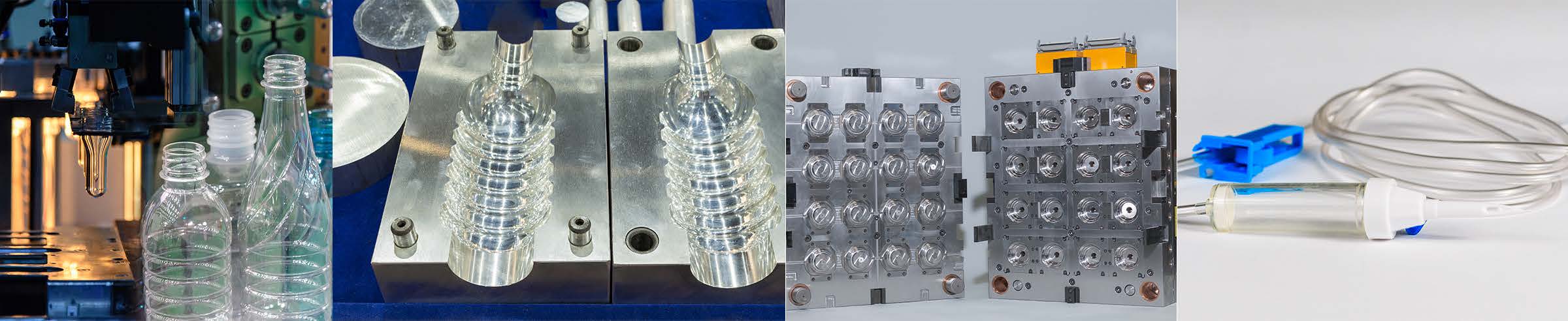
SilcoTek® is helping customers in the plastics molding industry solve their surface problems successfully by using our
Dursan® coating technology on their metal molds.
Can CVD Coatings Improve Plastic Mold Quality in Analytical Products?
Dursan is a chemically inert silicon-based coating that improves the release, corrosion resistance, and durability of
molds, leading to less maintenance and more production up-time.
In this blog post you will learn:
- How Silicon CVD coatings can improve plastic mold release without the use of chemical release agents.
- How Dursan coated stainless steel molds can reduce cost and improve quality.
- How silicon CVD coated stainless steel improves plastic corrosion resistance mold durability and helps to prevent process contamination.
|
Performance
Products used in trace analytical testing need to be free of contamination in order to achieve ppq performance in the lab. That means that any plastics used in or exposed to the sample need to be free of trace chemicals like mold release agents or particulates from corrosion. That's why it's important to use corrosion resistant, chemical free mold release agents, like Dursan. But are CVD coatings good for both product quality and the bottom line?
Testing proves that a silicon CVD coating, like Dursan, can improve plastic mold durability and improve the removal of the plastic part from the mold without the use of chemical agents that can contaminate the product. For example, a Dursan coated Stainless Steel mold was subjected to daily injection molded operations for (4) months and cleaned every (2) days. When the molds were returned to SilcoTek for analysis, the coating showed no signs of wear or degradation.
In another test, a packaging application for health care products improved the corrosion resistance of their plastic extrusion process by coating components with Dursan. After (5) months of use there were no signs of corrosion with any of these coated parts. The previously used nickel-coated SS parts experienced severe corrosion after (3) weeks of use. The customer was able to significantly extend the life of the plastic mold components, saving close to $50,000 USD per year with the use of our coating and the customer found significantly less product contamination.
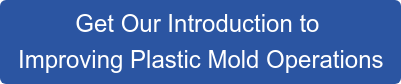
Protecting stainless steel from corrosive attack.
The Dursan® coating prevents corrosion by a factor of 8x or more by preventing interaction of analyte or cleaning corrosives with stainless steel. The surface exceeds typical metal passivation capability and inertness by orders of magnitude. Immersion testing in 6M HCl shows that Dursan coated surfaces prevent surface attack by orders of magnitude compared to passivated stainless steel.
