Inert coatings prove their value every day.
SilcoNert® 2000 treated sampling and transfer equipment results in more accurate sampling and faster cycle times. SilcoNert 2000 treated sample pathways improve accuracy and reliability of data for sulfur, mercury, H2S and methyl mercaptan sampling.
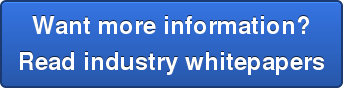
But treating a sample pathway increases component acquisition cost. It’s tempting to save some money by striking inert coatings from the material list, but at what real cost to the company bottom line? Let’s breakdown some real costs related to surface activity and poor surface inertness:
Loss of downstream process control:
If process instability (related to sulfurs or other active compounds) go undetected, a plant shutdown can lead to staggering costs. Even 1 hour of lost production can significantly impact profits.
Cost of a 1 hour shutdown relating to loss of process control by plant type:
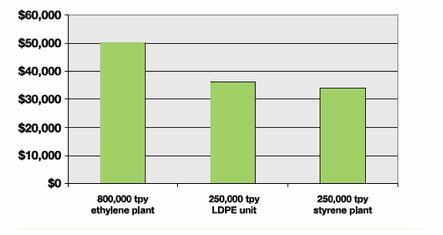
Contamination of downstream process streams:
Failure to detect sulfur in downstream process feedstock can be disastrous to plant profits. Replacement cost of common plant feedstock:
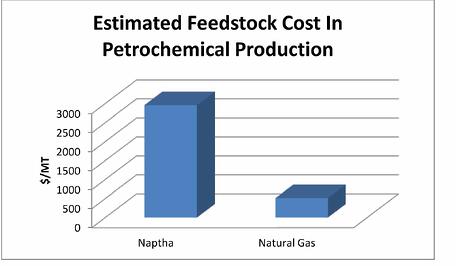
Inaccurate sampling:
False readings result in more sampling or testing. The average analytical cost per sample is approximately $30 to $35.00. Constant retesting can increase analytical cost by $130,000 or more per year. Inert coatings result in shorter sampling cycles which translate directly into more samples collected and analyzed in a given period of time. Process upsets can be detected faster while false readings can be eliminated.
So when calculating the cost of inert coatings, it becomes clear that you can’t afford not to add coatings to your material list. Learn more:
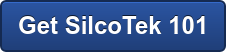