We frequently get questions about the electrical conductivity of our coatings. SilcoTek® offers coatings that are both conductive and insulative for various applications. We will characterize and explain our coatings' dielectric properties in this blog post.
How Do SilcoTek Coatings Perform for Electrical Conductivity?
Silcolloy® and Dursan®, 2 of SilcoTek's coatings most relevant to dielectric applications were characterized by the Dielectric Properties Lab at Penn State University, and the results are summarized in this blog discussion. Here we report the bulk resistivity, relative permittivity (also known as dielectric constant) and dielectric breakdown strength of these coatings.
Silcolloy is a multilayer amorphous silicon coating ideal for high temperature applications, corrosion resistance, preventing metal ion leaching, and oxidative environments, while Dursan is a functionalized silica-like coating that is commonly used for inertness in harsh environments.
Flat stainless steel coupons with one mirror polished surface were coated and used in all measurements, as shown below in Figure 1. Measurement was performed on the polished surface only.
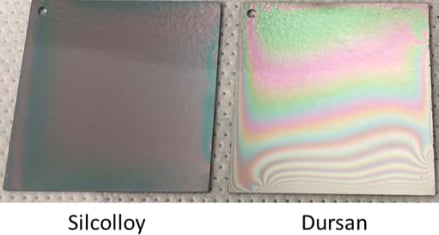
Figure 1: Coated stainless steel coupons used in dielectric measurements
Measurements and Instrumentation:
Dielectric spectroscopy: Agilent LCR meter (HP4980A) was used to measure the capacitance and loss tangent. The dielectric permittivity is calculated following Eq(1):
εr=C∙t/ε0∙A Eq (1)
Where C, e0, A and t are the capacitance, dielectric permittivity of vacuum (8.854 10-12 F/m), electrode area and sample’s thickness, respectively.
I-V (current-voltage):
An HP4140B DC source and pA meter was used to apply the voltage and measure the current. Voltage, ranging between 0.1 and 0.5V, was applied for 2 seconds before measuring the current to make sure steady state is achieved. The IV curve was then linearly fitted to calculate the resistance.
DC dielectric breakdown:
A Trek amplifier was used with a DC source to apply the voltage, which was increased at 100V/s until breakdown occurs. The voltage at which the final breakdown happens was recorded. Using the 2-parameter Weibull statistical analysis, the dielectric breakdown and Weibull modulus were extracted.
Need to pick a coating for your application? Our coating selector will help guide you to the best coating for you.
Go to Our Coating Selector Guide
Results and Discussion:
The results of the dielectric measurements for the coatings are reported in Table 1. The bulk resistivity data for Silcolloy was obtained with gold electrodes, whereas silver electrodes were used for Dursan due to the poor adhesion between the gold electrode and the Dursan surface.
The relative permittivity and dielectric loss tangent were measured at room temperature under 1 kHz. The relative permittivity of Silcolloy was found to be higher than the value reported for amorphous silicon (11.8),1 probably due to different hydrogen content in the coating. The relative permittivity for Dursan is also higher than the reported value for SiO2 (3.9),2 which can be explained by the carbon incorporation in Dursan.
As there is no perfect insulator in real world materials, the dielectric loss tangent provides us with a way to quantify a dielectric material’s inherent dissipation of electromagnetic energy (i.e. the ratio between lost energy/stored energy). Also, the lower the loss tangent value, the better a dielectric material is. Dielectric loss comes from both conduction loss (current leakage) as well as heat dissipation caused by movements/rotations of the molecules in an alternating electric field. For example, dielectric loss in water is the mechanism of heating up food in a microwave oven.
Table 1: Dielectric properties of two SilcoTek CVD coatings

Two breakdown strength values are reported per coating, with value 1 usually referred to as defect-driven breakdown, and value 2 represents the inherent dielectric materials' breakdown. Both coatings exhibited defect-driven breakdown, but value 1 was not available for Dursan due to poor data fitting. The dielectric strength value for the Dursan coating is quite respectable, and only slightly lower than the literature values for silicon dioxide (SiO2) (at 10 MV/cm). This is not surprising given that Dursan has a SiO2 framework with carbon incorporation.
It is also worth noting that the dielectric breakdown in both coatings occurred over some time because of defects self-clearing until the final failure took place. Defects self-clearing refers to the localized breakdown of dielectric films due to the presence of impurities such as pinholes or embedded foreign particles. After a successful self-clearing event, the dielectric material may continue to sustain the application of an electric field.3 This behavior is often observed in polymers and is referred to as “graceful failures,” in contrast to sudden catastrophic failures. Graceful failure is desired in applications where the ability to maintain functionality is needed as portions of a system breakdown occur.
The Weibull modulus is a shape parameter for the Weibull distribution model that maps the distribution of physical flaws present in a brittle specimen. When flaws are consistently and evenly distributed, samples will behave more uniformly and the calculated Weibull modulus will be high; when flaws are clustered inconsistently, there is more sample-to-sample variability and the calculated Weibull modulus will be low.4 Empirically, a value higher than 8 or 10 is usually preferred for Weibull modulus.
Lastly, for thin insulating films such as SilcoTek’s CVD coatings, the substrate material and its surface roughness have a major influence on the quality of insulation.5 For rough surface finishes, thicker films (multi-microns) in general may help improve the consistency and reliability of the dielectric performance.
Conclusion:
Dielectric measurements were carried out on two CVD coatings (Silcolloy and Dursan) by PSU’s Dielectric Properties Lab. Silcolloy and Dursan are both commercially available. Bulk resistivity, relative permittivity (dielectric constant), dielectric loss, breakdown strength and the related Weibull modulus for the coatings are reported in this blog.
For electrical insulation applications, Dursan outperforms Silcolloy and would be the preferred coating. However, if other coating properties are required for the application or the environmental conditions warrant, other coatings such as Silcolloy may be recommended.
Our coating properties guide shows an overview of the material composition, maximum temperature, contact angle, and what each coating does. For a more detailed look at all of our coating properties, please check out our coating properties quick reference guide.
If you have any questions about how our coatings can help in your application, please contact us for a free consultation with our experts!
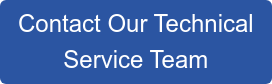
References:
- http://www.mit.edu/~6.777/matprops/asi.htm
- Robertson, J. “High dielectric constant oxides” Eur. Phys. J. Appl. Phys. 2004, 28, 265.
- Ahmed, S., Ounaies, Z. “A study of metalized electrodes self-clearing in electroactive polymer (EAP) based actuators” Proc. of SPIE 2016, 9798, 97983F-2.
- https://en.wikipedia.org/wiki/Weibull_modulus
- Schmaljohann, F., Hagedorn, D. and Löffler, F. “Systematic evaluation of thin electrically insulating layers on common engineering materials” 13th International Conference on Plasma Surface Engineering, 2012, Garmisch-Partenkirchen, Germany.