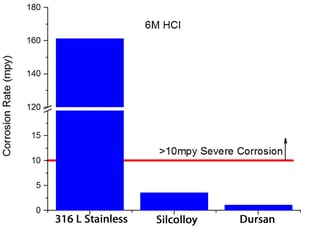
Dursan also significantly improves bleach corrosion resistance; making it the ideal coating for bio analytical, environmental, and process sampling. The graph below demonstrates the improved corrosion resistance or Dursan. The common coating on the left showed significant variation and corrosion after exposure to a 15% bleach solution for 72 hours. The Dursan coated surface showed minimal corrosion.
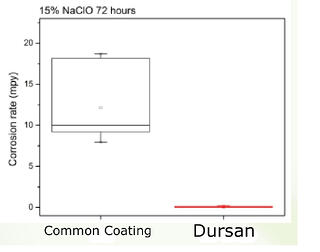
Dursan improves the performance of many materials:
- Stainless steel and steel alloys
- Hastelloy® (Yes Dursan can improve performance of high performance alloys!)
- Glass
- Ceramics
Wear resistance
CVD coatings are thin but are they wear resistant? We tested Dursan vs. uncoated stainless steel in a comparative pin-on-disk wear test. We found Dursan was more wear resistant than stainless steel and had higher surface lubricity, making the wear resistant coating ideal for valve components and wear prone surfaces.
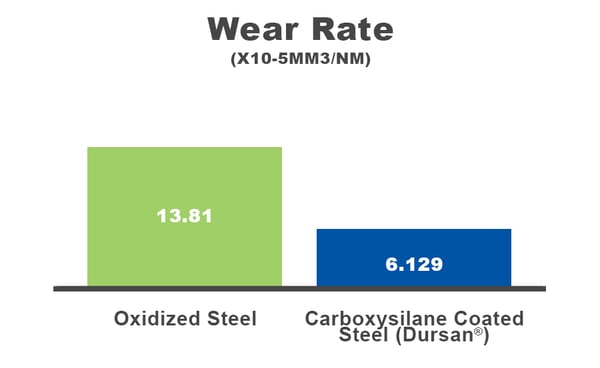
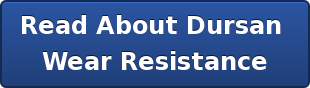
Benefits of Dursan® in Plastic Molding Applications
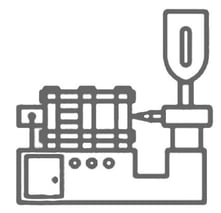 |
• Improve release of molded parts - Releases your molded parts quickly and easily for higher yields and longer up-time.
• Replace spray-on mold release agents - Dursan is chemically bonded to the mold so it is durable.
• Eliminate post-process cleaning of molded parts - Dursan does not flake or transfer onto molded parts due to its excellent adhesion properties promoted by SilcoTek’s patented chemical vapor deposition (CVD) process.
• Maintain existing tolerances and surface finishes - The Dursan process results in less than 2 microns of coating thickness, leaving critical surfaces and finishes unchanged.
• Safe to use - The Dursan coating technology is certified by NSF International and therefore is FDA compliant.
|
Plastic Molding Applications Using Dursan®
Plastic Materials
SilcoTek’s Dursan coating has shown excellent release properties with:
• Polyethylene Terephthalate (PET)
• Polyurethane (PU)
• Polypropylene (PP)
• Pebax
• Nylon
Mold Substrates
Dursan® can be successfully coated onto metals such as stainless steel, carbon based steel, and tool steel
alloys.
Molded Product Applications
Contact us to discuss your molded product application. Current applications of Dursan coated molds include:
• Medical Devices
• Medical Testing
• Food and Beverage Containers
• Consumer and Industrial Products
Have a question about how SilcoTek® can improve your precision plastic mold operations? Contact our Technical Service Team to speak with our experts.
