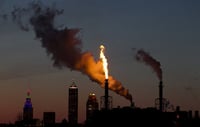
Refinery, flare & stack sampling can be a difficult and sometimes maddening task. Long calibration times, loss of sample, and inaccurate sampling can all lead to premature gray hair. The leading causes of premature aging of compliance and process engineers are sulfur, mercury and ammonia sampling! And teenagers...

Here are some helpful tips on how to improve process sampling and hopefully avoid gray hair. Sorry no help with teenagers.
Go inert
Part-per-billion or low part-per-million level analysis of ammonia, sulfur or mercury can be unreliable due to flowpath adsorption. Stainless steel, glass ceramics and quartz can be highly adsorptive; preventing accurate analysis. The lower the sensitivity, the more adsorption will factor into reliable sample measurement. Fluropolymer sealing materials can also react with the sample or outgass and cause contamination of the sample stream.
An inert silicon barrier coating is a proven solution to adsorption issues. Studies, like the ammonia whitepaper by the University of Helsinki, show reactive compound adsorption is minimized with silicon coatings.
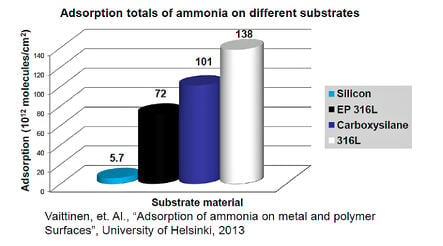
Watch for signs of ansorption in the sample system. Adsorption indicators are:
- Lost peaks, peak distortion
- Slow signal response
- Slow or no calibration signal
- Unexplained spikes in results (desorption)
Get more whitepaper studies on sulfur, ammonia and mercury adsorption.

Keep it Smooth
Analyte from flare sampling can get trapped in porous or rough surfaces. Stainless steel and PTFE tubing can trap and accumulate adsorptive moisture and test analyte. The trapped compounds can be a source of additional adsorption or can later desorb, causing a spike in test results. The smoother the tubing, the less likely materials will be trapped in the flow path. A smooth surface will have less surface area and less chance of contact with the sample. Optimizing and improving sample quality and reliability. 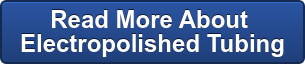
Electropolished heat trace silicon coated tubing adds unmatched value for analyzer installations improving results and system durability:
- Chemically inert sample path
- Reduced carryover contamination
- High Temperature (450° C)
SilcoNert coated electropolished stainless steel tubing offers nearly 100% recovery of the flare sample while conventional stainless steel adsorbs nearly all the sample.*
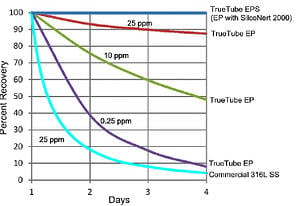
*data courtesy of O'Brien Corporation
Say no to copper, aluminum, carbon and stainless steel.
H2S and sulfurs will be scrubbed from sample streams that contain high copper alloys such as Monel® & Brass. Monel is commonly used in hydrofluoric acid sampling but if Monel is used in sulfur, ammonia, or mercury sampling the results can be distorted by rapid adsorption. Loss of the target sample can occur within hours for most commonly used sample flowpath materials including stainless steel, aluminum, and carbon steel.
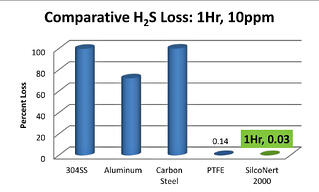
For HF sampling we recommend using Hastelloy® sample cylinders coated with SilcoNert® 2000 for optimum performance.
Learn more about how SilcoTek® coatings perform.
Know where & what you're sampling
Studies and presentations by Welker Engineering (www.welker.com) have shown that the sample point is critical to getting a representative sample from flare, stack and process streams. Test results show the optimum probe location is:
- Away from the wall
- Away from turbulent flow
- From center of stream if possible
- Away from any flow disruptions
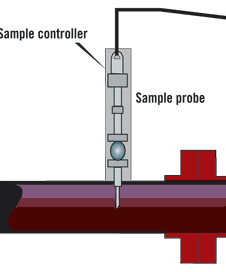
Don't let corrosion get the best of you
Corrosion not only damages system integrity, it's a source of active and adsorptive particles. SilcoTek® coatings reduce corrosion by orders of magnitude while preventing adsorption of sulfur compounds. SilcoTek coatings offer both inertness and corrosion resistance, keeping test results and the sample system flowpath reliable for years.
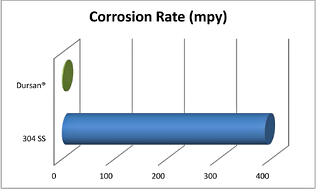
Remember that experts at all OEM's deploying improved equipment are there to help recommend the best solution for your application. SilcoTek has teamed up with industry leaders to offer inert coated products for flare, process and stack sampling. Go to our Coated Products page to find experts in each component of a flare sample system.
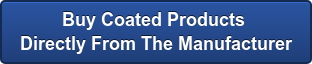