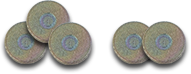
SilcoTek® CVD coatings like SilcoNert® and Dursan® are used in analytical column, metal capillary column analysis, sulfur analysis and process systems. But can they be used to improve corrosion resistance and inertness in sintered metal frits or metal filters without clogging the filter? Let's find out.
Background:
Sintered metal frits are made by pressing powdered metal together and heating the pressed material up until the discrete metal particles are fused into a tortuous network of pores and channels. Frits are used in a variety of industries for their ability to filter out unwanted particulate, or to keep particles in place during operation. While there are many benefits to using a metal sintered frit due to their robust nature, the metal they are made from is often too reactive for efficient use. Issues such as filtered particles sticking to the metal surface and clogging the frit or reactive molecules being adsorbed to the frit internal network are common. SilcoTek’s corrosion resistant, anti-fouling and inert coatings can offer a barrier between the metal in the frit and the reactive material.
In this blog you will learn:
- The big difference between CVD and PVD coatings.
- How SilcoTek coatings like Dursan and SilcoNert can penetrate small areas like sintered metal filters.
- How thoroughly do SilcoTek coatings coat filters?
- Do SilcoNert or Dursan coatings block fritted filter pores?
|
Coating a frit via common coating techniques such as paints, epoxies, or PVD is not trivial. Common challenges include complete coverage of all the internals, including blind holes, depositing a thin enough coating as to not block the pores and allow the frit to still act as a filter, and consistent coating throughout the frit’s inner network. In this blog post will discuss SilcoTek’s CVD coating technique and how it addresses these concerns for the coating of frits. Want to get all the data? Read the complete study.

In a previous study, we discussed the coating of a 2 µm sintered stainless steel frit with SilcoNert® 2000. Briefly, we saw that it conformally coats all of the internal networks of the frit, and the coating thickness ranges from 50 nm to 80 nm. SilcoNert 2000 is not the only coating that we apply to fritted materials. Dursan has increased in popularity as a coating for fritted materials due to its anti-coking properties in coal gasification systems as well as its general inertness and corrosion resistance in analytical equipment. As Dursan and SilcoNert use very different precursor gases, the question was raised: will Dursan® coat the internals of a fritted material as well?
Does the coating penetrate the entirety of the frit?
This is the most common question asked when discussing the coating of a frit, as many coating techniques are “line of sight”. As described in Figure 1, SilcoTek’s CVD coating is considered non-line of sight, meaning that it can penetrate into tortuous networks and coat blind holes where other techniques such as PVD can only coat areas that point in the direction of the deposition source.
Figure 1: A CVD coated part will be conformally coated around the entirety of the part, while a part coated via a “line of sight” method such as PVD only coat areas that are facing the source of the coating. This will leave areas uncoated and exposed to the environment around the part.
Does the coating block the pores?
SilcoTek’s coatings are typically hundreds of nanometers thick. When a customer is looking at applying our coating to a frit, this number rightfully causes hesitation. If a frit has an average pore size of 2 µm, a 500 nm coating will cut the average pore size in half. This can lead to serious back pressure issues for the customer. Fortunately, this specification of our coating is for flat solid surfaces. On a part like a frit which has a very high surface area to volume ratio, this thickness will be much lower on internal surfaces. The 2 µm frit described above that was coated with our standard SilcoNert 2000, had an internal thickness range of 50 to 80 nm as measured with a Filmetrics F40 film thickness measurement tool. Customers should be aware that the application of our coating may require a slightly higher pressure to accomplish the same flow through the frit, but not to a significant degree. This can be confirmed utilizing a flow/bubble point test.
Is the coating consistent through the entire frit?
When an amorphous silicon deposition is under a micron thick, a slight variation in thickness can cause a dramatic change in color. When a flat surface is exposed to process gas at high temperatures, things such as fill dynamics of the gas, slight temperature variations in the part, and surface roughness can all cause the growth rate of the coating to vary slightly. This is why our typical coatings have a rainbow-like appearance. Figure 2 shows a cross sectional photo of the frit after it has been broken in half. There are three distinct colors in the frit: gold which measures ~50 nm, pink which measures ~65 nm, and blue which measures ~80 nm. Raman spectroscopy was performed to ensure that the material that was deposited on the inner most portion of the frit was the same as the material on the exterior, and it was confirmed that the coating is an amorphous silicon coating, which is what makes our SilcoNert 2000, and Dursan coatings.
