On October 11th, 2023, SilcoTek's Clay Smith presented "Breakthroughs in Material Compatibility of Inert Coatings for Sampling and Analytical Systems" at the Gulf Coast Conference in Galveston, TX. In his presentation, Clay covered some important topics, like the use of coatings in sampling and analytical systems, specifically focusing on our SilcoNert® 2000 coating.
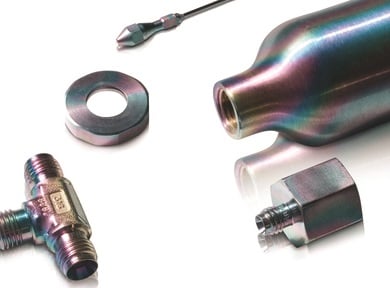
Demand for Inert Materials
The introduction of ultra-low-sulfur fuel standards in the 1990s drastically increased demand for more inert sample transfer components to make meeting these low detection limits possible. Because most sampling and analytical systems are constructed of stainless steel thanks to its easy workability, generally chemically resistant properties, and durability, companies were searching for alternatives to PTFE coatings with better high temperature stability, adhesion, and density to withstand chemical process environments. SilcoTek's founders developed a solution to this problem: coat stainless steel flow path components with amorphous silicon, a ceramic-like material, to make the stainless steel they want to use chemically inert.
About SilcoNert
Since it's launch in 2001, SilcoNert 2000 (then named Sulfinert®) has been a solution for improving analytical instruments in countless applications worldwide, from environmental labs to NASA space shuttles collecting samples from Mars. Though stainless steel is often the preferred material of construction as mentioned before, certain applications such as hydrofluoric acid (HF) alkylation processes in refineries require other specialized materials to withstand harsh process chemistries. Recently, SilcoTek’s R&D team developed a way for us to SilcoNert 2000-coat Monel®, which is preferred in these alkylation processes to withstand the HF, one of the most corrosive and aggressive chemicals in existence. Aluminum is also becoming more desirable as a way to reduce cost, weight, and variation in raw material quality. Today, SilcoTek can SilcoNert-coat nearly every aluminum alloy as routinely as stainless steel thanks to our continuous process improvements. These materials that have historically been incompatible with inert silicon-based coatings can now be modified to meet the evolving needs of customers across numerous industries and applications.
Is Electropolished Tubing Needed for Analytical Performance?
Since the COVID-19 pandemic, many customers have reported that they have consistently struggled to find electropolished (EP) tubing at acceptable lead times. For decades it has been shown that system inertness is maximized with SilcoNert 2000 on the smoothest possible surface, which can be achieved by electropolishing. For this reason, many large end users have specified EP tubing for their builds for decades. However, EP is absolutely not required prior to SilcoNert coating, so we wanted to know - does EP really make a difference in most analytical applications, or will only the SilcoNert 2000 coating achieve the required performance for low-level analysis of reactive compounds like sulfur?
