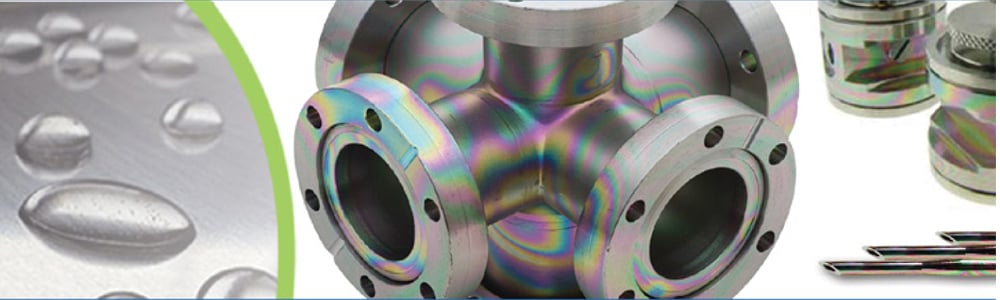
In part 2 of our our blog post on vapor cleaning and surface roughness, we compare corrosion rate of coated surfaces, with interesting results.
Will Surface Roughness Change Corrosion Resistance of Coated Surfaces
In part one of our blog post we discussed the impact of vapor stripping on aluminum, stainless steel, and other surfaces. The vapor stripping process is not part of our surface preparation process for any material but may be an option if customers elect to use a more aggressive surface preparation when a non alkaline cleaner is needed, or if a change in the part surface or surface morphology is needed.
In this blog post we compare the corrosion resistance of a coated vapor stripped surface and a coated mirror polished surface. We'll learn if a vapor cleaned or stripped surface changes the corrosion resistance of the part.
In this blog post you will learn:
- How mirror surface roughness compares to a vapor stripped mirror surface.
- How coated surface corrosion resistance is affected by vapor stripping.
- How to test and evaluate corrosion resistant coating and compare surfaces for corrosion resistance.
|
Background
In part one of our blog post, we investigated the impact of vapor cleaning primarily on two metals, i.e. aluminum 6061 alloy (6061-Al) and stainless-steel 316 alloy (316-SS). 6061-Al was chosen because it is the most commonly used general purpose aluminum alloy and represents the majority of the aluminum parts SilcoTek® encounters. 316-SS serves as a reference metal that is mechanically harder than aluminum and represents one of the most common substrate materials processed by SilcoTek. A variety of starting surface finishes ranging from mirror polish to mill finish were evaluated. Go to our previous blog post to read more about the surface evaluation.
Vapor cleaning, or vapor stripping, is a technology that uses a mixture of abrasive particles and pressurized water to clean, strip, and finish a surface. It is essentially a wet and gentler version of “blasting” that removes less material and creates a smoother surface finish than traditional dry blasting methods. SilcoTek does not utilize this method in our process but customers may use this or similar surface preparation methods as part of their process. More information about the technology can be found on this website.

Surface Roughness Comparison
Surface roughness and depth profile before and after vapor cleaning were measured using a Zygo Nexview 3D optical surface profiler. High magnification surface images were taken with a Thermo Fisher Scientific Apreo S Scanning Electron Microscope (SEM). The SilcoTek R&D Team would like to thank and acknowledge the Materials Characterization Lab at Penn State University for granting access to these instruments and for providing technical support.
The surface images below compare aluminum and stainless steel mirror polished surfaces before and after stripping. The vapor stripped surface for both materials show a consistent increase in surface roughness with roughness on the scale of 0.5 ~ 1 µm. A smoother starting surface results in slightly smoother end finish, and stainless-steel surfaces generate slightly smoother end finishes than corresponding aluminum surfaces with similar starting roughness, but overall roughness is similar as can be seen in figures 1 and 2 below.
