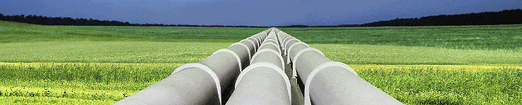
A recent article in Pipeline and Gas Journal, (Practical Consideration of Gas Sampling Systems, by David Fish, Welker Inc.), offers in-depth guidance on best practices of natural gas sampling. The article discusses ways to assure accurate natural gas characterization as well as providing historical background into why and how gas sampling methods were developed. Read the article. Key aspects of successful natural gas testing are:
Select the best method for your application:
- Spot, continuous composite, or continuous sampling methods have advantages and disadvantages. Select the method that best fits your application and need.
- Most errors are not related to the sample testing itself, but rather can be traced to the sample capture, and transport methods.
Component design and placement matter:
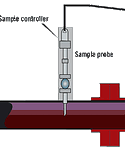
Individual component design should be appropriate for the application. Installation location is also a key factor:
- Sample probe: locate in stream, away from turbulence. Coat the probe with an inert, corrosion resistant treatment like SilcoNert®, or Dursan® to prevent loss of sulfur and mercury.
- Sample cylinder: Constant pressure cylinders will maintain sample phase; or static, constant volume cylinders for grab sample. Coat cylinders with an inert coating, like SilcoNert® 2000, to prevent loss of sulfur and mercury.
- Tubing size and installation: Pockets will trap adsorptive moisture, maintain fluid velocity, select non adsorptive coatings to prevent loss of sulfur and mercury.
- System materials, stainless steel Monel®, and super alloys are common materials, all are adsorptive to sulfur and mercury sampling.
- Filter and filter material, regulator design, sample pumps, valves and fittings all play an important role in the overall sample system performance. All should be coated with an inert coating like SilcoNert® 2000 or Dursan® to assure accurate sulfur and mercury testing.
The impact of a marginal sample transport system:
Sample measurement devices are capable of measuring natural gas Btu content to .5 Btu, but poor techniques can cause variation as high as 65 Btu in a single cylinder. A poor sample system design can make repeatable natural gas testing for Btu, sulfur and mercury nearly impossible.
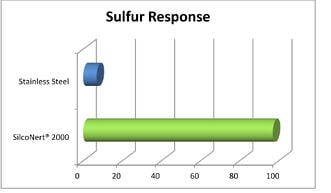
Active and adsorptive surfaces like stainless steel, Monel® or other alloys can completely adsorb sulfur and mercury in the natural gas sample. Artificially low sulfur readings can impact feedstock value, poison downstream catalysts, and cause artificially low odorant measurement.
SilcoTek® coatings can improve natural gas measurement by:
- Preventing sulfur/mercury adsorption and loss.
- Improve corrosion resistance.
- Reduce friction, improve operation of constant pressure sample systems.
- Repel adsorptive moisture.
SilcoTek® coatings can be applied to all wetted surfaces:
- Tubing
- Probes
- Filters
- Valves/Fittings
- Sample cylinders
- Constant pressure sample cylinders
- Regulators
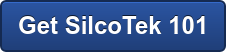