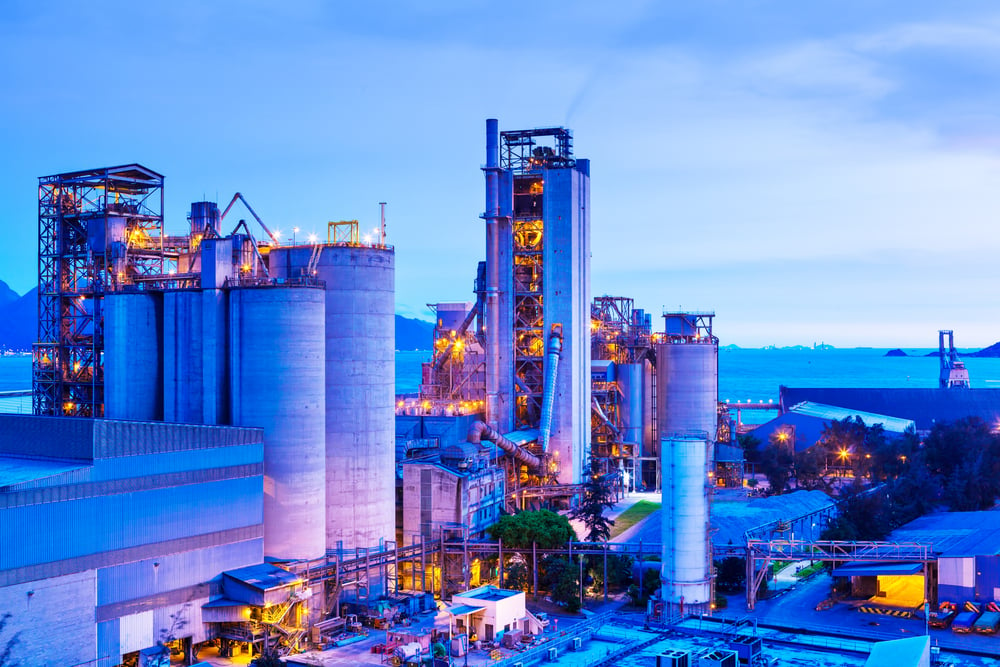
We discuss how coatings help to improve the performance of emission control systems and emissions monitoring.
Improve the Performance of Emission Control and Monitoring Systems
In this blog post you will learn:
- How high temperature corrosion resistant coatings can improve the durability of emission control systems like burn boxes, thermal destruction systems, gas abatement systems, scrubbers, and filtration systems.
- How inert coatings are used to improve detection limits for VOC, Sulfur and other air emissions.
- Learn about the various air standards and coating compliance.
- How silicon coatings can protect exhaust systems components in high temperature corrosive environments
|
SilcoTek® coatings are used in many emissions related applications. Because our coatings prevent the interaction of exhaust emissions with exposed piping, filtration, or probes; systems are protected from corrosive attack. And because our coatings are not reactive, emission compliance monitors are able to precisely measure emissions. The overall effect is that our barrier coatings reduce system maintenance and improve compliance.
Let's discuss some of the benefits and performance data for various emission monitoring and control systems for Air Quality Monitoring and Measurement.
Improved Durability and Corrosion Resistance in Emission Control Systems
Oxidation resistant, and corrosion resistant high purity coatings, like Silcolloy®, are used in high temperature exhaust applications (over 450c). The coating prevents corrosive attack and oxidation of the base metal used in the emission control system. We also offer hybrid coatings that are optimized for your specific applications. Results can be surprising, with service life extension of orders of magnitude over uncoated systems.
Recent testing of new coatings have shown significant improvement in hydrofluoric acid corrosion resistance in exhaust streams. To learn more about this performance enhancement contact our Technical Service Team.

To assure a stable high temperature coating, follow these 3 steps:
- Consult recommended metallurgy guidelines for your alloy.
- Preheat part to the target temperature per the guidelines (approximately 10 hours should do the trick).
- Heat in an inert environment to prevent oxidation of the surface.
