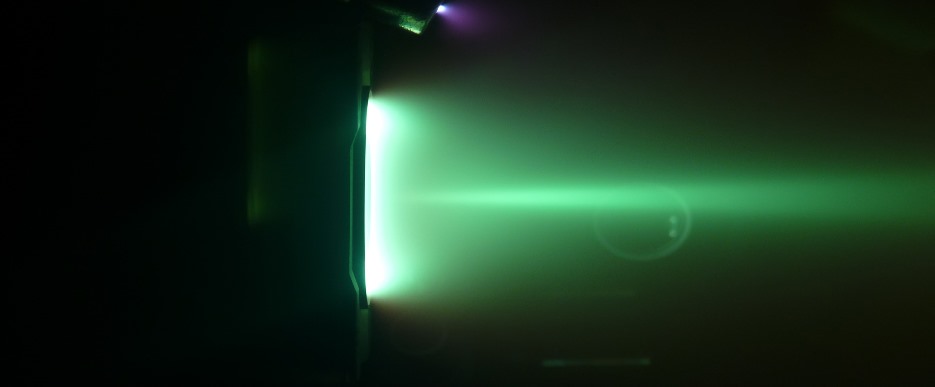
NASA tested our coatings under extreme halogen plasma conditions found on their latest state-of-art iodine thrusters. Here's what happened....
*Hall-effect thrusters have been used in satellites and medium-sized robotic space vehicles since the 1970s. These engines work by ionizing a propellant and accelerating these ions with an electrostatic potential to produce thrust. Xenon gas is the most commonly used propellant due to its high atomic weight (easy to ionize) and its chemical inertness; however, storage requires low temperatures and high pressures.
NASA Glenn Research Center has demonstrated that Hall-effect thrusters operating with iodine as the propellant can perform at the same thrust and efficiency compared to state-of-the-art xenon thrusters. Iodine has many logistical benefits over xenon for use in these engines. Iodine stores at 3 times the density of xenon, it can be stored at less than 15 psi, whereas xenon requires 2500 psi, and iodine is much more abundant than xenon, and therefore cheaper.
The Challenge
Despite these benefits, there are challenges to consider with material compatibility. Because iodine is a halogen, it can react with and oxidize surfaces, causing damage to process systems and in NASA's case may react with iodine Hall-effect thruster propulsion system materials. Very little is known regarding iodine reactivity with the wide range of spacecraft materials in a vacuum environment. This information would also be useful to the nuclear industry as iodine is regarded as one of the most hazardous fission products from a fuel nuclear reactor. NASA has developed an experiment to study the interaction between iodine and a variety of common spacecraft materials. In their tests, they have included protective coatings like corrosion resistant Silcolloy® and high durability Dursan® coated coupons for evaluation.
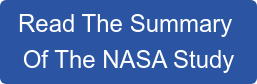
NASA stated the evaluation objective:
“The goal of this work is to begin studying the chemistry, structure and micro structural, and kinetic properties of materials and coatings exposed to iodine in a relevant environment to spacecraft technology development. For the study described in this report, five common spacecraft and test facility metals and two coatings were selected. The results of this work are pertinent to vacuum facilities and some regions of space since these environments contain molecular or atomic oxygen at very low levels.”
This report investigated iodine exposure to 304 and 316 stainless steel, A36 low carbon steel, 6061 aluminum, and 6Al-4V TiAl alloy. The study also includes Silcolloy coated on every alloy except for the 6061 aluminum, and Dursan only on a 304 stainless steel substrate.
The Results
The iodine exposure was done in a tubular furnace that was held at 300°C and flushed with 145 mL/min of argon gas along with 1 mg/min of iodine vapor. The testing exposed the coupons in triplicate for 5, 15, and 30 days. The coupons were monitored via weight measurements, XRD, and SEM. Weight change can be broken into three distinct groups: the steels which gained weight, the aluminum alloys which lost weight, and the coated coupons that had no weight loss or gain except for Silcolloy on 304 stainless steel which gained weight past the 15-day measurement period (Figure below). (Read a summary of the study.)
