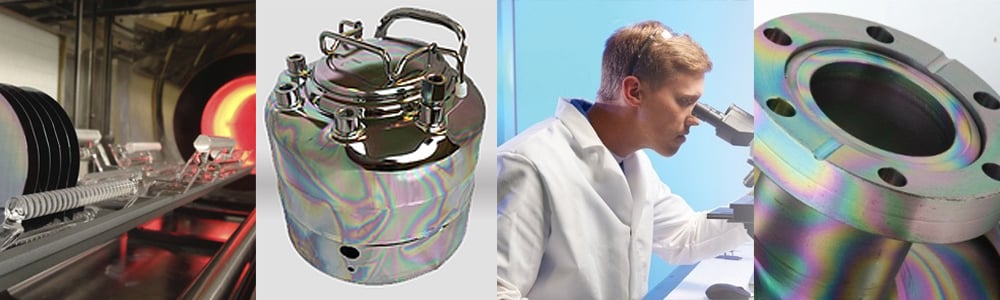
How do silicon coatings perform in high temperature and what is the thermal conductivity of silicon coatings? We turn up the heat on our coatings to see how they perform.
What is the Thermal Performance of Silicon Coatings?
In a previous blog post we focused on the high temperature thermal performance of SilcoTek’s surface-functionalized inert, heat resistant coatings, SilcoNert® 2000 and Dursan®, and the temperature limits for those surfaces. We found that our coatings can withstand some pretty high temperatures as seen in the summary below:
Inert Coating |
Maximum Temperature (Inert Atm) |
Maximum Temp (Oxidative Atm) |
SilcoNert® 2000 |
450° C |
400° C |
Dursan® |
500° C |
450° C |
Silcolloy® |
1000° C |
1000° C |
SilcoKlean® |
1000° C |
1000° C |
SilcoNert® 1000 |
1000° C |
1000° C |
Dursox® |
1000° C |
1000° C |
But what happens to silicon coatings when they're heated and do they actually conduct heat? We'll take a closer look at how our coatings perform under extreme heat.
In this blog post you will learn:
- Maximum temperature of various types of silicon and functionalized silicon coatings.
- Determine if thermal conductivity is a factor to consider when working with micro thin silicon coatings
- How various silicon coatings perform under high temperature conditions.
|
What's the Thermal Conductivity of ultra thin Silicon Coatings?
We do not have specific measurements of thermal conductivity for our coatings. There are literature values for thermal conductivity of amorphous silicon, for example (all of our SilcoNert/Silcolloy coatings are amorphous silicon), but those are values for bulk amorphous silicon. Very thin coatings of the same material do not retain the same thermal conductivity of the bulk material and it is apparently very difficult to accurately measure thin coating values.
From what we understand, our coating is so thin that it has only a negligible (at most) effect on the thermal conductivity of the material we deposit on. In other words, if we coat on top of 316 stainless steel, there is very little change to the thermal conductivity relative to the uncoated 316 stainless part. For example, a paper by Moon, Hatano, Costas, and Grigoropoulos: "Thermal Conductivity of Amorphous Silicon Thin Films" specifies the thermal conductivity of thin amorphous silicon films as being about 1.5 W/mK for 53 and 97 nm amorphous silicon films. For thicker 200nm amorphous silicon, the thermal conductivity is about 2.2W/mK. To learn more about the properties of our coatings, click the image below, read our coating e-books or go to our FAQ page.
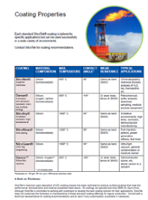
How Does Heat Affect Silicon Coatings?
To answer this burning question (sorry I couldn't resist....), we used thermal gravimetric analysis (TGA), mass spectroscopy (MS), differential scanning calorimetry (DSC) and IR/Raman spectroscopy to characterize the effects of heat on our high temperature coatings. After the touchy-feely scientific testing, we'll take the gloves off and pull out our blow torch and see how the coatings really perform! Our two base coating types are investigated in this experiment: amorphous silicon like Silcolloy and our new silicon coating, Dursox. Let's turn up the heat and see how our coatings react.
Pick your coating! Need high temperature coatings for steel, stainless steel, quartz, glass, or other surfaces? Be sure you're using the right coating for your application:
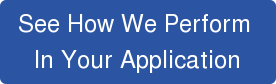
Amorphous silicon coatings, Silcolloy®:
The Silco-family of coatings consists of a single or multilayer hydrogenated amorphous silicon film. The hydrogen incorporation is a result of the deposition process. A collection of process silicon from a Silcolloy production run was collected and the mass monitored via TGA as the surface was heated. As seen in the figure below, there is an appreciable weight loss that starts at ~550°C. This can be attributed to the loss of hydrogen from the film. The hydrogen loss continues until 680°C, and then one final blast of hydrogen is released at 720°C.
