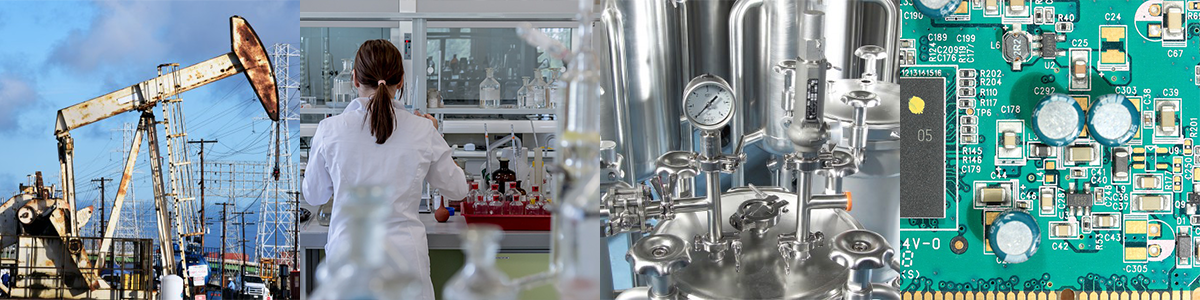
Can SilcoTek coating be used in oxygen service applications? We discuss oxygen service cleaning, cleaning methods, and coating compatibility with oxygen.
Can SilcoTek Coatings be Used in Oxygen Service?
Occasionally, customers have inquired whether parts coated by SilcoTek are certified for oxygen service. SilcoTek® coated parts are not certified for oxygen service, nor does SilcoTek endorse or provide certification as an option for their customers. Read on to learn more about oxygen service and cleaning.
In this blog post you will learn:
- What constitutes oxygen service cleaning requirements.
- Why SilcoTek® coatings are not recommended for oxygen service.
- Sources for standards for oxygen service cleaning and stainless steel cleaning.
|
What is Oxygen Service Cleaning and What Triggers Oxygen Clean Requirements?
If the gas flow within a flow path contains more than 23% oxygen, that stream is oxygen rich and triggers the requirement for all surfaces exposed to that stream to be cleaned for oxygen service.
Want to learn more about how our coatings can improve the performance of your products? Click the box below to subscribe to our informative emails and blog.

The cleanliness standards required for safe oxygen service are demanding, and depending on the certification body required, can be varied and confusing. The Precision Companies, a company that offers oxygen cleaning services and certification, says the following about oxygen cleaning:
"What Is Oxygen Cleaning?
Oxygen system cleaning (or “oxygen cleaning”) involves using different techniques, equipment, and solvents to remove contaminants from oxygen service equipment. Oxygen cleaning techniques are unique because they use oxygen-compatible solvents and specially designed equipment and processes to ensure the safe and complete removal of hazardous and potentially fire-causing contaminants.
Several different governing bodies regulate the solvents, equipment, and processes used in oxygen cleaning, as well as the standards for industrial oxygen system cleanliness in different sub-sectors. This includes the Compressed Gas Association (CGA), the Institute of Environmental Services and Technology (IEST), ASTM International (formerly the American Society for Testing and Materials), SAE International (the Society of Automotive Engineers), and NASA’s Kennedy Space Center (KSC)."
As you can see there are lots of standards and methods out there for oxygen service cleaning. But you'll notice if you read the standards none of them will definitively tell you exactly how to clean oxygen flow paths for your application. That's because the exact method used will depend on the contaminants involved. Selecting the right process and cleaning solvent used is critical to the effectiveness of oxygen cleaning.
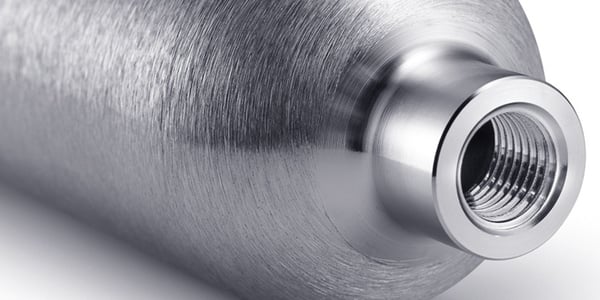
To compound the problem, oxygen clean standards are similar but not identical in their recommendations. Now the various organizations involved with oxygen cleaning are beginning to revise their standards to a more unified set of requirements. As the standards are revised, companies will need to pay close attention to the requirements of the revised standards and may be required to modify processes or replace/re-clean components in order to meet the revised standard. Learn more about coating care and cleaning tips, click the box below to download our Coating Care Presentation.
