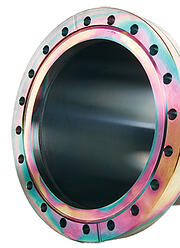
Protecting sealing surfaces like conflat flanges, VCR glands, and compression fittings from corrosion and keeping them inert is important to maintaining sample transfer system integrity. Corrosive attack around seal areas can dramatically shorten the life of process systems while particulates generated from internal corrosion can result in contamination of process fluids and will increase surface reactivity.
It makes sense to consider using inert, protective coatings in seal areas. But questions arise concerning coating surface durability. Can SilcoTek® inert coatings withstand sealing stress while remaining leak free? Let's find out.
SilcoTek® coatings are proven to withstand compression and shear stress common to CF, face seal and threaded systems. That gives customers a new option when looking for improved corrosion resistance, durability, and inertness in sampling and process systems.
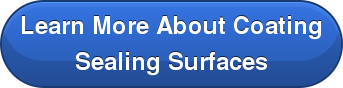
Let's see how a coated face seal stands up to the stress.
First we'll examine the coated surface before sealing.
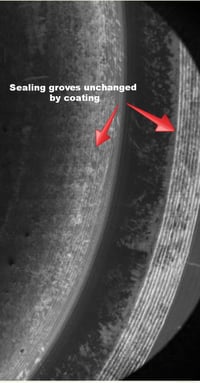 |
FESEM (Field Emission Scanning Electron Microscopy) image of the coated pre-sealed surface shows the coating conforms to the sealing area. The raised surfaces of the gland area can be seen. SilcoTek® coatings conform to surface contours and small orifices. |
Now let's make the fitting, disassemble and examine the surface.
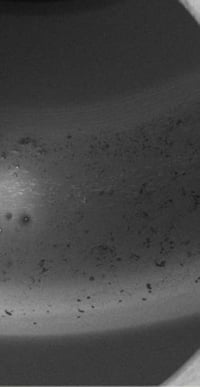 |
After making the metal-to-metal fitting per manufacturers instructions, a second FESEM image of the surface shows no scarring or scratching, only trace particulate from the silver gasket. |
Let's scan the fitting to be sure the inert, corrosion resistant silicon surface is really intact.
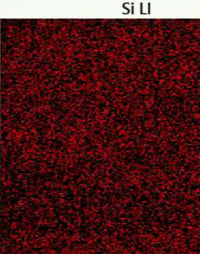 |
EDS (Energy Dispersive Spectroscopy) is used to map the distribution of silicon throughout the area. Post sealing results show the silicon surface remains intact with no major occlusions or scratches on the surface; assuring a leak free, inert and corrosion resistant surface. |
Finally let's do a leak test.
For this experiment, we'll compare coated and uncoated CF vessels under heating. As the temperature rises, leaks and surface outgassing can also increase. SilcoTek®coatings maximize leak integrity with a very low outgas rate compared to uncoated stainless steel surfaces, even under ultra high vacuum conditions.
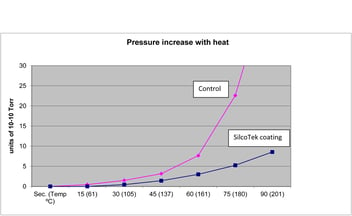
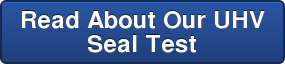
The benefit
Resistance to common corrosives like nitric, sulfuric, & hydrochloric acid is improved by up to 10x or more. Coated seal areas help prevent crevice corrosion as seen in the example below.
ASTM G48 ferric chloride immersion testing shows major crevice corrosion on uncoated 316L stainless steel coupon. Corrosion resistant coatings minimized the damage to the second coupon (bottom image).
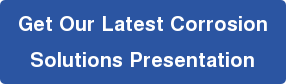
Make that seal inert!
Sticky compounds like proteins can hide in seal areas. An uncoated fitting can also react or adsorb sulfur, ammonia and other active or reactive compounds. SilcoTek inert barrier coatings prevent interaction with surfaces, making the fitting or seal area non reactive and non stick.
Dursan® coated stainless steel prevents protein sticking, allowing easy rinse of molecules and preventing carryover and cross contamination of samples.
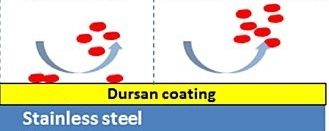
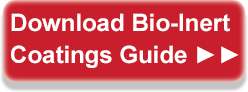
Dursan® coated fittings do not adsorb active compounds. Even after multiple cycles and years of service, Dursan remains non reactive and inert.
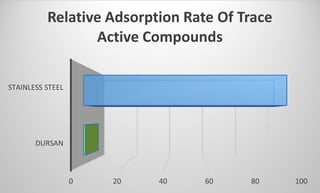
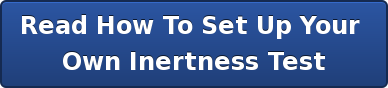
The SilcoTek Technical Service Team has lots of application and test data for your industry. Contact us and we'll be happy to help!