
Inert or non reactive coatings are used in analytical and process applications all the time, but how do they work and why do I need to use them?
Demystifying Inert Coatings
Coatings are used in analytical and process applications as a way to improve the sensitivity and repeatability of tests. Going to the trouble of getting an analytical flow path tested for inertness or sourcing coated parts takes time and some money. Inert coatings do help to assure a non reactive surface. For some reason they seem to magically allow better peak resolution and allow for the detection of that trace element you've been working on testing for half a day. But how do inert coatings actually prevent the loss of trace compounds or critical fluids? In this blog post we'll discuss the mechanism of inertness and how silicon coatings work to influence analytical test results.
In this blog post you will learn:
- How reactive or critical trace samples can be lost during sample transport and analysis.
- Understand the mechanism of how an inert coating prevents sample adsorption.
- Get test results showing how sample and flow path interaction can be minimized.
|
About Adsorption and Sample Loss
First lets sort out the difference between adsorption and absorption. Absorption is an effect where a material, liquid, or gas is taken up into the bulk material. Think of a sponge soaking up water.
Adsorption is an effect where the chemical or test analyte stick to the bulk material either by chemically bonding (chemisorption which is a molecular bond via valance forces) or physically bonding (physisorption, basically by attraction of molecules to the surface without chemically bonding, ie. Van der Waals forces).
The image below graphically depicts the surface interaction of adsorption.*
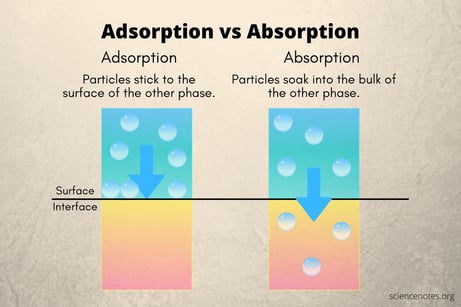
During the analysis of trace active compounds, those compounds that readily attach to surfaces or can easily react with other substances or oxides found on stainless steel. The adsorption reduces the sample concentration, resulting in a distorted test result. If the bond between the stainless steel oxide surface is somewhat weak, the chemical that is sticking to the stainless steel will later release from the surface (desorb) and cause an artificially high test result or cross contamination. The overall effect of adsorption is a change in the accuracy or reliability of the test. Chemicals to watch for adsorption effects include:
- Sulfur and sulfur compounds like H2S, mercaptans, or COS
- Volatile organic compounds (VOCs) like methanol
- Mercury
- Ammonia
- NOx
- Proteins
- Bacteria like Listeria
In the case of proteins, the stainless steel reaction may come from both physisorption or chemisorption. Making it important to have a coating that addresses both adsorptive effects. Next we'll discuss how non reactive coatings stop adsorption.
Interested in our blog content? Subscribe!

Breaking the Bond
That chemical bond or physical surface attraction that causes adsorption can be broken by either changing the surface metallurgy (reduce iron content and promote an oxide layer) by passivation techniques (often not effective) or by applying a secondary treatment or coating that is not reactive and acts as a barrier between the stainless steel and the test analyte. Inert coatings can be applied to either rough or smooth electropolished surfaces (EP) as seen in the graphic below.

The image below shows how Dursan®, which can be applied to stainless steel, other alloys, glass, or ceramics, prevents chemical interaction with the steel and does not attract reactive molecules. Inert coatings, like Dursan® and SilcoNert®, have relatively low binding surface energy and are engineered to have few open bonds that can promote chemisorption. Learn more about inert coatings by watching our webinar.

