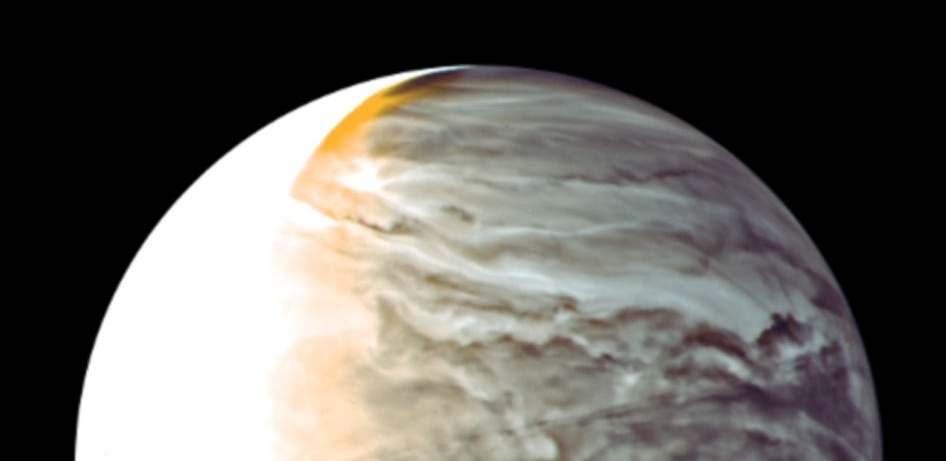
NASA tested our coatings under brutal Venus atmospheric conditions, here's what happened.
The weather forecast for Venus? 96% carbon dioxide with a high temperature of 462 ºC. I think I'll skip that Venus vacation this year and hit the beach instead. NASA on the other hand would like very much to send more probes to that unforgiving planet to better understand its origin and conditions. The catch? Lots of CO2 corrosion problems. So NASA compared several coatings under Venusian environmental conditions. As it turns out I may not be going to Venus, but our coatings could make the trip.
Why Do I Care About Venus and SilcoTek® Coatings?
Why care about whether our coatings can go to Venus? Because there are a lot of similar applications right here on Earth! Hydrocarbon processing including oil and gas downhole, upstream, downstream, refining, carbon capture technology, nuclear power, and advanced supercritical CO2 cleaning systems all face CO2 related corrosion issues. A cost effective solution that avoids using super alloys that does not require changes to design or materials would be ideal. That's where our coatings come in. Now back to NASA and Venus...
To create the next generation of probes to explore Venus’s surface, an understanding of how common spacecraft materials interact with the harsh atmosphere is necessary. NASA has started to explore coating options such as SilcoTek’s Dursan® and SilcoNert® 1040 (a SilcoNert 2000 derivative) on metal alloys in order to improve supercritical CO2 corrosion resistance. The test conditions were extreme, 92 bar (1330 psi) and 467 ºC (873F) in an atmosphere consisting of 96.5% CO2, 3.5% N2, 30 ppm H2O, 150 ppm SO2, 28 ppm CO, 15 ppm OCS, 3 ppm H2S, 0.5 ppm HCl, and 5 ppb HF.
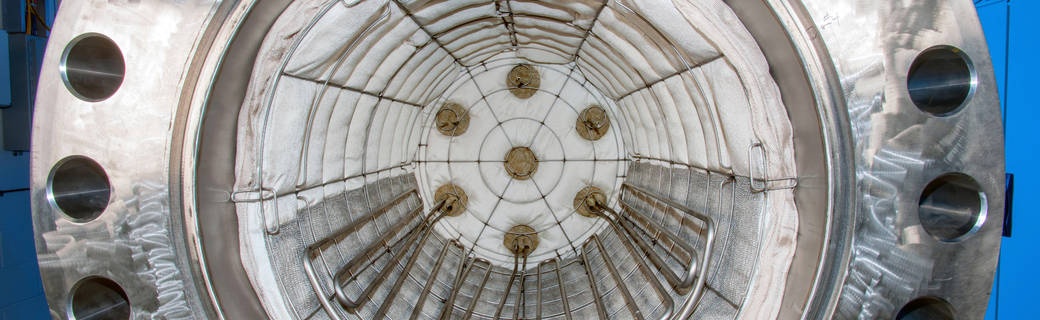
**
The Test
Bare and coated metal samples were placed in the Glenn Extreme Environments Rig (GEER) and were exposed to the atmosphere described above for 10 and 42 days to investigate the difference in weight and elemental composition between a “short” and “long” exposure. The Dursan and SilcoNert 1040 coupons were also subjected to a 21-day exposure specifically for XPS analysis. Coupons were monitored via weight gain/loss, XPS, AES, and XRD. Summary of results are below:
Read Our Technical Insight Summary of the NASA Study
Uncoated Alloy CO2 Corrosion Performance
Figure 1 shows the weight change in all of the bare metal alloys. The carbon steel (1018) shows the worst performance, followed by the three grades of stainless steel (316, 310, and 304). The bare stainless-steel coupons developed a double layer exterior in which the outer layer is mostly magnetite (Fe3 O4 ) and the inner layer is a nickel sulfide. These are formed from the exposure at both 10 and 42 days in the GEER.