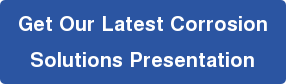
Solving Difficult Corrosion Problems in Exhaust Systems
SilcoTek coatings help to prevent common corrosion related problems including:
- Frequent component replacement
- Process or product contamination problems
- Sample probe damage and failure
- Lost productivity due to excessive downtime
|
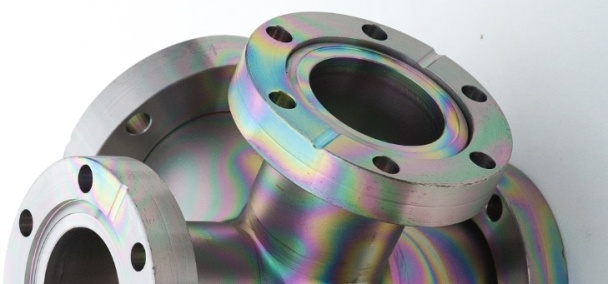 |
ASTM immersion testing proves SilcoTek® coated stainless steel enhances corrosion resistance by orders of magnitude, matching the performance of super alloys in many applications. Even after immersion in concentrated hydrochloric acid (below) the Dursan® coating and Silcolloy coated stainless steel coupons continue to perform with minimal corrosion, demonstrating performance comparable to super alloys.
/astm%20g31.png?t=1570811309696&width=570&name=astm%20g31.png)
SilcoTek coatings perform in a variety of corrosive environments including sulfuric acid and bleach.
Comparative Corrosion Summary |
|
|
|
Stainless Steel Corrosion Rate (mpy) |
Dursan Coated Stainless Steel (mpy) |
6M Hydrochloric Acid, 24 hr exposure |
160 |
1 |
25% Sulfuric Acid, 24 hr exposure |
55 |
5 |
52 Week Salt Spray |
<0.01 |
<0.01 |
Bleach |
1.7 |
0.1 |
Oxidation Resistance
SilcoTek coatings act as an inert and high purity barrier, improving the oxidation resistance of substrates.
Inert coatings like Silcolloy® 1000 improve oxidation and corrosion resistance of stainless steel by preventing oxygen from interacting with the stainless steel surface; increasing oxidation resistance by orders of magnitude.
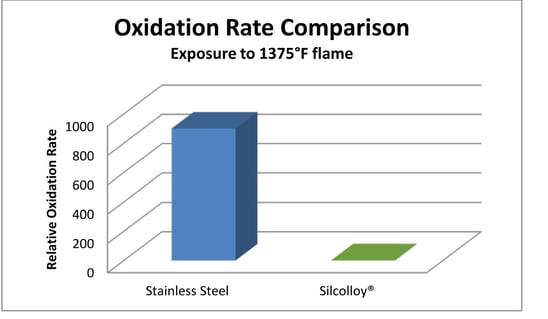
VOC Measurement
Volatile organic compounds (VOCs) have been linked to health issues, air pollution, green house gasses and ozone pollution.
VOCs are a contributing factor to pollution deaths because they are emitted during the burning of fossil fuels. Additionally, VOCs impact indoor air quality and are present in household chemicals, and emitted during production processes. Accurate sampling and analysis of volatile organic compounds have become critical to understanding and mitigating their impact to our environment.
Unfortunately VOCs can react with and be adsorbed by stainless steel, aluminum, and other sample pathway surfaces. If flow path surfaces react with the analyte, it's difficult to get reliable trace analysis results. Problem areas include:
- Calibration gas cylinder walls retaining and degrading VOC standards, causing variation in calibration gas quality.
- Sample tubing adsorbing and desorbing volatile organics resulting in false positive or false negative results.
- Fritted filter adsorption of volatiles
- Exposed stainless steel in valves and fittings reacting with volatiles
Selecting inert and durable materials for sampling critical flow path surfaces can be a key factor in successful analysis. Mr. Stefan (S.T.) Persijn of VSL, Dutch Metrology Institute, (in conjunction with the German Meteorological Office, DWD) presented a comparative study of adsorptive properties of various materials commonly used in VOC analysis.*
Read The VOC Presentation
The study exposed various tube surfaces to methanol at 50 and 100°C and measured adsorption rate of the surfaces. Results show that an inert coating like SilcoNert® coated stainless steel prevented adsorption and reaction with VOCs in critical flow paths. The study summary, below, highlights the comparative results:*
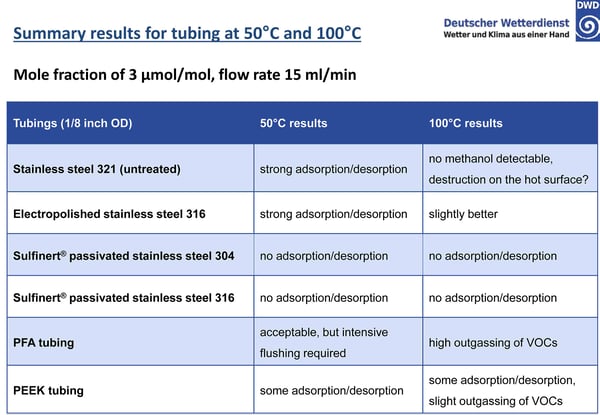
The untreated stainless steel readily adsorbs active compounds with complete loss of methanol. Electropolishing will smooth the surface and reduce overall surface area but adsorption is still significant. PFA and PEEK tubing require careful management of the surface in order to achieve acceptable results. Sulfinert® coated stainless steel does not adsorb active compounds because the inert silicon CVD surface bonds to and diffuses into the stainless steel substrate, preventing interaction with reactive sites.