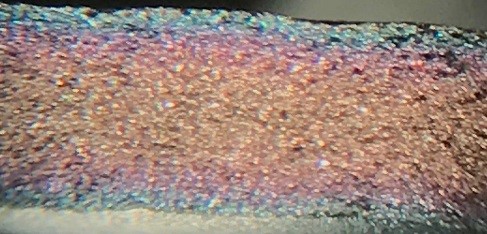
Figure 2: Cross section of a frit that was coated with SilcoNert 2000. While there is a gradient of thickness from the center of the frit to the edges, the difference in coating thickness is only about 30 nm from the center to the edge.
Discussion / Data / Links:
A 2 µm stainless steel frit was coated with Dursan using our standard process recipe. The frit was then broken in half to expose the internal network of the frit. Figure 3 shows an electron micrograph of the inner workings of the sintered frit. As noted above, this network would not be trivial to coat via traditional methods such as PVD, paints, or epoxies as they are line of sight techniques. Our CVD technique is non-line of sight and can penetrate the tortuous network of a sintered frit.
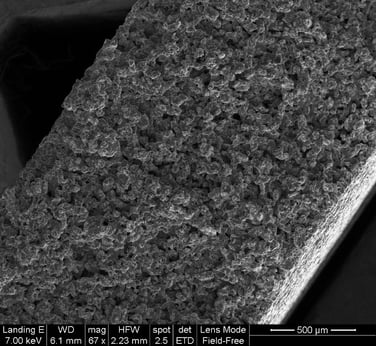
Figure 3: Electron micrograph of the sintered frit after it had been coated and broken in half to expose the internals of the part for analysis.
The common concern for most customers is whether the entirety of the part receives the coating, as any uncoated location would be a potential failure spot in their part. Figure 4 shows an EDS map of the iron, silicon, and oxygen signal in the same location as Figure 3. The silicon and oxygen are the two most abundant elements in the Dursan coating, and the iron signal is from the stainless steel substrate that is being coated. The maps show good penetration through the entirety of the frit. While there are areas in the silicon and oxygen map that are showing no signal, note that these black areas are also in the iron signal which means they are shadowing effects from the rough surface rather than holes in the coating.
Figure 4 and 5 are high magnification electron micrograph and EDS maps at the center of a Dursan coated frit. This higher magnification shows that the coating conforms to the internal network of the frit. In addition to the SEM/EDS work to show full coverage, a measurement was taken of the coating thickness, and the results were very similar to the SilcoNert 2000 coated frit (50-80 nm). It ranged from 60 nm in the very center of the frit to 80 nm toward the outer surface. This consistency is due to the surface area to volume ratio consistency within the internal working of the frit.
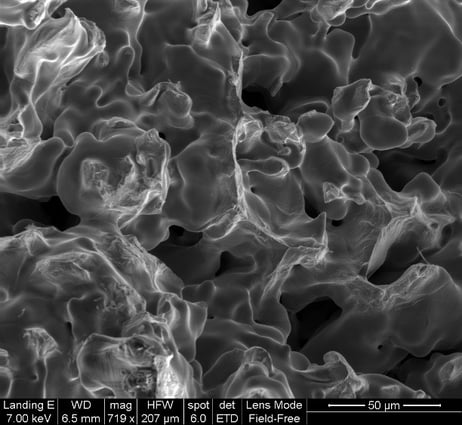
Figure 4: Electron micrograph of the internal network of a 2 µm sintered frit at higher magnification.

Figure 5: EDS maps of silicon at a higher magnification within the sintered frit.
Conclusion:
SilcoTek can conformally coat the internals of fritted materials utilizing our patented CVD coating technology. SilcoNert and Dursan coatings are superior to line of sight coatings such as PVD which would not be able to penetrate into the tortuous network that a typical sintered frit might have.
The two most common coatings used for fritted materials at SilcoTek are SilcoNert 2000 and Dursan. In this study both coatings were applied to 2 µm stainless steel frits. The coatings were found to conformally coat the entirety of the frit. They were also able to penetrate the frit to offer a thick enough coating to act as a good barrier between the environment and the steel while at the same time being thin enough to not block any pores or cause back pressure issues. The coating process resulted in a consistent coating through the entire frit within ~30 nm of thickness variation. Customers that are experiencing activity or corrosion issues between their system and a bare metal frit should consider SilcoTek’s coatings to provide the protection necessary for optimal performance.
OK the coatings can be applied to fritted filters, but do the coatings actually improve the corrosion resistance or inertness of the frit? Read our next blog to find out.
