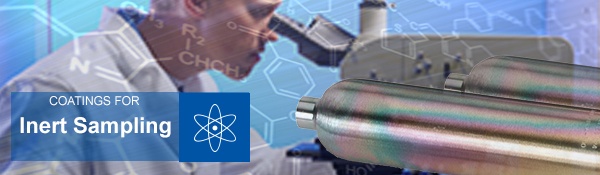
Customers interested in improving instrument sensitivity and precision often evaluate the coating surface for reactivity to confirm the coating meets performance parameters. But what's the most effective way to test a coating for inertness and purity? Let's find out.
Testing and evaluating a coating or surface for adsorption, non reactivity, inertness and purity can be a challenging undertaking, especially when testing reactive compounds at trace levels. If you're having trouble figuring out how to evaluate a coating, you're in luck! We've got 30 years of experience recommending processes or methods to use when evaluating an inert coating or surface. Here are a few tips we've learned over the years.
In this blog you will learn:
- Tips on how to evaluate a surface for chemical inertness and reactivity
- How selection of test compounds and concentration affect results
- Get sources for inertness test design standards and specifications
- Get ideas on test system design
|
Selecting The Compound & Concentration
How do I know a surface is inert for my test? That's a tough question to answer. A surface may perform very well for one compound but not for others. Additionally, a surface may be adequate for higher levels of concentration but not for trace analysis or speciation. Let's first discuss compound selection, then we'll expand the discussion to concentration.
Selecting the compound
If you have one compound and don't expect to test other reactive chemicals then picking a compound to test is pretty straight forward; just pick that chemical at the expected concentration and run the test. Of course you'll need to run a statistically significant number of runs (say n=5) and test a few coated flow path component samples to assure repeatability, but overall a pretty easy method to evaluate inert surfaces. Before testing it's always a good idea to understand the capabilities of the coating or surface. Here's information on our coatings:
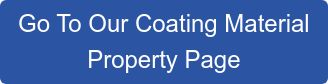
Unfortunately most analytical systems will be exposed to several active compounds over the life of the flow path. In this case things can get complex quickly. Unfortunately you can't test all reactive compounds, there are millions of chemicals out there so testing them all would take just a few minutes short of forever. Rather than spending the rest of your life evaluating various flow path surfaces, consider testing a class of reactive compounds rather than all potential analytes. For example, endrin and DDT are excellent environmental test compounds because they rapidly degrade when in contact with a reactive surface, especially if it's a hot surface.
Chromatography companies offer good reference source material for selecting chemical standards containing target compounds for your analysis and surface needs, be it environmental testing, clean air standards, whole air monitoring standards or oil and gas sampling. The standard can be sourced from several companies that offer calibration samples. If you're testing lots of compounds the standard can get expensive pretty quickly so be judicious in your selection.
Here are a few links to relevant company information on sourcing chemical standards.
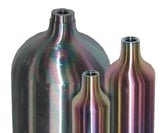
Concentration matters
OK I've selected my test compounds, is that it? Sorry no. You'll need to select the compound concentration. In many ways concentration is as important as the test compound. Take sulfur analysis for example. A stainless steel surface may yield perfectly fine results at percent level analysis but sample at part per million levels and it's a completely different story.
Sulfur is known to adsorb or "stick" to stainless, glass or ceramic flow paths. But flow enough high concentration sulfur through the flow path and the active surface will be seasoned or primed to the extent that tests will yield reasonably good results. However at ppm or lower levels, sulfur will be adsorbed onto the surface because there's not enough of the analyte to adequately "prime" all the active sites. So virtually all the sample is lost. Here's a chart comparing the loss rate of trace H2S. You can see that virtually all H2S is lost within an hour of exposure. The SilcoNert® coated surface adsorbs virtually no sulfur compound.
