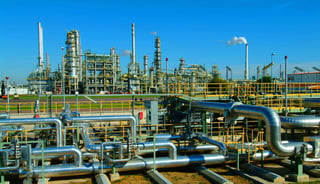
It's audit time! Yay! OK no plant operator thinks happy thoughts when a state regulatory agency shows up for an emissions continuous emissions monitoring system (CEMS) audit. You're about to enter into a bit of a dance with a 500 lb gorilla who can either pat you on the head and throw you back over the fence (to live another day) or pull some nasty leavers that could result in costly re certification or a plant shutdown.
Here are some tips regarding interacting with auditors and managing a successful audit result. Want more information about improving system durability and performance? Read up on Dursan®.
What Triggers an Audit of a CEMS Emissions Monitoring System?
EPA may send a recommend audit list to state regulatory agencies. The list is based on performance data pulled from MDC software (Monitoring Data Checker). Or local state agencies may receive air quality complaints or it may come down to simple random selection. Regardless it pays to be prepared.
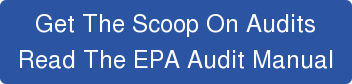
Inspector's Role
The inspector's job is to document compliance. He's not there to offer free consulting advice or to chat about the weather. He can, however offer clarification on regulatory requirements and reporting which can be helpful in gaining insight into particular areas of an inspection that's considered to be more important to the inspector or agency.
The auditor's goal is to identify areas to be corrected so the emissions source can provide good data. Depending on inspection level, the auditor will make the following checks:
- Past MDC data (checking for gaps and poor trends or unexpected or odd results)
- QA - QC checks and plan
- Calibration (frequent re calibrations can be s sign of CEMS trouble)
- System inspection
- Probe, sensors, sample lines, sample conditioning systems (Damage, no dips or kinks in tubing, flow measurement location and condition of probe, moisture removal, pump operation and filter cleaning)
- Gas analyzers (fast accurate response)
- Cal gas (expired gas)
- Flow monitors
- Maintenance log & check lists
Red Flags
There are some areas to pay particular attention to if you want to avoid further inspection and scrutiny from an auditor.
The number one red flag for the inspector will be extensive missing data or invalid data. It's a real numbers game for regulatory agencies. Agencies manage by emissions data, so missing test results, gaps in testing, or high data variability can lead to more in depth inspection or re certification.
Lots of re calibration tests can indicate trouble with the CEMS or sample system.
Gaps in maintenance records, or QC - QA records can lead to additional questions from an auditor as can apparent poor safety procedures or documentation.
Lastly operational issues like poor equipment condition (rust, damage, leaks) can raise a flag.
Pay Attention To The Soft Stuff
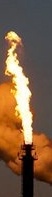
When a regulatory agency came knocking on my plant's door. I would go to great pains to read the tone and body language of the auditor. Is the auditor having a bad day? Is the auditor all business, in a hurry, all about data? Or does the person seem more chatty and engaging. Whatever the tone, need or mood of the auditor, I always tried to act appropriately to the situation. Is the auditor in a hurry? Produce the information quickly and efficiently. Want to chat? Chat away. Remember to always be helpful, forthright and informative. If you're having a problem, tell the auditor about it right away. It will go a long way to building trust and a positive reputation for both you and your company.
Here's an example of how not to build trust. Many years ago while employed as a Plant and Environmental Safety Engineer by a manufacturing company (now no longer manufacturing in the US); I discovered a soil and water contamination issue at our site. I contacted the state regulator and offered a detailed plan to mitigate the contamination and solve the problem. The state agreed to the plan and we were able to begin mitigation efforts quickly.
Our company and I had a positive reputation for being helpful and solving any regulatory issues. Based on our reputation, the state was very cooperative and helpful in solving the contamination problem.
Soon after starting remediation, a job rotation for me resulted in a new Environmental Safety Engineer for the project. The Engineer was all about litigation and stonewalling the project rather than solving the problem. The abrasive and unhelpful nature of the individual severely impacted the project. After just one meeting with the new Engineer, the state walked out of a meeting and began legal action. Years of goodwill was lost in an hour! A good reputation means something, so work hard to develop and maintain a good working relationship with inspectors. (I'd say that's good advice for most of life's relationships).
The key to a positive audit result?
We can sum up how to survive an audit by following 4 basic ideas:
- It's all about good data
- Keep thorough and complete records
- Maintain the system
- Be positive and helpful to the auditor
Want to know how SilcoTek® coatings can help you survive an audit? Read how our inert coatings improve reliability and data quality of sample transfer and CEMS systems.
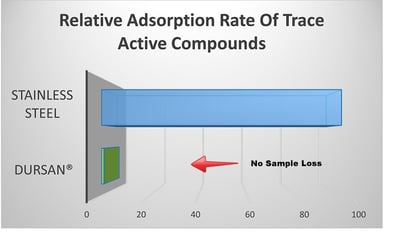
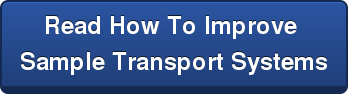