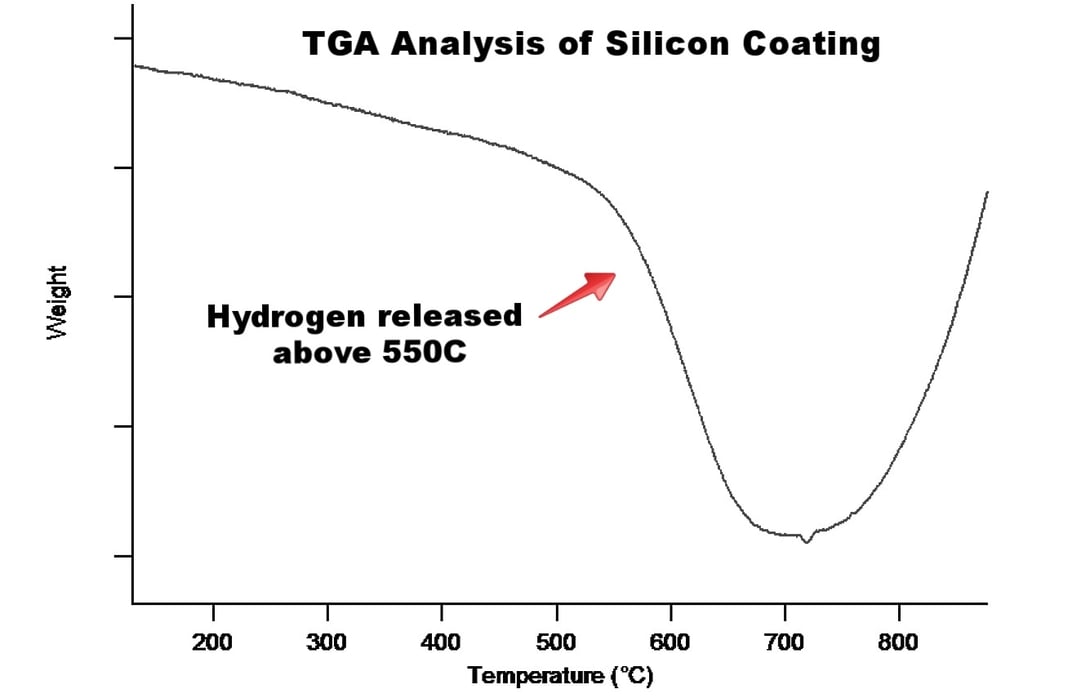
DSC (differential scanning calorimetry) was run in coordination with the TGA and as seen in Figure 2 (below), there is a very small and consistent release of energy from the coating which corresponds to a structural relaxation that increases as hydrogen is driven out of the film. At 720°C there is a crystallization peak. Note that this occurs at the same temperature as the “final blast” of hydrogen from the TGA. Figure 1 (above). The TGA plot also shows an increase in the weight after the crystallization occurs. This is due to a small amount of oxygen that is in the TGA. As the experiment is running, the system is flowing nitrogen gas under sealed containment; however, it is nearly impossible for the seal to be leak free. Trace oxygen interacted with the sample at elevated temperatures. The now crystalline silicon is much more susceptible to oxidation than amorphous silicon, especially at high temperatures, and the silicon is converted to silicon oxide.
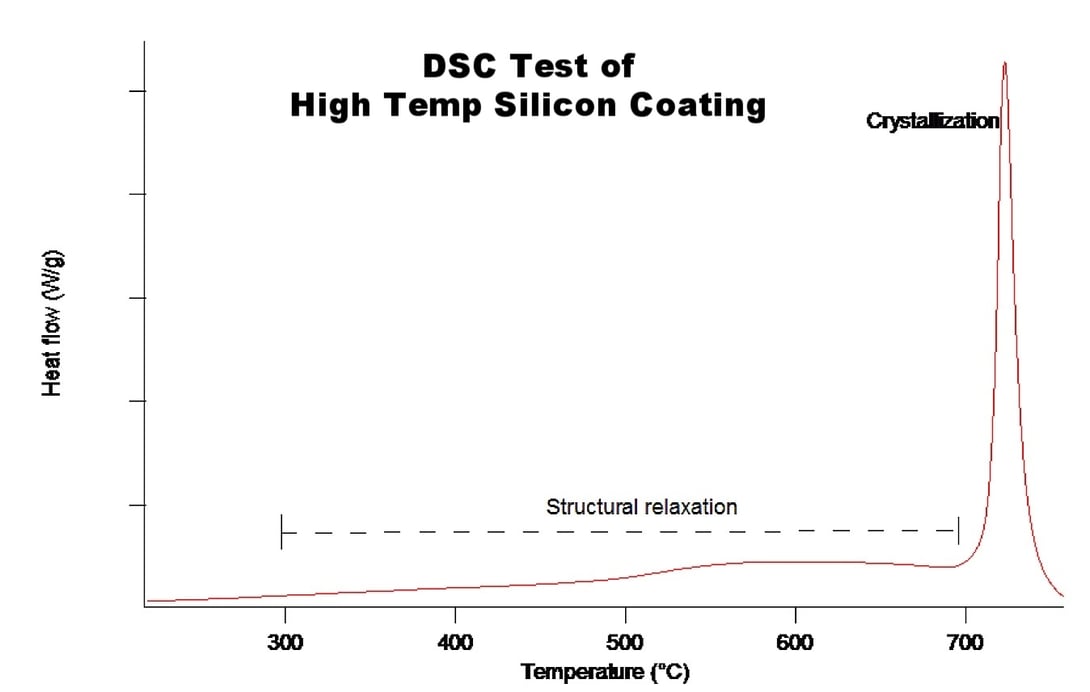
Once the silicon is crystallized, there is a well-established melting point of 1414°C of silicon. If there is oxygen in the system, the thermal oxidation of the silicon will raise the melting point to 1713°C. For the purpose of this test, we're assuming there is no influence from the substrate on the coating. In some cases, the substrate may melt at temperatures that are lower than the silicon coating or they may chemically react with the silicon to form other chemical species.
