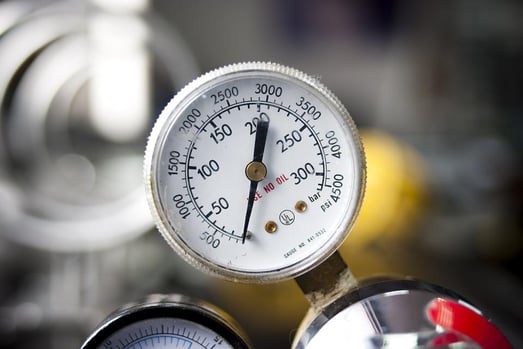
Pressure gauges have been around for a long time. So why are they hard to coat? We discuss pressure gauge basics and why they're not coated.
Challenges to Coating Pressure Gauges
The most common modern pressure gauge was invented in 1849 by Eugene Bourdon. Leave it to the French to come up with an elegant and durable design that withstood the test of time. In this blog post we'll discuss the basic design elements of the Bourdon tube pressure gauge and discuss insights about why they're generally not coated.
In this blog post you will learn:
- How the most common pressure gauges work.
- Why they're prone to failure after coating.
- Challenges to coating Bourdon tubes.
- Corrosion resistance and future gauge design.
|
Bourdon Tube Pressure Gauge Design
The commonly used pressure gauge consists of just a few parts. A curved tube that's sealed at one end and connected to a link that in turn is connected to a pivot arm that has teeth at one end. Those teeth act as a gear that turns a small toothed wheel that is connected to a needle. The design is simple and elegant. As pressure builds within the tube, forces will begin to straighten out that curve. As the tube straightens, the pivot arm will move the needle and indicate a change in pressure. The key to precisely measuring pressure is the Bourdon tube. If the tube curve is off or if the tube cross section, material thickness, or quality varies, the pressure will not be accurately displayed.*
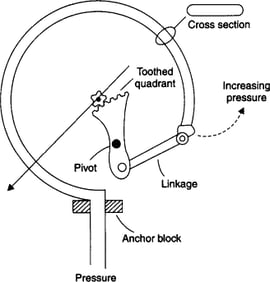
The tube material and tempering method (called spring tempering, a heat treating method that retains shape and elasticity) are critical to the precision and accuracy of the gauge. Materials that are particularly suited for Bourdon include:
- Stainless steel
- Beryllium copper
- Steel alloys
- Phosphor bronze

Tube selection depends on several factors including cost, desired level of corrosion resistance, and pressure requirements.
Factors that can alter the performance of pressure gauges include:
- Change to the tube arch due to shock or physical damage.
- Perforation in the tube.
- Damage to the gear or pivot mechanism.
- Excessive heat which affects the heat treating of the tube.
- Corrosion of the tube or mechanism.
- Failure of the soldering or brazing at the tube/socket interface.
Coating Gauges
Our chemical vapor deposition (CVD) process involves the application of silicon and other non reactive materials to the part surface under heat and a range of pressure conditions. This process can result in potential damage to the gauge. Here are some factors to consider.
Heat
Coating gauges involves processes that can potentially affect the performance of the gauge. Our coating process involves heating the part ( to approximately 400°C). Heating the part may alter the heat treating properties of the metal tube. That heat may also damage the soldering or brazing at the tube/socket interface. This could result in a leak in the gauge.
If the entire gauge mechanism is coated, the heat exposure during processing may also damage the pivot or the coating may interfere with the gear mechanism.
Coating Deposition
Our CVD coatings are very thin but they do slightly change the mass and thickness of the surface. The coating itself may slightly change the rate at which the tube curve changes. This may also throw off the gauge accuracy.
Physical Damage During Disassembly or Assembly
Pressure gauges appear to be very simple mechanisms but shock or handling during processing or customer disassembly or assembly can result in a change in gauge calibration or accuracy.
Generally speaking the potential of gauge damage plays a big part when considering coating a gauge. For the most part we'll recommend not coating a gauge rather than risk damage to a customer part.
Learn more about the properties and benefits of SilcoTek coatings. Go to our FAQ page.

