*
EPA Method 325 requires low-level monitoring of benzene at the refinery fenceline. Compliance will be costly to refineries; but to make the most of the dollars invested and to fully comply with the regulation, operators need to understand the why and how of refinery fenceline monitoring.
Understanding The Why
Rather than acting on a mandated "because I said so" approach; it's better for operators to understand why EPA is taking action on monitoring benzene and potentially other toxic VOC's. According to EPA, 85% of benzene emissions from refineries occur from fugitive sources. Typical fugitive emission sources are:
- Process piping leaks
- Wastewater streams leaks, vents, cooling towers, and drains
- Tank leaks, vents, pump leaks, maintenance related emissions
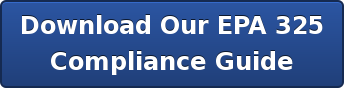
Emissions are likely to have the highest concentrations at ground level and because monitoring specific sources in the refinery will be impossible, perimeter ground level sampling makes sense and will provide the refinery operator the best data for monitoring and addressing potential benzene emissions. The ultimate payoff of will be protecting and improving the health of area communities.
According to EPA the regulatory objective of refinery perimeter monitoring is to manage benzene and eventually other toxic VOC's. Monitoring requirements and specifics of the regulation are:
- Require perimeter monitoring and corrective action upon exceeding trigger of 9 ug/m3 (2.8 ppbv)
- Require sub-3 ppb level monitoring capability for benzene.
- Monitor by Auto-GCs and passive monitoring using thermal desorption tubes.
- Trigger is based on highest concentration modeled at any fenceline.
- Continuous, 2-week sampling periods.
- Complete coverage of fenceline, average concentration over the 2 week period.
- Trigger for Root Cause Analysis / Corrective Action based on annual average concentration.
*
How to get the most out of your investment
EPA has mandated that thermal desorption tubes be inert coated to prevent adsorption of active and reactive compounds. According to EPA the analytical approach will be based on the TO-17 method which specifies pumped sampling into tubes with thermally stable adsorbents. But there are plenty of factors that can derail your fenceline monitoring program.
Potential sampling related issues with EPA 325 are:
- Interference
- Other non target VOC's and coelution of sample peaks
- Sorbent decomposition
- VOC's not completely cleaned from tubes
- Humidity & moisture contamination
- Contamination from sample handling.
- Reactivity of the sample and analytical flowpath
SilcoTek’s SilcoNert® coating can help get the most out of your sampling investment by minimizing common sampling problems. SilcoNert® will help operators more efficiently operate monitoring systems and improve reliability. Here are a few benefits of using SilcoTek® coatings in sorbent tube and GC systems.
- Improve sample peak clarity by preventing peak distortion, missing peaks and improving peak resolution.
- Providing a non-stick surface to promote easy cleaning and removal of VOC's from the sample flowpath.
- Hydrophobic, moisture shedding surface improves humidity management.
- High purity easy clean surface helps to prevent surface contamination.
- Inert surface prevents adsorption and reactivity of the critical flowpath.
SilcoNert® is recognized industry-wide as the leading inert surface, enabling refiners to sample their processes reliably with high accuracy and reproducibility. If left uncoated, even low surface area parts will adsorb VOC's of interest and lead to invalid results, causing expensive retesting and compliance issues.
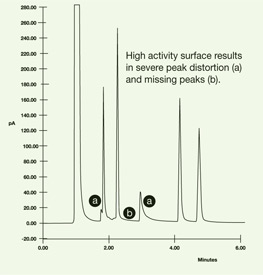
Figure 1: Uncoated surfaces within the GC flow path adsorb benzene, toluene, xylenes
and other target analytes, leading to severe peak distortion and missing peaks.
Benzene, organosulfur compounds, and other hazardous air pollutants (HAPs) that can be measured with Method 325 protocol are known to be highly reactive with bare, untreated stainless steel. SilcoNert provides a uniform barrier between substrate and sample while preventing analytes of interest from adsorbing onto the surface, ensuring they reach the analyzer and can be accurately assessed at low levels (ppb or lower).
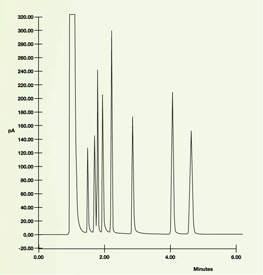
Figure 2: SilcoNert-coated GC flow paths produce sharp peaks with high resolution, giving refineries superior analytical accuracy and full compliance with EPA regulations.
Coat The Entire Sample Flowpath
To assure complete inertness, coat the entire sample flowpath with an inert coating like SilcoNert 2000. Be sure high surface area internal components are coated:
- Fritted filters
- Screens
- Tubes
- Tubing
- GC Liners
- Inlet Weldments
- Fid jets
- GC columns
|
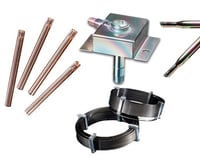 |
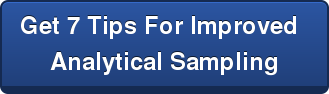
Image courtesy of US EPA.