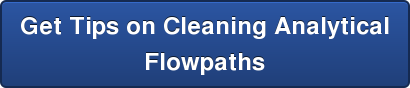
Cleaning Methods
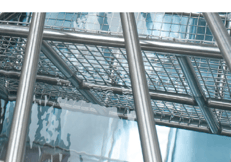
The many oxygen clean standards available specify various methods for cleaning surfaces. Cleaning methods or processes may include:
- Ultrasonic cleaning
- Steam cleaning
- Cleaning with an acid or base solutions
- Solvent cleaning
- Vapor degreasing
- Physical removal of contaminants by mechanical cleaning methods
- Thermal cleaning or hot water cleaning
The method employed will be dictated by the nature and chemical composition of the contaminants, the flow path materials involved, and form factor of the part being cleaned.
Cleaning Results
One of the more cited standards for oxygen service cleaning is CGA G-4.1. That standard sets the criteria for acceptable cleaning results. The Penflex website highlights and cites the CGA standard for post contaminant levels in oxygen cleaning processes. Final clean specifications should be established with the oxygen cleaning service provider and should reflect the requirements of the application. The Penflex website cites the CGA standard for oxygen clean acceptance criteria as:
“An acceptable contamination level for oxygen service equipment is approximately 47.5 mg per ft2 (500 mg/m2) but could be more or less depending on the specific application (state of fluid, temperature and pressure). If the purchaser’s requirement includes a particle and fiber count, a representative square foot section of surface shall show no particle no larger than 1000 microns (.0384″) and no more than 20 particles per ft2 (215 particles/m2) between 500 and 1000 microns. Isolated fibers of lint shall be no longer than 2000 microns and there shall be no accumulation of lint fibers.”
Even this criteria leaves a lot of room for acceptance. It's up to the user, in conjunction with oxygen cleaning specialists to determine the exact acceptance criteria for your application.
Why is it Important to Clean Oxygen Exposed Flow Paths?
There's a distinct fire danger associated with oxygen. Oxygen is not in itself flammable but oxygen is needed for fire to occur. Oxygen enriched environments will lower the ignition temperature of combustible materials. Oxygen is a highly effective oxidizer, in high concentrations, it can cause simple materials like dust, carbon particulates, or lint to explode or catch fire.
Fire occurs when oxygen, fuel, and heat energy (e.g., a spark) combine. Pure oxygen environments, therefore, require the absence of a fuel, like a hydrocarbon-containing material, and heat energy. Additionally, materials are easier to ignite at higher pressures and/or rapid flows of oxygen, which can be the case for oxygen service coming from a compressed gas cylinder. The presence of particles can be the cause of static discharge (spark) or from particle impact that strikes a material and generates heat. To summarize, it is very important with oxygen service to exclude any hydrocarbon contaminants and particulate matter, particularly in compressed and/or high-flow oxygen delivery systems.
Can SilcoTek® Coatings be used in Oxygen Service and Are There Byproducts from SilcoTek Coatings?
Unfortunately, for SilcoTek processes such as SilcoNert® 2000, SilcoKlean® 1000, Dursan® and Notak®, hydrocarbons are present in either the surface functionalization or the bulk of the deposition. And except for Notak, all other SilcoTek processes generate particles, that although are visually removed post-processing, are still present at a microscopic level.
Because of the presence of hydrocarbon, particles, or both on SilcoTek-treated parts, it is not recommended to clean a SilcoTek coated part in preparation for oxygen service certification. As a result, SilcoTek discourages using parts coated by SilcoTek for oxygen service. However, customers are encouraged to conduct testing to best understand appropriate limitations of the coated parts.
Have a question about our coatings and how they can improve the performance of your products? Contact our Technical Service Team, go to our FAQ page, or follow us on LinkedIn.
