Earlier this year, fabrication began off the coast of the North Sea on the Norwegain Continental Shelf for a new production and wellhead platform (PWP) called the Valhall PWP-Fenris Joint Development Project. The project consists of a new centrally located production wellhead platform. The platform will be linked to the Valhall field centre by a bridge with 24 well slots and an unstaffed installation with 8 slots at Fenris.
For this big project, SilcoTek was once again contacted by Wood, who is working in collaboration with Aker Solutions, for help. In 2023, we worked with Wood in collaboration with Equinor to provide coatings that allow for easy analyzing while onsite. SilcoTek coatings have been used to prevent reactions and adsorption of mercury compounds for a variety of customers in many applications. The chart below (Figure 1) shows an example of how untreated stainless steel can interfere with active compounds in a mercury storage cylinder, creating poor analytical results while the SilcoTek coated version is impervious to adsorption and shows accurate readings. We were proud to assist Equinor in the mercury removal unit of their methanol plant and look forward to serving the energy production community in the future. To read the full case study on Wood, click HERE .
Figure 1. Mercury adsorbs into stainless steel creating poor reading results while SilcoNert-coated stainless steel maintains an accurate and steady level of mercury compounds over 50 days.
So, how can SilcoTek help with this new project?
SilcoTek coatings can provide significant benefits in offshore drilling projects like the Valhall PWP-Fenris Joint Development Project. Given the harsh and corrosive conditions typically found in offshore environments, the use of SilcoTek’s chemical vapor deposition (CVD) coatings can enhance the durability, reliability, and efficiency of drilling operations. Here are some examples of how SilcoTek coatings could be applied in this application:
Preventing Adsorption in Sampling Systems
Accurate chemical analysis is crucial in offshore drilling to monitor the composition of hydrocarbons and other fluids extracted from wells. SilcoNert® 2000 coating can be applied to sampling lines, probes, and containers to prevent the adsorption of reactive compounds like sulfur and mercury. This ensures that the samples taken from the wellhead or other parts of the platform are accurate, leading to better decision-making and optimization of the drilling process. See the below Figure 2 showing how SilcoNert coated tubing retained the Methyl Mercaptan sample.
Figure 2: Tubing coated by SilcoNert 2000 provides nearly instant sample response, requiring no “priming” of the analytical system.
Increased Component Lifespan
Offshore platforms like the Valhall PWP-Fenris often operate in remote locations where replacing damaged or corroded components can be costly and time-consuming. By using SilcoTek’s coatings, the lifespan of critical components is extended, reducing the frequency of maintenance shutdowns and the need for costly replacements. This contributes to the overall operational efficiency and cost-effectiveness of the drilling operation.
Corrosion Resistance
Offshore drilling platforms are exposed to extreme environmental conditions, including saltwater, high humidity, and various chemicals that can lead to rapid corrosion of metal components. Silcolloy® 2000, one of SilcoTek’s coatings, significantly improves the corrosion resistance of stainless steel and other metals. By applying our coating to key components such as pipelines, valves, and fittings on the platform, the longevity of these materials is increased, reducing the need for frequent maintenance and replacements. Another great case study that SilcoTek partnered with Turner Designs on involved corrosion problems in measuring hydrocarbons in seawater. Below, Figure 3 shows SilcoTek’s high durability and corrosion resistant coatings, Silcolloy and Dursan, significantly improve salt and sea water corrosion resistance and durability while significantly reducing cost. Dursan resists corrosive attack from sea water and most chlorides. Concentrated hydrochloric acid immersion shows Dursan and Silcolloy compare favorably to super alloys while significantly reducing life cycle cost.
