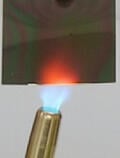
Analytical systems are assembled using many types of joints ranging from compression fittings, VCR, VCO, up to KF and conflat flanges. In order to make a system inert and to assure a consistent and thorough coating throughout the system, we ask customers to send in parts disassembled.
SilcoTek will then coat the individual components and then ship the parts back to the customer for assembly into an inert high performance analytical system. But often individual components are assembled with brazed or soldered joints. Can SilcoTek make a brazed or soldered joint inert or corrosion resistant? And is one joint better than another in regards to coating quality and analytical performance?

The short answer to "can we make a a solder or brazed joint inert or corrosion resistant" is a qualified yes. OK I'll stop dancing around the issue and give you the longer version of what type joint is coatable.
Some Background About Brazing And Soldering
There are three main concerns when considering whether a brazed or soldered joint is coatable:
- Will the joint physically survive the heat exposure of our process?
- Will the solder/braze material contaminate SilcoTek processing systems (vessels / lines / other customer parts)?
- Will the joint area meet customer quality requirements for appearance and performance. This is a critical concern because the solder/braze joint area may appear "hazy" or cloudy after processing.
It's always best to consult with the customer to communicate what we know, & what we don’t know about potential coating issues, and to establish proper customer expectations before coating parts.
Brazing and soldering are typically defined by the melting temperature of the filler material:
- brazing joints are rated to withstand temperatures over 450°C.
- solder joints can fail above 370°C.
One common misnomer, however, is “silver soldering”. Typically, silver soldering is actually a silver braze process and should withstand temperatures of 450°C.
Brazing: An excellent primer on brazing can be found in the Oerlikon Brazing Guide. Brazing is a joining process where metals are bonded together using a filler metal with a lower melting point than the base material. Heat, via torch or furnace, is used to liquefy and allow the flow of filler metal (via capillary action), which then cools, solidifies, and joins the base material. Additional materials, such as flux, may be used to prevent the accumulation of oxides and other undesirable contaminants in the filler metal.*
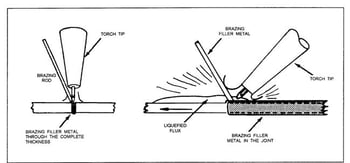
The following materials may be present in filler metal. Formulation is highly variable and unique between most suppliers:
Possible Base Materials: Nickel, Cobalt, Silver, Gold, Aluminum, Copper
Possible Alloying Materials: Nickel, Cobalt, Manganese, Boron, Silicon, Iron, Chromium, Tungsten, Aluminum, Copper, Molybdenum, Carbon, Titanium, Niobium, Germanium, and Rare Earth elements such an Lanthanum, Yttrium, etc.
The presence of some of these materials in higher concentration may pose a reason for concern. For example, we know that high levels of copper can cause contamination issues with our processing systems and affect the inertness of the coating, particularly SN2000.
Soldering: The soldering process has similarities to brazing but is generally a less challenging process. Solder filler material may have some of the same materials as found in braze materials, such as silver and copper, but it is also alloyed with metals such as tin, bismuth, indium, zinc, antimony, gold, lead and manganese to yield lower melting points (lead is being phased out but is still available). **
The Bottom Line

Brazing OK.
Recommendations for Braze Joints:
- Most braze joints are compatible with our process temperatures
- Most braze joints will not cause contamination issues
- The most preferred braze method is Vacuum Nickel Brazing. This joining method is highly compatible with our process and does not show cosmetic hazing. This is the joining method typically used by our collaborators at Solar Atmospheres Inc. Titanium brazing, although not as popular, also coats well.
- For high copper-containing filler material, a general recommendation is to follow our current existing guidelines on copper-containing base materials. The level of copper can be determined by use of our XRF alloy detection gun.
Solder not OK unless it's a high temperature solder.
Recommendations for Solder Joints:
- Because of the low melting temperatures of solder, it is not recommended to process parts joined by this method. The presence of filler materials that allow for low temperature soldering (tin, lead, and zinc) can result in joint failure and system contamination. There's always an exception, see below.
- However, the presence of the above materials is not necessarily a smoking gun for a low temperature solder joint. It's best to contact the customer and confirm whether the joint is soldered or brazed, and if they know the temperature capability of the joint.
- “Silver soldered” is typically not soldered, but is brazed. Most “silver solder” joints will survive our processing, but the coating will appear hazy around the joint after deposition.
With a proper joint, the entire analytical flowpath can be successfully coated. The result? More consistent test results, less analytical time and improved profits!
Want more tips on how to improve analytical sampling, processes and products? Get 7 great tips on how to improve anaytical sampling.
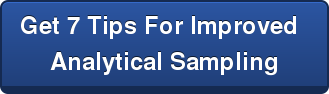
*Image courtesy of http://www.free-ed.net.
** Image courtesy of http://canada.newark.com/solder-and-soldering-guide