can reduce pump down time by up to 3X or more. The result? Coated UHV surfaces improve system productivity while preventing contamination from stainless steel flow paths. SilcoTek-treated vacuum chamber surfaces achieve a lower base pressure significantly faster than uncoated surfaces, saving time, improving productivity and reducing process cost.
Coating Care: Do's and Don'ts of Maintaining an Inert Coating
- Select the right coating for the application
- Keep it clean
- Don't get steamed
- Don't exceed the pH range
- Install filters in the flow path
Conclusion
We've discussed how our inert coatings can help your sampling systems to perform at their peak and maintain that level of reliability long after the typical life-span. Start improving process sampling now! To recap, this E-book focused on:
- the impact of corrosion, contamination, particulates, and cleaning on sample cylinder and sample system inertness performance.
- Ways to prevent sample system damage and improve system response.
- How to improve sample system reliability.
- The impact of uncoated stainless steel on sample system analytical performance.
- How to care for and maintain inert-coated surfaces.
Have questions about our coatings? Let's talk!
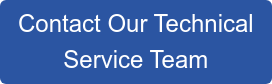