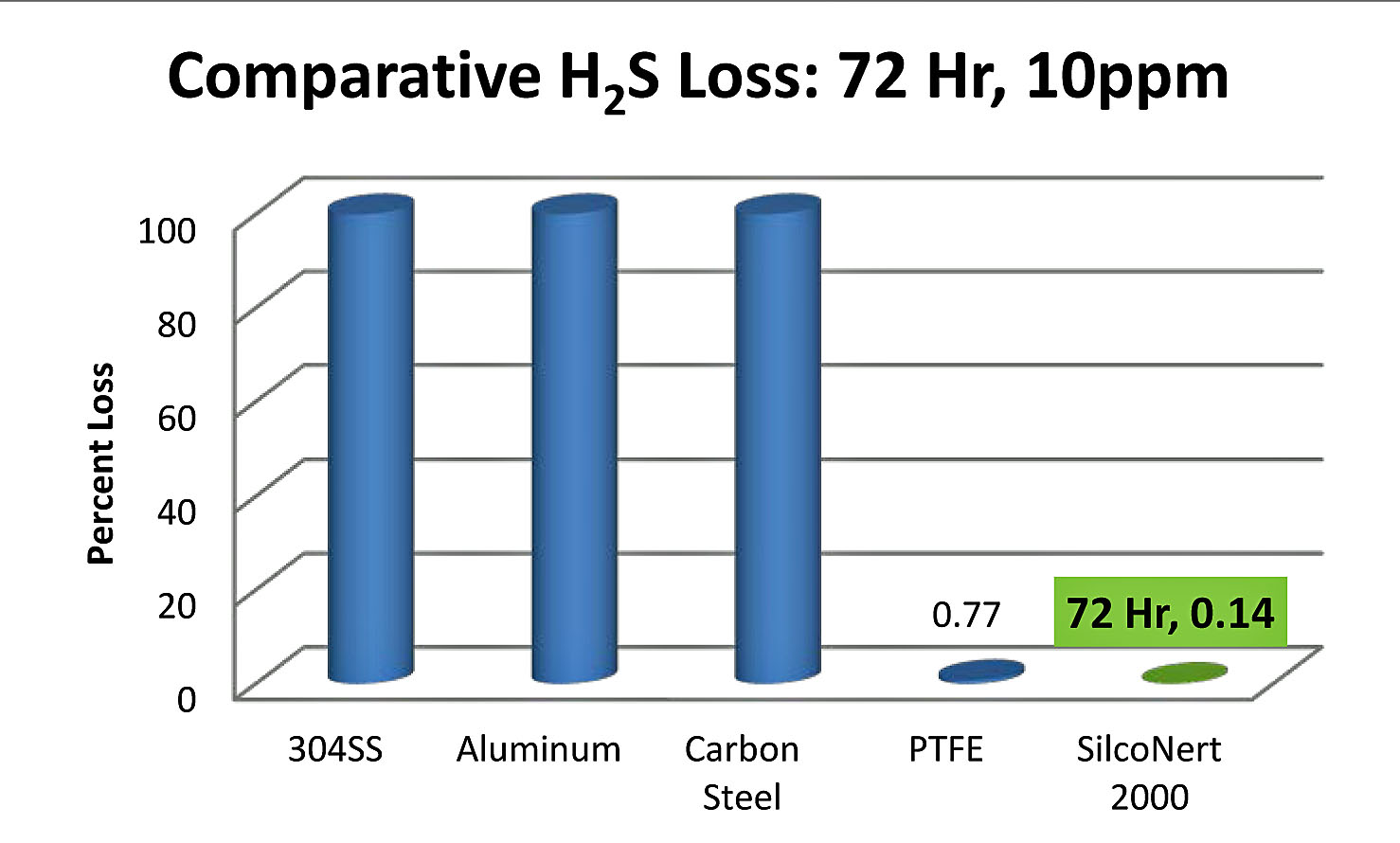
Factors to consider when selecting concentration include:
- Regulatory requirements
- Industry or customer standards
- ASTM recommended methods
- Internal specifications
Setting a lower concentration limit to use for a coating evaluation may depend on the lower calibration point for the instrument or system. To establish that baseline, find any relevant regulatory or industry standards that dictate a calibration sample range. Often you'll need to test a system for levels lower and higher than the established range of operation. So for example a calibration run for a flare CEMS may require a total sulfur sample be run at a low side of 5ppm and a high range of 200 ppm for an operation range of 10 to 150ppm. The high range sample may be relatively easy to achieve but all sorts of gremlins can pop up when dealing with a 5ppm sample. Some factors to consider when testing at low levels include:
- Faster expiration of the standard or stability of the chemical standard
- Contamination and cross contamination
- Adsorption by an uncoated reactive fitting or fritted filter
- Seal material like o-rings that may be reactive
- Moisture contamination may cause adsorption
- Corrosion related particulate adsorption
- Seams or pinholes that promote cross contamination or trace sample loss
- Cleanliness of the system
- System surface temperature, phase change
- Detector or instrument sensitivity to the target compound
The details make a big difference when testing reactive samples at low levels. Take note system parameters and any changes made during the test to assure an apples to apples comparison and to avoid "getting lost in changes" while troubleshooting a system.