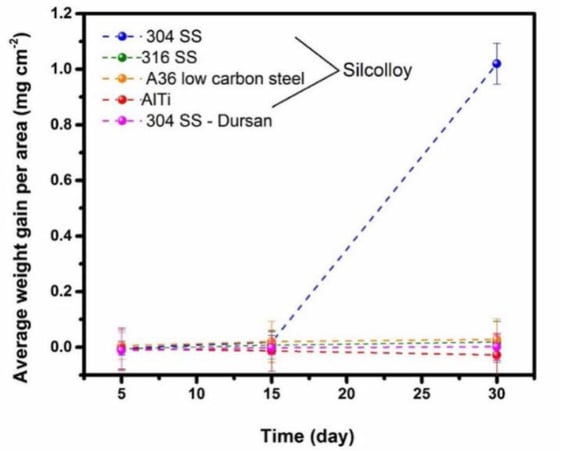
The authors concluded that Silcolloy® and Dursan® were effective in protecting the coupons that were studied. The only outlier was Silcolloy on 304 stainless steel. The coating on the 304 SS was much thinner than the Silcolloy coating on the other steels (~500nm on 304 SS whereas the 316 SS had a ~1000 nm Silcolloy coating). The authors suspect that the failure was related to the surface preparation before the coating was deposited since it worked so well on all other substrates. They plan to investigate further to address the anomaly.
Read the Complete NASA Whitepaper
Our coatings are known for their durability in space applications. We just lost one of our more well known missions in Cassini, but who knows, we may be venturing into space in an all new application. Not on the analytical side of the spacecraft, but playing an important role in propelling the mission into deep space!**
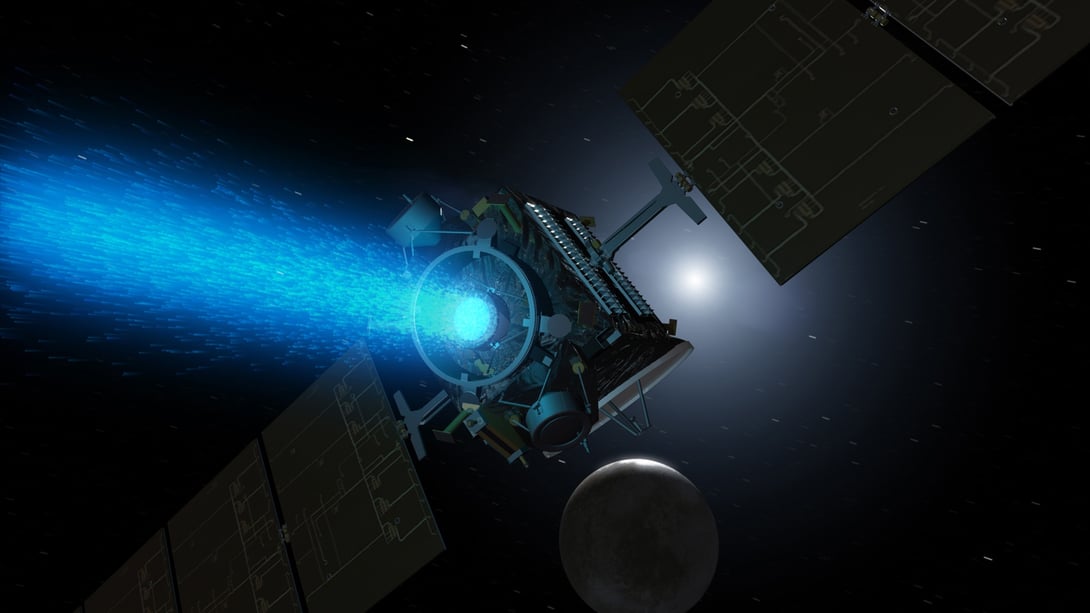
*Image credit NASA
** Image credit NASA Jet Propulsion Laboratory