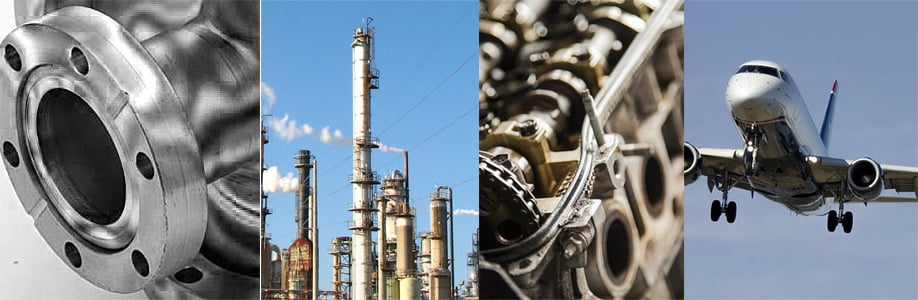
We get lots of questions relating to the effect our coating may have on customer parts. Let's review some of the more common concerns.
Tips For Designing, Fabricating, and Installing Coated Parts
The SilcoTek® Technical Service Team is here to help customers understand how to use, maintain and design for the use of our coatings in their process or products. We get lots of questions about the physical properties and limitations of our coatings. The more a customer understands how to properly employ and maintain coated surfaces in their process, the better the coating will perform throughout the life of the product or process. With that in mind, here are a few of the more common questions about how our coatings impact part design, fabrication, and installation.
In this blog post you will learn:
- Factors that can limit the use and application of silicon chemical vapor deposition (CVD) coatings.
- Capability of the CVD process when coating various materials and product shapes.
- Physical properties and capabilities of SilcoTek coating products.
|
Here are some common questions asked by our customers.
Will I have to change the dimensions of my parts to account for the coating thickness?
There are several variables that determine thickness, but all SilcoTek coatings in current production are deposited at < 3µm thicknesses. We're able to select the right coating thickness for your application. For example, SilcoTek is able to coat precision 0.5um filters with minimal impact to filtration performance. Please contact us to discuss thickness specifications.
Can the coatings withstand high process temperatures?
In general, temperatures should not exceed the recommendations below in order to maintain the coatings' specified performance properties, but coated parts can be used at higher temperatures under certain conditions. Heat treatment of parts at the application's temperature will ensure the best results if exceeding the temperature limits suggested below. Please contact technical support for additional information or to discuss your application.
Watch our heat resistance video to see how our coatings perform under extreme heat:
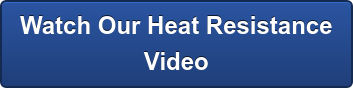
SilcoTek® coatings are stable to the following temperatures in an inert atmosphere:
*The values below reflect limits of the coating material itself and assume that the base substrate is stable at these temperatures.
SilcoNert® 2000 |
450 °C; 400 °C (oxidative atmosphere) |
SilcoNert® 1000 |
1410 °C |
Silcolloy® |
1410 °C |
SilcoGuard® |
1410 °C |
SilcoKlean® |
450 °C (functionalization loss), 400 °C (oxidative atmosphere), 1410 °C (melting) |
Dursan® |
500 °C; 450 °C (oxidative atmosphere) |
Dursox® |
500 °C |
Notak® |
300 °C |
Are the coatings wear resistant and can they withstand sliding friction?
Depending on the coating, wear resistance can be increased. For example Dursan® will double the wear resistance of stainless steel. The SilcoNert® coating will not significantly improve wear resistance. Dursan will reduce sliding friction and can be used for light duty applications involving wear or sliding, like in a slider valve or cylinder bore involving elastomeric seal contact.
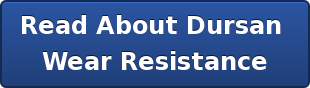
What materials can you coat? Are there some metals you cannot coat?
Most alloys of stainless steel, exotic alloys (except some duplex steel alloys), ceramic, and most glass materials can be treated. Some other metallic materials, such as nickel, brass, and copper, are incompatible with the 400+°C temperatures used in the process, and should not be treated. Go to our material compatibility chart for a complete listing of material that can and cannot be coated, or contact our team to discuss your application.
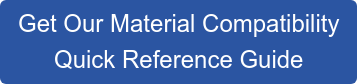
Note: carbon steel, F22 or similar carbon steel, is not recommended for coating in corrosion resistant applications. Treated carbon steel may rust in corrosive environments. Avoid corrosive environments when using treated carbon steel in inert sampling applications.
SilcoTek® can coat aluminum substrates however there are limitations for components used in high stress applications. Go to our aluminum coating page to learn more about aluminum coating capabilities. Contact us to ensure optimal processing of your aluminum parts. Want to learn more about coating metal parts? Read our materials blog post.
Can I weld parts after coating?
Welding will remove the SilcoTek coating ~2-4mm in all directions from the heat affected zone. SilcoTek can coat over high-quality welds, such as those listed in our material compatibility guide.
Can brazing or soldering impact the coating quality?
Read a Technical Insight from SilcoTek's R&D group regarding coating of brazed and soldered components.
We recommend vacuum brazing or welding of joints for best coating quality. Vacuum brazing is a high temperature, flux-free brazing process that results in a contamination-free joint. SilcoTek recommends vacuum brazing services from Solar Atmospheres Inc.
Do SilcoTek® coatings change the roughness of the part surface?
SilcoTek coatings conform to the microstructure of the part surface. There is minimal filling of voids or change to the overall surface roughness. Overall roughness measurement may be reduced slightly (1-2 RA reduction), but not a significant change in roughness. Some SilcoTek coatings have a higher lubricity than stainless steel, so even though surface roughness has not changed, the surface may have a lower friction coefficient.
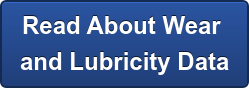
Can sealing surfaces be coated?
Yes! SilcoTek coatings are proven to withstand compression and shear stress common to CF, face seal, and threaded sealing systems.
Get more information about SilcoTek coatings and sealing surfaces.
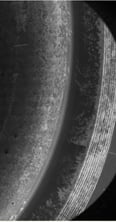
|
FESEM (Field Emission Scanning Electron Microscopy) image of the coated pre-sealed surface shows the coating conforms to the sealing area. The raised surfaces of the face seal gland area can be seen. SilcoTek coatings conform to surface contours and small orifices. |
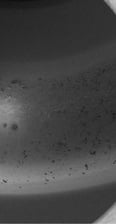
|
After making the metal-to-metal face seal per manufacturers instruction, a second FESEM image of the post sealing surface shows no scarring or scratching, only trace particulate from the silver gasket. |
Can compression fitting ferrules be coated?
SilcoTek does not recommend coating ferrules, we've found this may lead to leaking problems after coating.
Can SilcoTek coat small bore or intricate parts?
Yes, SilcoTek can coat intricate parts and small bore tubing. For example we're able to coat sample needles and components with blind holes or narrow passages. How do we do it? We our process involves specialty gases that are able to penetrate small or intricate openings. We're even able to coat fritted materials. The image below shows a sectioned fritted metal filter after coating. You can see how our process gases are able to penetrate the filter and coat internal surfaces.
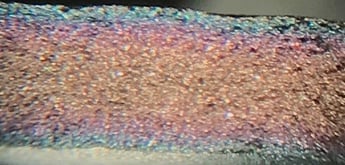
If you have more questions about factors that influence part design and use of our coatings or want to get more CVD coating information, you can chat directly with a member of our Technical Service Team. Our chat is open weekdays from 9:00 am until 5 pm. Or follow us on LinkedIn.
