Molding PVC (Poly Vinyl Chloride) presents the processor with a host of important issues, and many companies in the molding industry have similar problems. Heating PVC results in the outgassing of hydrochloric and hydrobromic acids. These acids can be a substantial pain-point for operators and can lead to pitting, oxidation, and other problems with a mold, die or other metal machinery within your environment. Mold build-up can occur over time, along with pitting from HCl corrosion that will eventually accelerate soil deposits. SilcoTek's CVD coating technology can help to protect equipment from this less-than-desirable environment.
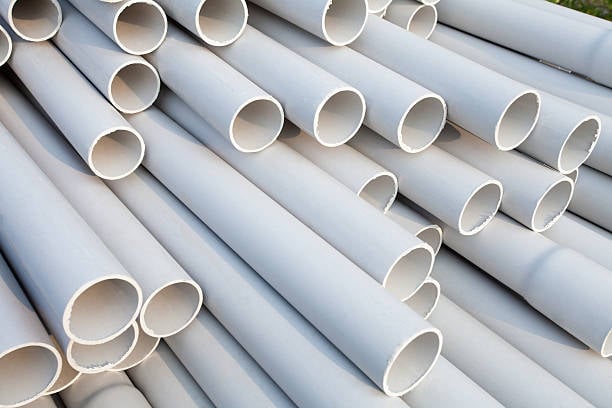
Coating Solutions for Common Molding Problems with PVC
As with any project, running into problems can be very frustrating. For most of us, we want to find a quick and easy solution to avoid any further setbacks.
Common Solutions
Common molding problems could lead to mold sticking, expensive equipment replacement, down-time, reduced yield, and many others. To combat these common problems, we found a few solutions:
- Mold release agents
- While helping with mold release, release agents can cause a host of other problems
- Constant re-application needed
- Can cause buildups on the mold itself from heating release agents
- Can cause part defects and contamination if not cleaned properly after use
- Constant Cleaning
- Will deteriorate the mold over time
- Moisture and heat from cleaning can cause premature corrosion on the mold, requiring spray on corrosion inhibitors - which also cause problems
- Teflon Coating
- Does not hold up under higher temperatures
These options may work for a limited time, but a more sustainable solution is available.
How Can SilcoTek Help?
SilcoTek has a variety of coating solutions for a plethora of applications, and these are our best-suited coatings for molding applications:
- Dursan® Coating
- No need to reapply
- Durable coating
- Easier cleaning. Dursan creates a non-stick/non-toxic surface that can be cleaned without the need for harsh chemicals or sand blasting.
- Anti-corrosive on all fronts: Dursan protects from HCl corrosion, but has the added benefit of protection from moisture in the air that can cause corrosion on a mold surface.
- Notak® Coating
- Excellent non-stick properties
- Hydrophobic / oleophobic
- Solvent resistant
Not sure if the coating would help your application? Contact us! Our technical service team is ready to answer your questions and work with you to find the right coating solution.
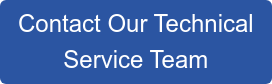