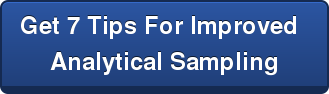
System Design, Testing an Inert Coating
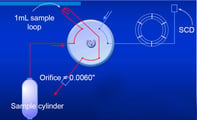
So you're all ready to go! You've got the samples at the right concentration, you've got the test method (or ideas of a method) based on industry, regulatory or company procedures. But what about the test system itself? Here are a few ideas to be sure you get reliable, accurate test results.*
The test system may be set up in accordance with regulatory or industry practices; when evaluating a surface always take into consideration the following:
- Apples to apples. Don't change the test conditions during the evaluation
- Nooks and crannies. Minimize surface pin holes, threads grooves or other areas where a sample can get trapped and cross contaminate a test.
- Combining reactive surfaces with inert surfaces. You can't test an inert surface by placing it in line with a reactive surface. For trace analysis the sample will be adsorbed by the reactive areas so a comparison of surfaces would yield the same results. You'll need to either coat the entire test flow path and compare 2 competing flow paths or select a known inert surface and change only a portion of the flow path for comparison.
- Minimize flow path complexity. Keep the test flow path as simple as possible to minimize test variables.
- Make the exposure time adequate to determine effectiveness. Either flow through a long tube at low flow or through a high surface area component like a sintered metal frit to be sure there's adequate surface exposure. Another option would be to test by residence time in a sample cylinder. This method can take a while (days or weeks) but will allow you to establish the degradation rate of the sample. To accelerate the test, consider heating the sample cylinder to accelerate the reaction rate. Here's an example of 15 day comparative testing for sulfur adsorption. The top chromatographs continue to show sulfur peaks after 15 days for SilcoNert® (Sulfinert®) coated sample cylinders. Uncoated stainless steel sample cylinders adsorb the sulfur (lower graphs).**
- Seals. Viton, septa or other seal surfaces can be active. Minimize the use of polymeric seals to limit adsorption.
- Instrument capability. If your instrument is not capable of testing to the desired concentration or is not set up to yield reliable results for a target compound then don't bother evaluating the surface. Instrument factors to consider are:
- Detector (designed for the target compound)
- Appropriate instrument (LC or GC?) Should be capable of testing in the target sensitivity range for those compounds.
- Calibration. Instrument should be calibrated and maintained
- Training. The analyst should be familiar with the instrument and detector.
Take a short cut
Are there papers available comparing surfaces for inertness for your sample? You bet! SilcoTek has a considerable library of comparative whitepapers demonstrating the effectiveness of our coatings in inertness applications. We don't want you to take our word for it, or rely on someone else's test for your application, but reading papers that discuss testing a coating in a particular application can be helpful in getting evaluation ideas or understanding the limitations of a surface.
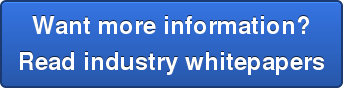
*Image courtesy of Restek® Corp.
* *Data courtesy of Restek® Corp.