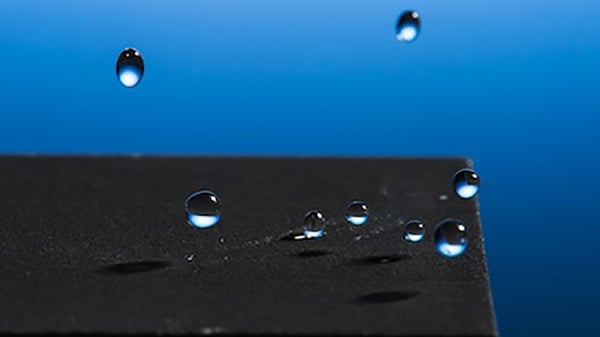
How to improve high temperature hydrophobicity and oleophobicity in demanding fuel injector and combustion applications? SilcoTek® answered the challenge by developing a new high temperature moisture and oil repelling coating able to remain stable at temperatures of 300c.
In this blog post you will learn:
- How SilcoTek's new Notak™ coating impacts surface energy, hydrophobicity, oleophobicity and fouling resistance
- How surface energy changes moisture resistance, hydrophobicity and oleophobicity
- The benefits of a hydrophobic coating surface
- The benefits of on oleophobic coating surface
|
SilcoTek's new coating, Notak™, achieved significant improvement in hydrophobicity and oleophobicity compared to the uncoated DLC surface. More impressively, the new coating remained stable when exposed to high temperatures for over 24 hours. Both hydrophobicity and oleophobicity contact angle were unchanged over the test period, indicating stable surface energy.
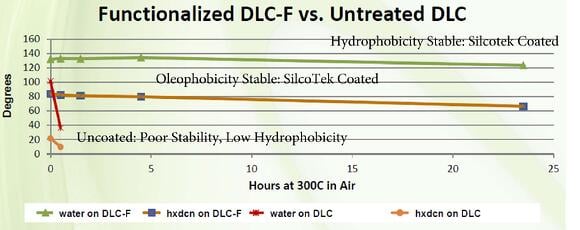
SilcoTek® coatings are the ideal hydrophobic and oleophobic solution to challenging environments. Applications include:
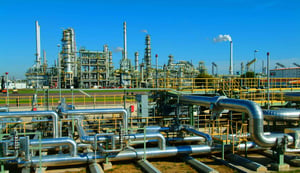
- Analytical sampling
- Refining/petrochemical
- Oil and Gas exploration and transport
- Automotive
- Aerospace
- Heat exchangers
- Process sampling
Have a question about this blog or high temperature hydrophobicity? Click the box below to discuss your application with one of our coating scientists.
Have a Question? Contact Our Technical Service Team
You can get lots of interesting information on how to prevent fouling and manage moisture resistance by viewing our webinar "Solving Surface Fouling with New Non-Stick CVD Coatings".
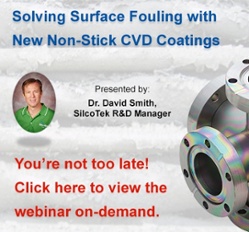
SilcoTek's inert, high durability, high tolerance coatings can be applied to high precision components used in the most demanding environments:
- Fuel injectors
- Nozzles
- Probes
- Separators
- Downhole tools
Learn more about SilcoTek hydrophobic coatings
About Hydrohobicity and Oleophobicity: a Comparison
A hydrophobic surface is a water repelling, low surface energy surface that resists wetting. Moisture contact angle measurements will classify a surface as hydrophobic when the contact angle of the water droplet exceeds 90 degrees. Exceed the 150 degree contact angle mark and the surface will be classified as superhydrophobic. Water will jump right off the surface as seen in this video.
There are many benefits of a moisture repelling surface. They include:
- Surface icing prevention |
- Condenser & evaporator fouling prevention |
- Improved corrosion resistance |
- Prevent moisture contamination in heat trace tubing |
- Produced water filtration & management |
- Improved reliability in continuous emissions monitors (CEMS) |
- Improved moisture detection instrumentation |
- HPLC medical diagnostics improved separation & corrosion resistance |
- Manage moisture contamination in liquid natural gas systems |
- Prevent contamination in analytical sample transfer systems |
How do I get a surface to match my desired moisture level of moisture resistance?
