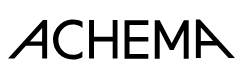
ACHEMA is a major international forum and trade show for the process industries, focusing on chemical engineering, biotechnology, and environmental protection. Held every three years, ACHEMA brings together manufacturers, service providers, and industry experts from over 50 countries to showcase and discuss the latest technologies and innovations in these fields.
ACHEMA 2024 will take place from June 10 to June 14 in Frankfurt, Germany, at the exhibition grounds of Messe Frankfurt. The event will cover five key innovation themes: process innovation, pharma innovation, green innovation, lab innovation, and digital innovation. Each theme will feature dedicated stages with keynotes, expert panel discussions, and case study presentations. Additionally, a special show on hydrogen will highlight the role of hydrogen in the clean energy transition, featuring technologies and innovations related to its production, handling, and storage.
Our partners at SilcoTek GmbH will be in attendance this year in booth F19, in Hall 11.1. For free tickets to the show, please contact SilcoTek GmbH at +496172/388410 or info@silcotekgmbh.de. Feel free to stop by the booth and speak to Rene Unglauben, Johannes Kuett, and Nils Herbach about how our coatings can help in your application!
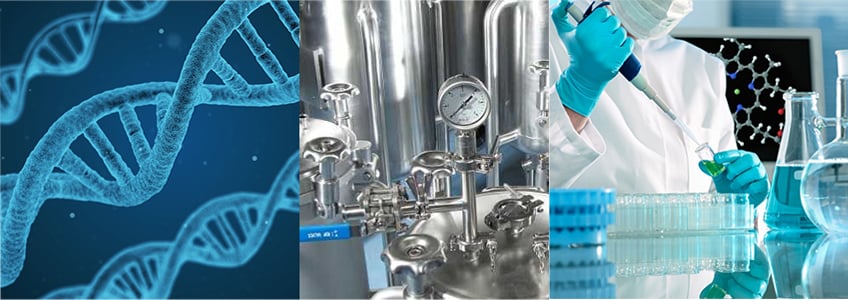
SilcoTek Leads Coating Innovation
SilcoTek's coatings provide several advantages for applications relevant to ACHEMA 2024, particularly in the pharmaceutical and biotech industries. Our coatings, created through a chemical vapor deposition (CVD) process, enhance the performance of various materials by offering properties such as chemical inertness, corrosion resistance, and anti-fouling capabilities..
-
Chemical Inertness and Corrosion Resistance: SilcoTek coatings like Dursan® and Silcolloy® are known for their exceptional chemical inertness and corrosion resistance. These properties are critical in chemical processing, pharmaceutical, and biotech applications where the purity and integrity of the products are paramount. The coatings prevent metal ion leaching and chemical interactions that could compromise the quality of the pharmaceutical compounds or biological samples.
Our coatings act as a barrier to reduce or prevent ion leaching and interaction of flow path substances with the metal substrate. In the example graph below, methanol (CH3OH) extracted metal ions from uncoated alloy surfaces. Metal ion extraction can contaminate flow path fluids and may result in system corrosion.
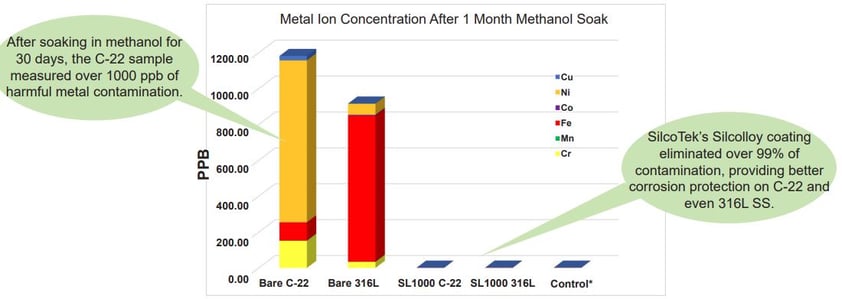
-
Anti-Fouling and Anti-Stiction: In processes involving fluid dynamics, heating, and cooling, SilcoTek coatings help by providing anti-fouling and anti-stiction surfaces. For example, coating shell-and-tube heat exchangers or condenser tubes helps to reduce fouling and provide enhanced thermal efficiency for much longer than uncoated alloys or overly-thick alternative coatings that degrade thermal conductivity. SilcoTek coatings reduce downtime, lower maintenance costs, and improve the ease of cleaning in fouling-, sticking-, or polymerization-prone applications.