The Key Factor in VOC Analysis? An Inert Flow Path.
Be sure to coat the entire flow path to prevent selective adsorption by reactive surfaces. Not coating a fitting or fritted filter can significantly impact analytical results and can cause calibration failures, increased system maintenance, false positive/negative results, frequent retesting, and potential regulatory compliance issues. To understand how our coatings improve performance to to our Chemically Inert Coatings page.
Coated flow path surfaces include:
- Whole air sampling canisters
- Regulators & mass flow control
- Valves
- Fittings
- Tubing, duct, and probes
- Liners (yes we can coat glass)
- Fritted filters
- Sample cylinders
- GC, FTIR, and instrument components
|
** |
Learn More About VOCs
And Inert Sampling
Sulfur Measurement
The world is catching on to the benefits of clean air. China for example has enacted aggressive new standards to improve air quality. They recognize the benefits of improved health, a stronger economy and a better functioning society. They realize that fewer air quality related fatalities, less flight cancellations, and fewer pollution related plant shut downs benefit quality of life and the quality of China's economy. In fact, the world seems to be getting the idea that clean air is important. Just look at the number of new tighter air standards being enacted throughout the world:
What's the primary objective of all these new air quality standards? Reduction of pollution effects through the detection and control of particulates, low level sulfur (SOx), and NOX emissions.
What's the key to control of SOx and NOx? Reliable detection. Without a way to sample and compare pollution levels, measuring the effectiveness of air pollution controls like scrubbers and clean fuels would be impossible. Unfortunately sulfur is a tricky element to detect because it tends to stick to all sorts of metals, glass, and ceramics; which are common materials used in sample flow paths. You can learn how to prevent sulfur sticking and adsorption by going to our Inert Coatings page.
Read Inert Sampling
Presentation
Why is sulfur hard to sample and detect?
Because sulfur and sulfur compounds tend to stick to materials commonly used in sample flow paths. If the sulfur gets trapped in the flow path, the instrument can't accurately record the data, making control of scrubbers and processes difficult at best. Here's an example of how sulfur can get lost in a tube. Shell and O'Brien conducted a study where a sulfur compound was injected into a tube. Then they waited for the detector at the other end to "see" the sulfur. They waited... and waited... and finally after 90 minutes some sulfur hit the detector! Here's a graph of the test results.
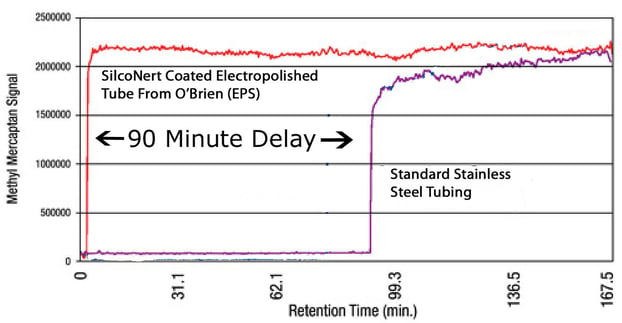
The first red line is a graph of the sulfur response when that tube is coated with SilcoNert®. Under the same test conditions the response is almost immediate! Virtually no sulfur was lost in the tube. When all the sulfur makes it to the detector, the plant or refinery can accurately control emissions or their process; making for a better product while minimizing sulfur related air pollution.
Read The Entire Sulfur Detection Study By Shell and O'Brien Analytical
How do SilcoTek® inert silicon CVD coatings improve sulfur sampling and air quality?
Our inert CVD coating, SilcoNert®, provides a barrier between the sample and the reactive stainless steel surface. That allows the sulfur or NOx sample to pass right through the flow path without interacting with the surface, delivering the entire sample to the detector. Our inert coating benefits include:
Sometimes it's not about how fast you can deliver the sample but how long you can hold the sample. When field operations staff take a grab sulfur sample (be it from the well or from the refinery hydrotreater) they can run into sulfur adsorption problems. The stainless steel sample cylinder surface will adsorb sulfur starting the second the sample enters the cylinder. That means time is of the essence when trying to accurately assess if the well is sweet or sour or if the hydrotreater is running to spec. Sulfur stability in a stainless steel cylinder can be measured in minutes or hours. After that, it's likely the sample is not indicative of field conditions. Conversely; SilcoNert® coated stainless steel sample cylinder stability is measured in days or weeks. That means rather than rushing a sample back to the lab, field technicians can grab and hold a sample for 30 days or more with confidence that the sample is the same as when it was pulled from the field.
