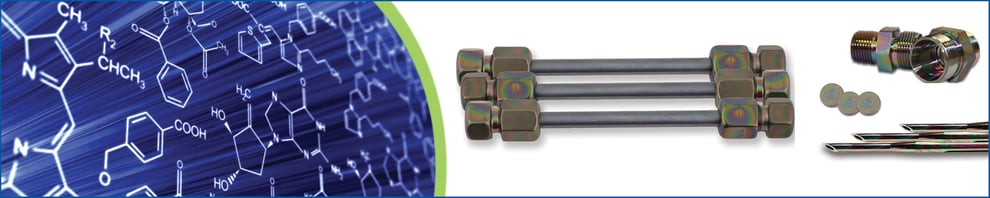
Did you know the base material can have an impact on the performance of CVD coatings? We tested the compatibility of most metals and other materials commonly used in analytical testing. Here's what we found out.
About Silicon CVD Coating Material Compatibility
Why is it that we can coat most metals but cannot coat some materials like nickel? Furthermore we say that we see excellent results with Hastelloy® (up to 74% nickel) and Inconel (over 70% nickel) but on the other hand Monel (2/3 Nickel & 1/3 copper) is not treatable. Why is there variation in material compatibility for CVD coatings? All great questions! To understand why certain metals perform the way they do we'll need to jump into alloys and how they react with our coatings.
In this blog post you will learn:
- How metal alloys can improve CVD coating adhesion.
- How some base metal elements cannot be coated but can be coated in an alloy.
- How material compatibility can impact test quality and reliability.
- How to select the best coating and surface for the application.
|
About alloys and why they make a difference in coating results.
An alloy is a mix of a base element metal with another element (or elements). Metal alloys can often have quite different properties than their base metal. In the case of alloys, two wrongs can often make a right. For example aluminum and copper are pretty soft metals, but mix them and you get an aluminum alloy that's stronger.
The same goes for iron mixed with a touch of carbon. Carbon's not even a metal but mix a touch of it with iron and you get steel which can have all sorts of benefits like greater strength. Throw in a bit of chromium into the mix and the resulting stainless steel will vastly improve corrosion resistance.
Alloys have benefits and drawbacks that impact coatability. We'll use nickel as an example.
Confused about what we can coat? Get our latest quick reference Material Compatibility Guide.
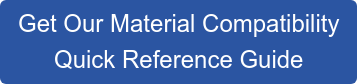
How Material Compatibility Can Impact Performance
Our process is incompatible with pure nickel, because it induces a different growth mode and does not produce the typical nice amorphous (unstructured or non crystalline) coating we see on a stainless steel substrate. You see silicon is happy to bond and diffuse into all sorts of metals, glass or ceramic surfaces but it preferentially does not bond particularly well with nickel. In fact after the first few silicon atoms bond to the nickel surface, the remaining silicon atoms prefer to bond to themselves rather than to the nickel. The result? Under magnification you'll see lots of silicon columns with deep voids, almost like skyscrapers in a big city. That's not a good coating because chemicals you're interested in testing can hide in the valleys, or corrosive chemicals can attack the exposed surfaces. The SEM image below is a general example of what columnar growth looks like under magnification. See? Kind of like big buildings.
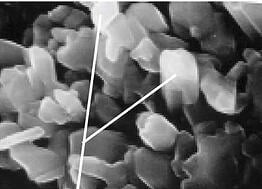
Our amorphous coating when applied to stainless steel, glass, ceramics or many metal alloys will bond uniformly to the surface and build a coating layer-by-layer over the entire surface. It will look something like this SEM image below (note silicon particulates on the surface).
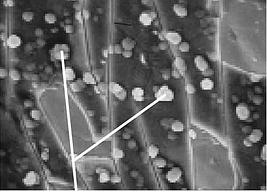
The Auger plot below shows how our silicon barrier coatings bond to the surface. Auger electron spectroscopy (AES) sputter depth profile analysis quantifies the material composition and diffusion zone characteristic of our silicon coatings (in this case our inert SilcoNert® coating). The plot shows a layer of approximately 2000 angstroms (200 nm) of silicon. Note the approximately 500 angstrom diffusion zone between the stainless steel surface and the silicon coating. An Auger depth profile of a coated nickel part would show areas with little to no coating while other areas would have a much greater depth profile.
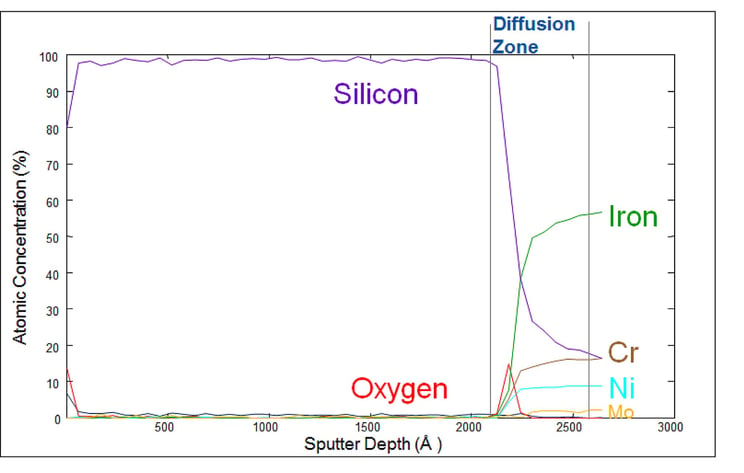
Back to alloys.
In cases where nickel is alloyed with other “stabilizing” elements, such as Cr (chromium), Si (silicon), P (Phosphorus) etc., even when nickel (Ni) is the major component base metal, our process coats beautifully over these alloys (e.g. Hastelloy®, Inconel, or typical nickel brazing filler alloys such as Ni-Cr-P or Ni-Cr-Si-P). In these cases, the coating is able to bond to the "more beneficial' alloy despite the Ni base metal because the alloy characteristics will allow silicon to more easily or preferentially bond to the surface uniformly. So that's why we can coat superalloys and Ni brazing material.
You can't win them all!
In cases where nickel is alloyed with another difficult to coat element, such as copper, there is no “stabilizing force” or synergy to allow our CVD coatings to bond to the surface. A copper nickel alloy is usually incompatible with our process. Monel is such an example. Nickel and copper by itself are both incompatible with our process, so when you combine these two into Monel, it is incompatible as well.
If you want to learn about our coatings and how they benefit your applications, get our webinar:
How To Choose The Right SilcoTek Coating
Have questions about silicon CVD coating material properties? Go to our Material Property Page and get coating specifications, material data and much more.
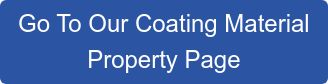