Figure 1: Weight change per area of various metal coupons placed in the GEER and exposed to the Venusian atmosphere.* Data courtesy of NASA
Figure 2 shows the weight change for the Dursan and SilcoNert 1040 along with Yttria-stabilized zirconia (YSZ) and porcelain coatings. After exposure in the GEER, YSZ proved to be a semi-porous coating, the supercritical CO2 was able to penetrate through to the steel surface to start the oxidation process. The YSZ simply slowed this oxidation. NASA ranked the coatings by weight gain (effectiveness in preventing CO2 penetration & corrosion) and found SilcoNert 1040 to be the most effective followed by porcelain, Dursan, and YSZ .
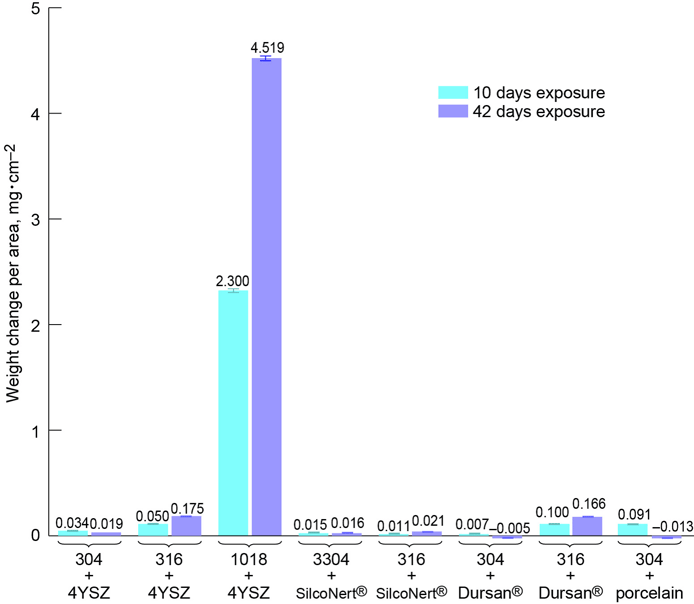
Figure 2: Weight change per area of various coated metal coupons placed in the GEER and exposed to the Venusian atmosphere.
The results? Outstanding CO2 Corrosion Resistance. Not too shabby!
XPS analysis of the SilcoNert 1040 coating, seen in Figure 3, shows that while there was some reaction of the silicon from the coating with the iron and chromium of the steel at the interface, none of the Venusian gas was able to penetrate into the bulk of the coating, or the 316 steel substrate.
Figure 3: XPS depth profile of a 316 stainless steel coupon before (a) and after (b) exposure to the Venusian atmosphere for 21 days.
Supercritical CO2 Corrosion Resistance
The study concluded that SilcoNert® 1040 was the most promising coating that NASA tested in the Venusian atmosphere. This sub-micron thick coating not only outperformed SilcoTek’s Dursan® coating, but it also out performed a 140 µm thick YSZ coating and a 200 µm thick porcelain coating. NASA will continue testing both SilcoNert and Dursan in the future, and with the knowledge gained from this study, we can now confidently recommend Silconert 1040 as protection against CO2 corrosive attack.
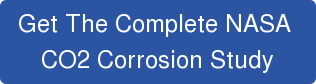
**Image courtesy of NASA