In summary, our Silco-family of coatings, like Silcolloy or SilcoNert 1000 (Silcosteel) have four major events that may occur as they are exposed to high temperatures:
1. The loss of hydrogen will occur from 550°C to 680°C.
2. Crystallization of the film will occur at or above 720°C.
3. Once crystallized, if the film is in a high temperature environment and exposed to oxygen, it will oxidize.
4. The film will melt between 1414°C and 1713°C, depending on the extent of oxidation.
Dursox coating:
Dursox® is a proprietary silicon coating that can be functionalized to create our popular Dursan® coating. Think of it like a coating foundation. Unlike amorphous silicon, there is not a wealth of information in the literature to use as guidance in determining the thermal properties of the material. When TGA-MS was run on a sample of silica powder coated with Dursox, there was a release of gaseous molecules from the coating between 500°C and 775°C.
The coating that remains after the “burn off” of the water and methane/ethane molecules is relatively stable up to 1275°C where it begins to melt. This is shown in Figure 3 (below), where DSC of silica particles that were coated with Dursan are compared to the bare silica particles up to 1500°C. The biggest difference between the two is the large peak between 1275°C and 1450°C. This peak is endothermic and is second order which can be interpreted as the melting of the coating.
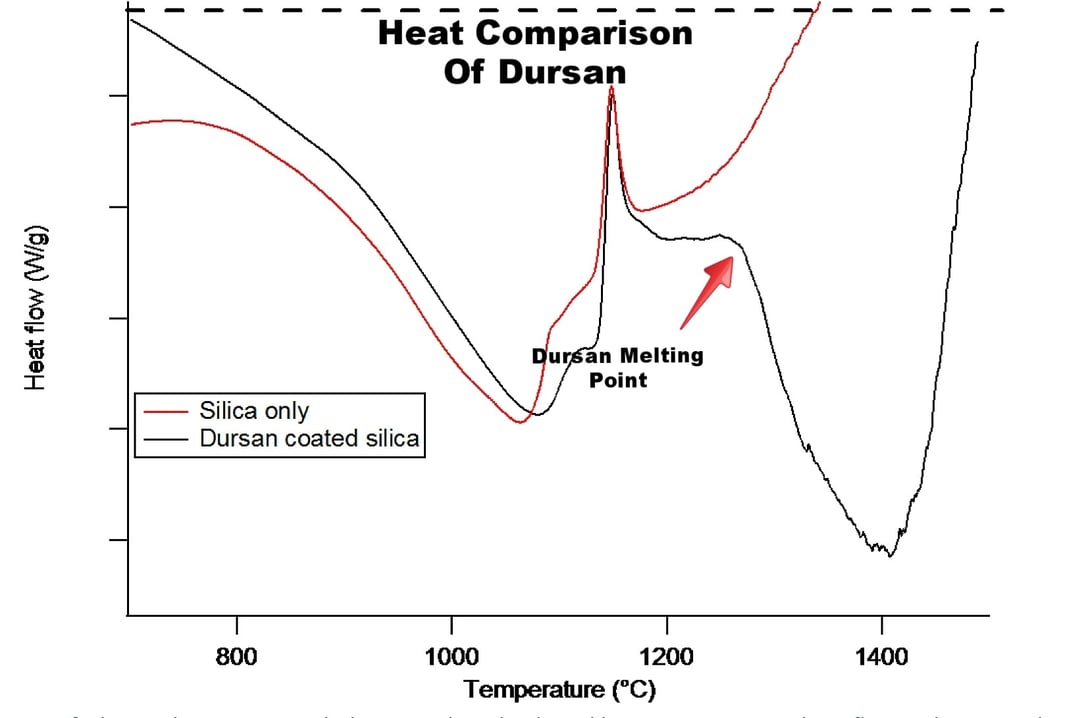
In summary, our Dursox family of coatings have two major events that occur in the bulk of the coating as they are exposed to high temperatures:
1. There is a loss of water and hydrocarbons from the coating between 500°C and 775°C which leaves a coating consisting of Si-O and Si-C bonds. This coating is chemically different from Dursox, but still may provide the protection needed for the customer.
2. The coating will melt starting at 1275°C, which would be the upper temperature limit of the coating.
If you're interested in evaluating our coatings or would like us us to test our coatings in your application, contact our technical service team and we'll be happy to discuss your application. We may not have the exact test platform, but I'm sure we can find a solution!
Contact Us To Test Our Coatings In Your Application.
