We get the question, "what does SilcoTek do?" quite often. Sometimes, we forget that there are people in the world who don't know what a CVD coating is (crazy, right?). This week, we wanted to get back to the basics and dive into how our process works for those who are new here.
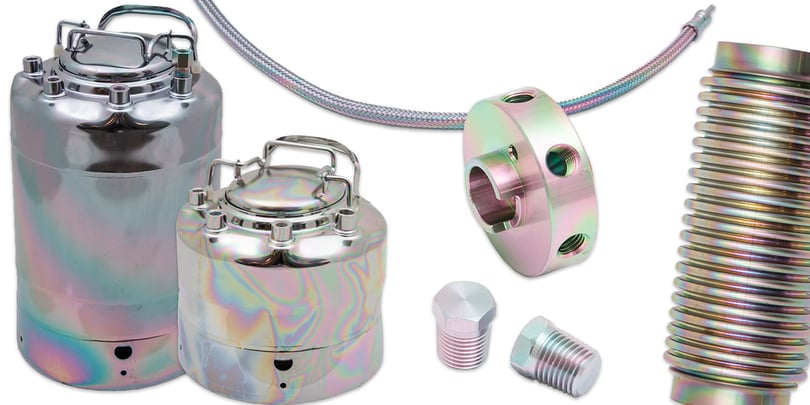
First of all, WELCOME! We're so glad you're here.
Opening our doors in 2009, SilcoTek is a state-of-the-art coating service facility located in the heart of central Pennsylvania, USA. We work with a team of talented researchers, manufacturing technicians, engineers, customer service, sales, marketing, quotes, quality assurance, HR, finance, and management. Our innovative CVD coatings improve the surface properties of materials our customers already use, allowing them to get better results from process instruments, run their equipment longer with less maintenance at lower costs, manufacture complex products more efficiently, and continue developing innovations that push the scientific and industrial world forward.We don't sell any products because we're solely focused on offering coatings that make your product better.
What is a CVD coating?
Chemical vapor deposition (CVD) is a process that involves the reaction of a volatile precursor which is injected into a chamber (typically under vacuum). The chamber is heated to a reaction temperature that causes the precursor gas to react or break down into the desired coating and bond to the material surface. Over time, the coating material builds on the surface and creates a coating throughout the exposed part's surface. So for example, if we wanted to bond silicon to a surface we may want to use a trichlorosilane precursor. (*NOTE: this is for example purposes only and does not represent a real SilcoTek coating process – visit https://www.silcotek.com/ip for a list of our patents). When the trichlorosilane is heated in the coating chamber, the decomposition and coating reaction may look like this:
SiHCl3 → Si + Cl2 + HCl
The silicon will bond to any exposed surfaces (both internal and external) while the chlorine and hydrochloric acid gas would be vented from the chamber and scrubbed according to appropriate regulatory requirements. The resulting coating is a thin, dense, conformal layer of the reacted material that is molecularly bound and grown out from the substrate material. In the magnified focused ion beam (FIB) image below, our Siltride® coating – a silicon oxynitride material – is highlighted in green on top of a stainless steel sample coupon.
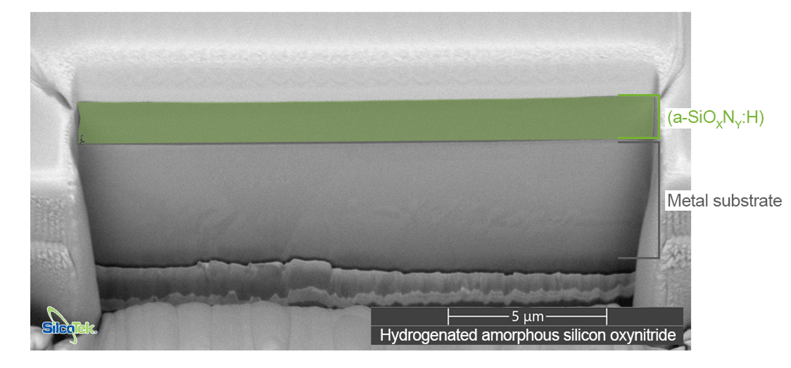
The image above shows a smooth, thin, and uniform layer of Siltride®, a hydrogenated amorphous silicon oxynitride coating, deposited onto the metal substrate.
CVD coatings are prevalent throughout industry and can be found in many consumer products. They're known as being an environmentally friendly durable thin film surface. CVD products can be found in applications ranging from machine tools, wear components, analytical flow path components, instrumentation and many other areas demanding a high performance thin film.
How does our process work?
After receipt, SilcoTek uses proprietary surface preparation methods to ensure the highest quality coating. It is important to note that any surface characteristics, such as scratches, rough textures, or varying surface qualities, will become more apparent after the coating process. Therefore, creating a pristine, contaminant-free surface prior to coating is essential for achieving optimal results and a visually appealing finish. Metal working and machining processes can sometimes leave behind contaminants that are not visible to the naked eye. To help us achieve the best possible outcome, please provide details on the treatments and processes your parts have undergone before sending them to us for coating.
The surface preparation process begins after receipt.