Potential Option
There may be a option to coat gauges with our new Notak® coating. Notak is applied at a lower temperature and does have water repelling and anti fouling properties. Notak may not offer significant inertness or corrosion benefits. Testing in the application would be required as there is still the potential for loss of calibration and gauge damage during processing.
Newer gauge technologies involving electronic components that provide a signal to a processor may have the potential for coating if the individual gauge components are coated prior to assembly. We are not able to coat electronic components but, depending on the gauge design, we may be able to coat wetted components before assembly. Again, we recommend testing the coated part before use and there may still be a risk of damage to the gauge or a change in performance as a result of coating.
We recommend discussing your application with our Technical Service Team before considering coating a gauge. We'll be happy to help and provide any information relating to your application.
Want to learn more about our coatings and how they can improve the performance of your products?
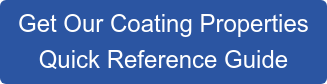
Coating Corrosion Resistance and Inertness
Gauges make up a very small portion of the wetted flow path. To improve the corrosion resistance and inertness of tubing, fittings, and valves; SilcoTek® offers a wide range of performance coatings. SilcoTek coatings help to prevent common inertness and corrosion related problems including:
- Frequent component replacement
- Process or product contamination problems
- Sample probe damage and failure
- Lost productivity due to excessive downtime or test errors
|
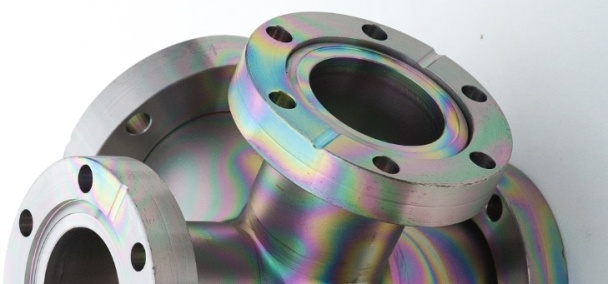 |
ASTM immersion testing proves SilcoTek® coated stainless steel enhances corrosion resistance by orders of magnitude, matching the performance of super alloys in many applications. Even after immersion in concentrated hydrochloric acid (below) the Dursan® and Silcolloy® coated stainless steel coupons continue to perform with minimal corrosion, demonstrating performance comparable to super alloys.
/astm%20g31.png?t=1570811309696&width=495&name=astm%20g31.png)
SilcoTek coatings perform in a variety of corrosive environments including sulfuric acid and bleach.
Comparative Corrosion Summary |
|
|
|
Stainless Steel Corrosion Rate (mpy) |
Dursan Coated Stainless Steel (mpy) |
6M Hydrochloric Acid, 24 hr exposure |
160 |
1 |
25% Sulfuric Acid, 24 hr exposure |
55 |
5 |
52 Week Salt Spray |
<0.01 |
<0.01 |
Bleach |
1.7 |
0.1 |
About Notak®
Notak® is SilcoTek’s most hydrophobic and oleophobic surface treatment, using an organo fluoro surface functionalization of the substrate to drastically lower surface energy (patent info at www.silcotek.com/IP). Applied via chemical vapor deposition (CVD), the Notak® process directly enhances surfaces to resist unwanted build-up of water, oils, sticky hydrocarbons, and other foulants to improve performance.
Key Applications and Benefits
- Increase hydrophobicity and oleophobicity
- Improve mold release
- Prevent surface fouling
- Stable performance up to 300°C

To learn more about how our coatings can improve the performance our your products, go to our Coating Applications page or contact our Technical Service Team. To stay in touch with the latest in coating technology, follow us on LinkedIn or subscribe to our blog.

* Image courtesy of Science Direct.com. https://www.sciencedirect.com/topics/engineering/bourdon-tube
Read more about pressure gauge construction: http://www.madehow.com/Volume-1/Pressure-Gauge.html#ixzz7YHyShbah