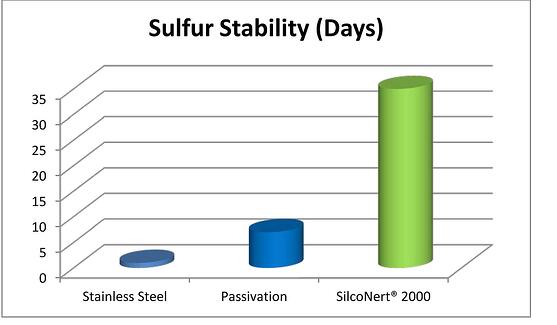
Precise and fast sulfur response allows the plant to better control pollution emissions and avoid plant upsets or regulatory compliance issues. Improved sulfur, and NOx sampling flow paths give the plant operator the tools to achieve those tighter clean air standards worldwide. Want to lean more about analytical sampling and how surface science can improve results?
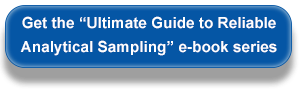
Related Standards
SilcoTek® coatings are used in a wide variety of applications. Coating uses range from mold release, process sampling, semiconductor manufacturing, oil and gas production, hydrocarbon processing, analytical testing, GC, HPLC, medical diagnostics instrumentation and much more. Customers in these fields often ask how are the coatings used in test methods and do SilcoTek coatings comply with my industry standards? That's a valid question, so we rolled up our sleeves and dug through methods or applications that use our coatings. To be sure, there are many more applications and uses for our coatings, here are just a few on our list.
We searched methods and related products used in the method application to find industry approved or customer approved use of our coatings. For some applications we’re formally approved, in other uses we're referenced in tests or standards. Some applications call out a specific coated component either by our brand name or the customer brand. So we're casting a wide net to list as many standards and methods for various industries. Of course individual customers have their own approval process and methods which are not discussed. We don't list customer approved uses as they are confidential.
Here are the many standards that specify our silicon coatings.
Related Oil and Gas Standards:
A standard we don't comply with
What about NACE standard MRO 175 (Materials for use in H2S containing environments)? Do SilcoTek coatings comply with this standard? No. MRO 175 specifies the base metals that are approved for H2S environments, not coatings. No coating will apply to MRO 175, only base metals. Our coatings when applied to MRO 175 approved metals will improve the surface inertness and improve H2S detection. The base metal will continue to comply with MRO 175. Applying our coatings to non compliant materials will not make them compliant, only inert to reactivity.
Bio Inertness and Bio Contamination
Our coatings act as an inert barrier between the exhaust flow sample and the flow path surface. The coatings prevent corrosion, cross contamination, and chemical adsorption. All benefits are geared toward improving test reliability and sensitivity. Our coatings are FDA compliant by meeting NSF standards.
Related Standards
Air Quality
SilcoTek coatings offer high durability and inertness, making them ideal for field sampling and air quality measurement. Our coatings improve peak resolution, and allow technicians to achieve ultra low detection levels.
Related Standards
Environmental Testing
SilcoTek coating technologies have become the industry standard for inert coatings used in environmental testing. Our coatings improve peak resolution, and allow researchers to test to previously unattainable detection levels. Part-per-billion, part-per-trillion and Part-per-quadrillion are achievable when testing to industry standards.
Related Standards
About Corrosion Resistance
Our coatings are also tested to various corrosion standards. In this case our coatings are not part of the test method, we're the focus of the testing. Since corrosion testing applies to many industries, we thought it would be beneficial to list some of the methods used to evaluate our coatings for corrosion resistance. Our coatings have been successfully tested for corrosion resistance using the following standards:
To learn more about how our coatings benefit emission control and emission monitoring systems, contact our Technical Service Team. We offer free coating evaluations and consultations and are here to help you solve your material problems.
To stay in touch with the latest in coating technology, follow us on LinkedIn, or subscribe to our blog.

*Images and data courtesy of The Dutch Metrology Institute (VSL) and the German Meteorological Office (DWD) presented at the Key VOC joint project April 21st 2016, in Paris, France.
** Image courtesy of Restek® Corporation