For many heat exchanger applications, Calcium Sulfate (CaSO4) leads to increased fouling and pressure drops. Researchers at the University of Illinois Urbana-Champaign compared bare aluminum, Silcolloy 1000 coated, Dursan coated, and a competitor in 2L synthetic seawater and 5g calcium sulfate solution at 80° C. SilcoTek's Dursan coating performed well and improved pressure drop 74% in comparison to bare aluminum (blue line in the graph below).
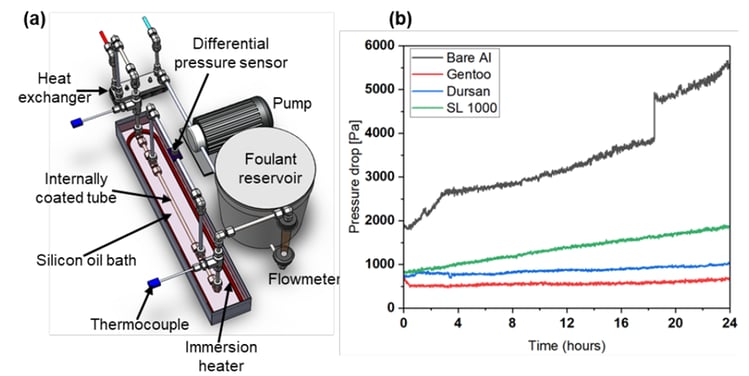
-
Hydrophobic and Hydrophilic Surfaces: The ability to tailor surfaces to be hydrophobic or hydrophilic allows for better control of fluid behavior in various applications. This is particularly useful in high-performance liquid chromatography (HPLC) and other separation technologies where precise fluid dynamics are necessary for effective analysis. See some of our coating contact angles below.
The comparative graph below highlights the water repelling properties of our coatings when compared to stainless steel. As presented below, SilcoTek's SilcoNert 1000, SilcoNert 2000, Dursan, and Notak all vastly outperform bare stainless steel when it comes to hydrophobicity.
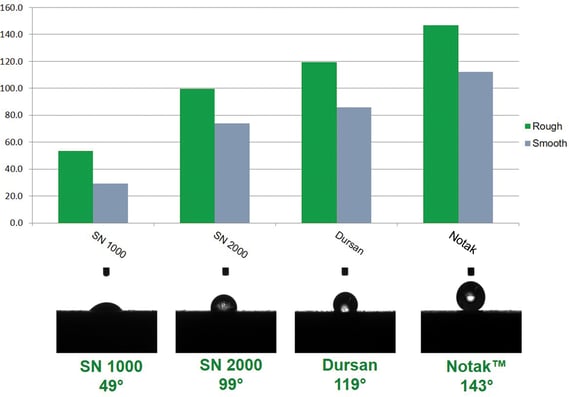
-
Enhanced Performance in Extreme Conditions: For the energy sector, including oil and gas, SilcoTek coatings provide enhanced performance under harsh conditions, such as high temperatures and corrosive environments. This extends the life of equipment and maintains the integrity of processes, which is essential for maintaining consistent production quality.
SilcoTek® coatings are stable to the following temperatures in an inert atmosphere:
*The values below reflect limits of the coating material itself and assume that the base substrate is stable at these temperatures.
SilcoNert® 2000 |
450 °C; 400 °C (oxidative atmosphere) |
SilcoNert® 1000 |
720 °C |
Silcolloy® 2000 |
800 °C |
SilcoGuard® |
720 °C |
SilcoKlean® |
450 °C (functionalization loss), 400 °C (oxidative atmosphere) |
Dursan® |
500 °C; 450 °C (oxidative atmosphere) |
Dursox® |
500 °C |
Notak® |
300 °C |
Overall, the integration of SilcoTek coatings in pharmaceutical and biotech applications at ACHEMA 2024 demonstrates a commitment to advancing the reliability and efficiency of processes through innovative surface modification technologies.
If you have any questions about SilcoTek, our coatings, or how we can help in your application, please reach out to us!