We used our in-house gas chromatograph (GC) to examine this further. SilcoTek's research and development team compared 20’ lengths of ¼” OD stainless steel tubing - 1 only coated with SilcoNert 2000 and not EP, as well as 1 electropolished but not coated. A test mix containing hydrogen sulfide (H2S), carbonyl sulfide (COS), and methyl mercaptan (MeSH) at 20 ppbv was used in the experiment. The results are as follows:
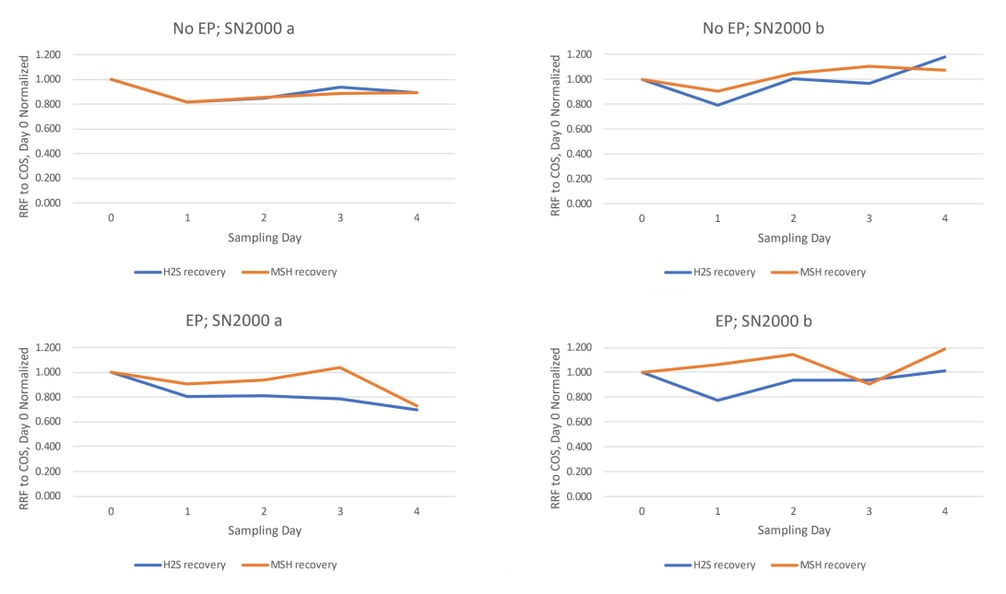
As noted in the above graphs, SilcoNert 2000 coated tubing without electropolishing consistently performed as well as coated EP tubing with the aforementioned trace-level test mix of active compounds that represent a typical sampling application. Electropolishing shows no significant impact on the inertness of the analytical system for measuring this sulfur mix. It is noted that electropolishing itself results in a smoother surface, thereby reducing the opportunity for chemical activity with less surface area, but for the purposes of our testing, it showed no significant improvement over coated tubing without EP. Click below to read the full electropolished vs. non-electropolished comparision study.

SilcoTek values its strong relationships with tubing manufacturers and electropolish service providers. We coat thousands of feet of EP tubing every day. However, in the challenging supply chain conditions we have faced for years now with no signs of letting up on the horizon, we believe it is important to find opportunities for the industry to get the products they need faster without unnecessary costs or delays.
The Solution
Since developing SilcoNert, SilcoTek has commercialized several new silicon-based coatings that show greatly improved compatibility with aluminum and copper-based materials. New “hybrid” coating recipes combine a base layer of coating that is compatible with the metal substrate, followed by a top layer of SilcoNert that completely adheres to and covers the base coating layer, leaving only SilcoNert exposed to the process stream. This hybrid coating allows for many more substrates to be coated and used in sampling systems to offer benefits of different materials.
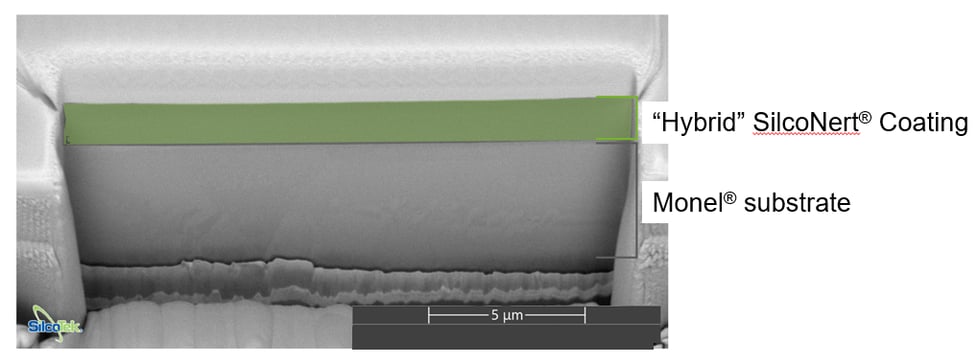
Conclusion
The presentation emphasizes the importance of inert coatings in sampling and analytical systems, particularly as samples become more complex and detection limits need to be lowered. SilcoTek continues to invest in its capabilities to meet the industry's requirements and lend a helping hand in making the world a better place. Clay's presentation highlights the significance of coatings like SilcoNert in ensuring the reliability and accuracy of analytical systems, especially in the context of evolving technical and regulatory needs. While EP has been used for years in the analytical industry, its decreasing availability and increasing lead times and cost have pushed industry professionals to find alternative solutions. SilcoNert 2000 coating can be your solution to this problem.
To view the full presentation, please click on the link below:

Benefits of Coated Sampling Systems:
- Reduce system maintenance
- Improve rust prevention
- Improve process yield
- Prevent contamination and particulate generation
- Improve oxidation resistance
For more information on how SilcoTek coatings can work for your applications, please contact our technical service team today!
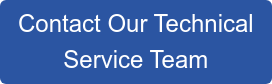