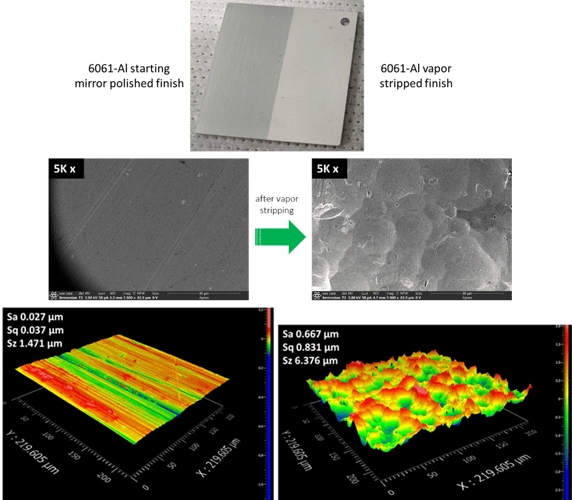
Figure 1: Surface comparison before and after vapor cleaning for a mirror polished aluminum sample.
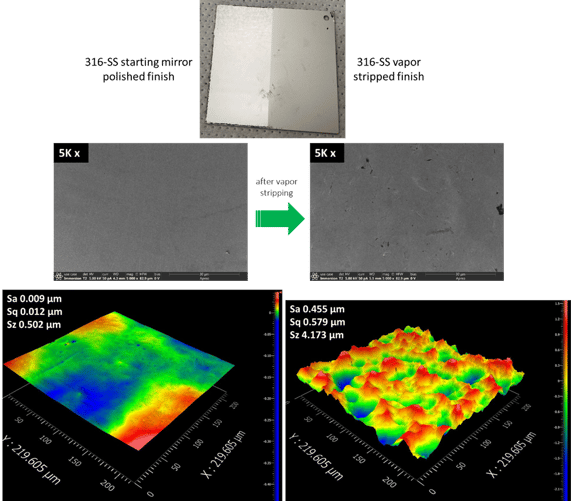
Figure 2: Surface comparison before and after vapor cleaning for a mirror polished stainless steel sample.
Corrosion Resistance Comparison
Corrosion resistance of the aluminum and stainless steel samples was measured in 5% hydrochloric acid (HCl) solution using a linear polarization resistance scan. The corrosion rate values were calculated based on the corrosion current values measured during the scan. Figure 3 plots and compares the control mirror-polished samples and vapor stripped samples (all coated with Silcolloy®) on aluminum and stainless-steel coupons.
The measurements were taken after 20 minutes of exposure to hydrochloric acid (HCl) for aluminum, and 60 minutes of exposure for stainless steel. Coating on vapor stripped samples delivered comparable corrosion performance in HCl as the control samples.
Figure 3: Corrosion performance of the Silcolloy® coating is not significantly affected by vapor stripping, demonstrated by similar corrosion rates measured on control mirror-polished samples versus vapor stripped samples. Each group contains at least ten samples to gain a statistical spread.

Conclusion
The results above show a slight increase in the median corrosion resistance rate for vapor stripped vs. the control. But the overall range of the corrosion rate of the samples is comparable and within the pass fail criteria for the study. The increase in corrosion resistance is marginal and has minimal impact on performance.
Previous studies have shown some increase in the corrosion rate of rough surface coated parts vs. smooth surfaces. Read that comparison to learn more about how the corrosion rate is affected by rough surfaces. That study compared the corrosion rate of electropolished and standard mill-finished non electropolished surfaces, which represents a larger difference in surface roughness than what were compared in this current study. In addition, the chemical passivation effect from electropolishing further enhances the corrosion resistance of surfaces. These factors may explain why a more pronounced positive impact was observed from electropolishing, whereas little negative impact was measured from vapor stripping.
Have a coating corrosion question about your products or processes? We're here to help you get the most out of your process and products. Contact our Technical Service Team to discuss your coating application. To keep up with the latest in surface science and coatings, follow us on LinkedIn or subscribe to our email and blog.