Coatings with a low surface energy have less attraction and adhesion to the surface, allowing easy removal of reactive compounds with rinsing or product flow. The result is no adsorption or sample loss and more accurate and reliable testing without cross contamination or desorption.
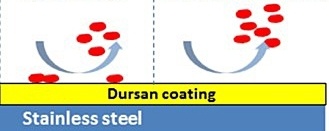
Minimizing Interaction
Let's look at some test data to show how inert coatings perform. In the test below a mix of several reactive compounds were injected onto a gas chromatograph. The sample flowed through stainless steel tubing and GC components (coating GC and GC-MS flow paths) including a separation column. The resulting peaks indicate the presence of the various chemicals. The chromatograph below is an example of what the resulting test should look like. Notice the sharp peaks. You can count each of the test chemical peaks.
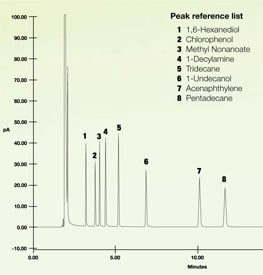
Now let's look at how the gas chromatograph looks like when the sample is exposed to an untreated stainless steel flow path. The same chemical mix is used but now there are fewer peaks! And what peaks are visible show a lot of distortion and tailing (a). The surface is so adsorptive that there are several chemicals that don't even show up on the graph (b).
Now let's repeat the experiment, only this time we'll coat the stainless steel flow path with SilcoNert® 2000. Notice how clear and sharp the peaks are and how all the chemicals tested are visible and resolved. The inert coating dramatically improved test results.
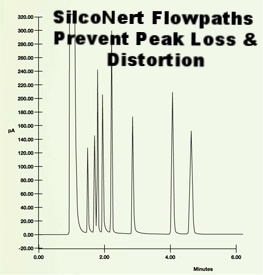
In general an inert coating will improve test quality by a significant margin. Results show that a non reactive surface will perform at levels similar to the ideal control sample and will out perform competitor or passivation techniques by nearly twice the margin.
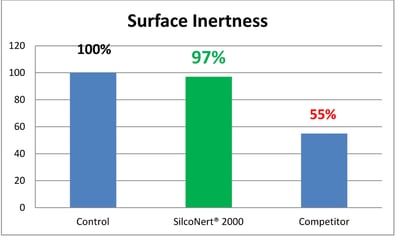
Sulfur Testing
Sulfurs also stick to stainless steel surfaces. With the onset of low sulfur fuels and blue hydrogen production, detecting trace sulfur contamination is critical to protecting catalysts and complying with emission regulations. The test results below show that even short duration storage and exposure of untreated stainless steel to sulfur containing compounds can result in significant loss and even complete loss of the sample. After just a few hours of storage the untreated storage cylinder (green line below) shows significant loss. The SilcoNert treated cylinders remain stable over the test duration and can remain stable for over 30 days.
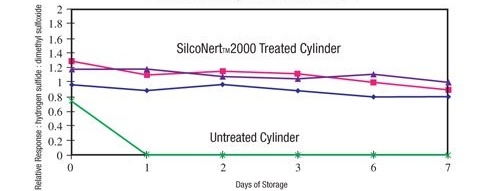
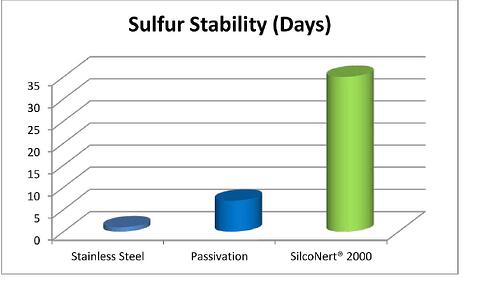
Protein and Bio Contamination
Protein adsorption is also an issue with stainless steel. Some proteins can bind to stainless steel surfaces resulting in test errors and eventual carryover and contamination of other samples. Flushing the system with bleach or ionic surfactants alone may not completely remove trace proteins. Microbalance testing below compares an untreated stainless steel surface with a Dursan® treated stainless steel flow path. Notice how the balance returns to baseline after applying a protein sample and then rinsing (top line). The untreated stainless steel sample does not return to baseline after rinsing, showing high protein binding to the surface.**
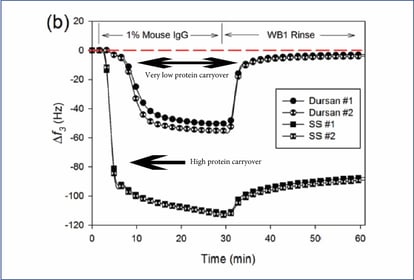
Finally let's look at bio contamination. An independent study*** recently compared various coatings to determine if in inert coating can prevent Listeria biologic formation on food preparation surfaces. The graph below shows that most of the coatings had little or no impact on overall Listeria formation. But the Dursan coated surface significantly reduced the binding of Listeria to the stainless steel surface.
.png?width=301&name=Listeria%20Active%20Cells%20(003).png)
Summary
Improving the performance of analytical and process systems depends not only on utilizing sound test methods and equipment. Good analytical performance also depends on the quality of the analytical flow path materials. Stainless steel, metal alloys, glass, and even ceramics can react with test chemicals, causing adsorption and other unintended reactions. This can result in poor test results and cross contamination. You can read more about inert surfaces on our website. Here are some additional pages for further reading:
Inert surfaces like SilcoNert® and Dursan® can break the cycle of unreliable analytical performance, without the mystery!
Stay abreast of the latest in coating new by subscribing to our blog and email, or follow us on LinkedIn.

* image credit Science Notes .Org. https://sciencenotes.org/adsorption-vs-absorption-differences-and-examples/
** Image and test data courtesy of Abbott Labs.
*** Image and test data courtesy of * "Listeria monocytogenes biofilm formation as affected by stainless steel surface topography and coating composition"; TingtingGua; ApisakMeesrisoma; YaguangLuob; Quynh N.Dinha; SophiaLina; ManyunYang; ArnavSharma; RuoguTang; JindeZhang; ZhenJia; Patricia D.Millner; Arne J.Pearlstein; BoceZhang: Food Control, Volume 130, December 2021, 108275