You don't have to make a super radical change to material or product construction in order to change the moisture performance. Fortunately we offer silicon barrier coatings with a wide range of water management capabilities. Want a more corrosion resistant or inert coating with a low surface contact angle? Try SilcoNert® 1000 or Silcolloy®. If you're looking for an inert coating that's not too moisture repelling, go with SilcoNert® 2000. Need maximum water repelling coating properties? Dursan® or our new Notak coating may do the trick. Note, our Notak coating is in pre-production Beta testing so we have limited capacity for that coating. Contact our Technical Service Team to discuss your application and we'll be happy to make a coating recommendation.
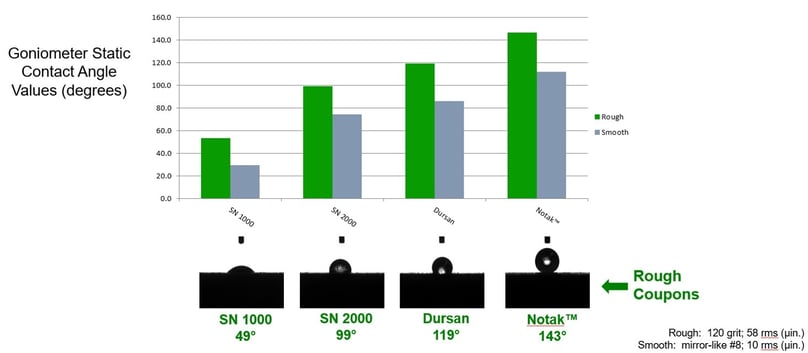
The comparative graph above highlights the water repelling properties of each of our coatings compared to stainless steel; each coating has specific applications and benefits. Go to our applications guide to get the lowdown on each of our coatings.
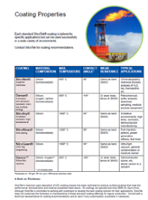
Hydrophilic Surfaces
Not to be outdone, hydrophilic surfaces have benefits as well. What are hydrophilic surfaces? They are high surface energy substrates that attract water and allow wetting of the surface. They typically have a droplet contact angle measurement of less than 90 degrees. Lots of surfaces tend to be more water friendly including, glass, steel, or stainless steel and many coatings and paints. Of course test results can depend on the surface roughness and surface energy of the material you're testing.
Learn How To Improve Moisture Resistance, Fouling Resistance, and Corrosion Resistance. Get Our Presentation.
Benefits of a moisture friendly surface include.
- Improved separation in medical diagnostics (application dependent) |
- Improved efficiency in heat transfer devices & heat exchangers |
- Improve acceptance of In-body devices |
- Improve surface interaction in filtration devices (application dependent) |
High Temperature Oleophobicity
Low surface tension liquids like oil or organic solvents are designed to wet the surface for maximum lubrication or solvation. But what if you're separating organics or don't want the surface to wet? Water repelling materials like PTFE aren't effective in repelling oil. Here's what oil and hexadecane look like when placed on a PTFE surface.
We bonded our new Notak coating on a rough stainless steel surface to see if the contact angle would increase. Notak made a big difference in contact angle, making the stainless steel an oleophobic surface.
Given the nature of refining or cleaning processes for that matter, we can expect the surface to be exposed to elevated temperatures. PTFE is high temperature limited and can fail in many high temperature applications. We exposed the Notak surface to elevated temperature (300°C) for several hours to gauge the impact to wettability, high temperature oleophobicity, and contact angle on various surfaces. The graph below shows consistent contact angle readings over the 90+ hour test. PTFE would have failed at 250°C.
The contribution of surface energy and it's relationship to process fluids can have far ranging impacts. Surface interaction can impact corrosion, fouling, analytical sampling results, filtration and medical device performance. So it's important to understand how to manage the energy of critical flow path surfaces.
Get some informative and helpful tips on ways to prevent fouling, change surface energy, & improve surface performance.