After a thorough surface preparation, our technicians load customer parts into a vacuum vessel corresponding to the size of the parts. This vessel is placed in a large oven and connected to the raw material - gas - then heats to temperatures near 400° C. Throughout this process, a proprietary blend of gas enters the vessel and starts a reaction which diffuses the treatment into the molecular lattice of the substrate, forming the ultra-thin SilcoTek coating that so many have come to recognize and trust.
With our process, 100% of your parts are coated, even if the design is intricate or the pathways are complex.
Parts are then loaded into an oven for processing.
Once the coating process is complete, your parts are unloaded and moved to the inspection area. SilcoTek Technicians then visually inspect each part to ensure conformal thickness and proper aesthetics and then review coating run data to verify all process parameters meet specification. Parts that pass inspection are issued a coating certification adherent to ISO 9001.
Thorough quality inspection after coating.
See our coating process video below!
Why are coatings important?
SilcoTek coatings are crucial across many industries due to their exceptional properties and the diverse range of benefits offered. One major advantage is their outstanding resistance to corrosion, which is essential for components operating in harsh environments. This resistance significantly extends the lifespan of these components and reduces maintenance costs. In addition to corrosion resistance, the chemical inertness of SilcoTek coatings means they do not react with most substrates, making them indispensable in fields like chemical processing, pharmaceuticals, and oil and gas, where equipment is regularly exposed to reactive and hazardous materials.
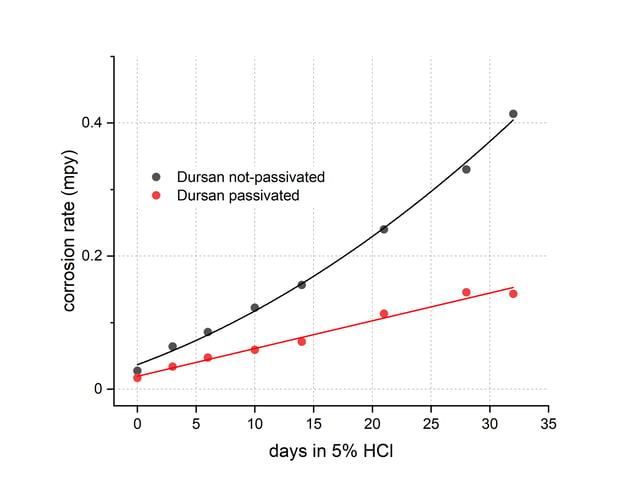
SilcoTek’s Dursan® coating improves stainless steel’s lifetime in aggressive 5% liquid HCl conditions. Passivating the stainless steel surface before Dursan-coating it provides even greater protection over time, adding greater value to an investment in coating.
Our coatings are also renowned for their ability to withstand high temperatures without degradation, making them suitable for high-temperature environments such as those found in aerospace, automotive, and various industrial processes. Their non-stick and anti-fouling properties prevent the accumulation of materials on surfaces, which is particularly beneficial in food processing and the oil and gas industry, where maintaining cleanliness and efficient operation is critical. Additionally, SilcoTek coatings improve the flow of fluids through pipelines and equipment by reducing friction, which is essential for efficient transport and processing in petrochemical industries.
The improved Silcolloy 2000 process allows customers to experience high-temperature stability in their applications. The amorphous silicon layer avoids oxidation at high temperatures to improve and prolong performance.
In analytical and laboratory settings, the inertness and non-reactive nature of SilcoTek coatings ensure that samples remain uncontaminated, leading to more accurate and reliable results. Their biocompatibility makes them suitable for medical devices, ensuring they do not cause adverse reactions in the body. Furthermore, the hydrophobic nature of some SilcoTek coatings prevents water and other liquids from adhering to surfaces, which is advantageous in applications requiring moisture control, such as in semiconductor manufacturing.
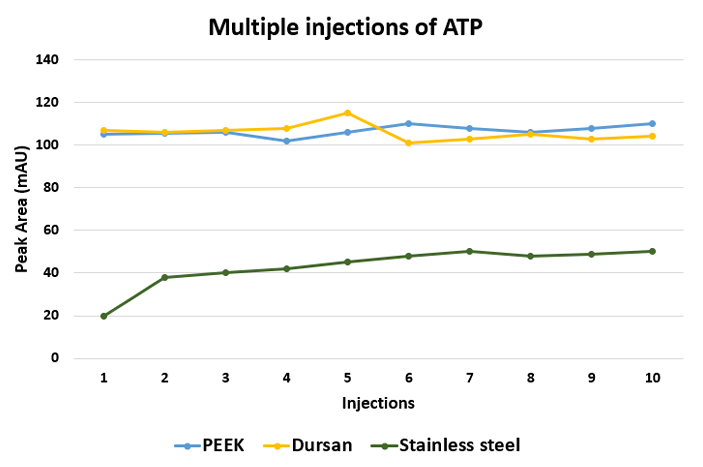
Dursan-coated stainless steel performs as well as the inert polymer PEEK for reducing unwanted metal activity in sensitive liquid chromatography applications.
From an environmental perspective, these coatings contribute to sustainability by extending equipment life and reducing waste and resource consumption. Overall, the versatility and efficiency improvements offered by SilcoTek coatings make them an invaluable asset across a wide range of industries, enhancing performance, reliability, and cost-effectiveness while minimizing environmental impact.
Have questions about SilcoTek, our process, or our coatings? Please reach out to our coating experts!
Follow Us on Social Media!