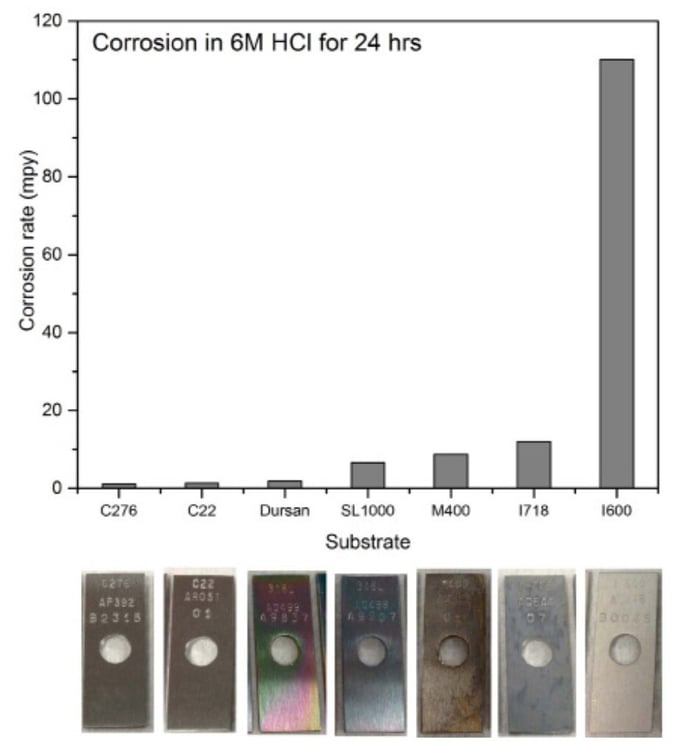
Figure 3: SilcoTek coated 316 Stainless Steel outperforms alloys like Inconel and Monel.
Safety and Environmental Protection
Coated components are less likely to suffer from leaks or failures due to corrosion or chemical reactions. This enhances the safety of the drilling operation, as well as the integrity of the platform, reducing the risk of environmental spills and contamination. In addition, SilcoTek’s inert coatings help to ensure that the drilling process does not introduce additional contaminants into the marine environment.
Cost Efficiency
While the initial investment in SilcoTek coatings may be higher than standard untreated materials, the long-term savings in maintenance, repairs, and downtime can be substantial. This makes SilcoTek coatings a cost-effective solution for the complex and challenging environment of offshore drilling. Figure 3 is a cost comparison of Silcolloy vs. high-performance materials and uncoated stainless steel. As you can see, Silcolloy coating is more than 2x more cost effective than stainless steel and about 4x more cost effective than the expensive high performance alloys, providing our customers with the best option when cost is a concern.
Figure 3: Life cycle cost comparison of Silcolloy® vs. high performance alloys show significant cost savings over the life of the project.
Enhancing Flow Assurance
In offshore drilling, maintaining uninterrupted flow in pipelines and equipment is critical. SilcoTek coatings can reduce the adhesion of contaminants, such as waxes, hydrates, and scale, that can form inside pipelines and equipment. This leads to smoother flow and reduces the risk of blockages that could halt production. Applying SilcoTek coatings to flowlines and critical equipment helps in maintaining optimal production rates.
Application Areas:
- Wellhead Equipment: Protecting wellhead components from corrosion and chemical attack.
- Flowlines and Pipelines: Enhancing the internal surfaces to prevent deposition and corrosion.
- Sampling Systems: Ensuring accurate sampling by preventing adsorption of active compounds.
- Valves and Fittings: Extending the lifespan of critical flow control equipment.
- Heat Exchangers and Pumps: Improving the performance and durability of key process equipment.
In summary, SilcoTek coatings can play a vital role in enhancing the performance, safety, and cost-effectiveness of offshore drilling operations, such as those in the Valhall PWP-Fenris Joint Development Project. By protecting against corrosion, improving sampling accuracy, and reducing maintenance needs, these coatings contribute to the overall success and efficiency of offshore projects.
For more information on how SilcoTek coatings can help in your application, contact our experts!
References:
Fabrication begins on major projects Yggdrasil and Valhall PWP Fenris. Aker Solutions. (2023a, September 4). https://www.akersolutions.com/news/news-archive/2023/fabrication-begins-on-major-projects-yggdrasil-and-valhall-pwp-fenris/
Follow Us on Social Media!