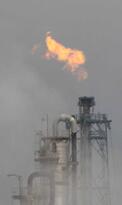
Phil Harris, Senior Scientist at Haritec, & O'Brien Analytical recently published a paper outlining opportunities to improve both hydrofluoric acid (HF) corrosion resistance and low level sulfur sampling in flares required by EPA 40 CFR part 60, subpart Ja.
The study emphasizes the importance of improving sample reliability in alkylation units, especially considering the potential of hydrofluoric acid (HF) exposure. HF corrosion not only will reduce system life and increase maintenance/replacement cost; but will also increase sample and transfer system activity. Active surfaces will adsorb sulfur species, significantly impeding low level sampling of H2S, sulfurs, and ammonia.
The study compares materials commonly used in sampling. SilcoNert® 2000 coated stainless steel is the common solution to improving low level sulfur and ammonia sampling. HF exposure will eventually erode the SilcoNert 2000 surface, corrode the stainless steel, & consequently will make the sampling system surface active.
The study recommends SilcoNert® 2000 coated alloy C-276 to maximize both corrosion resistance and inertness. Alloy C-276 demonstrates significant corrosion resistance (see graph) while the SilcoNert 2000 coating assures industry leading H2S, sulfur, and ammonia inertness (see table).
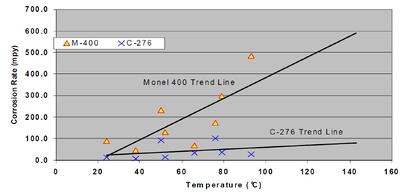
The study states:
"Monel 400 also does not accept a SilcoNert 2000 coating very well, resulting in poor coating uniformity. By contrast, alloy C-276 is naturally more resistant to sulfur species, can be chemically polished and will accept a uniform SilcoNert 2000 coating."
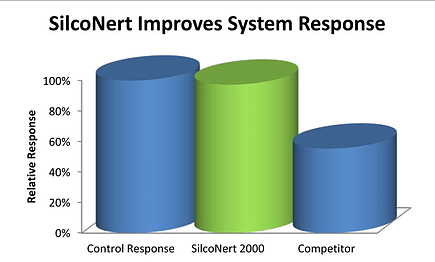
Read the full study.
Learn more about how SilcoNert® 2000 and SilcoTek® coatings Improve sulfur inertness in flare systems.