SilcoTek® recommends customers who use coated stainless-steel parts in high temperature applications (over 450°C) to preheat the parts prior to sending them in for coating. This recommendation was based primarily on the knowledge of metal sensitization, but we had not investigated how much of a benefit to expect. This blog post provides experimental data to show when and how preheating before coating may benefit high temperature applications.
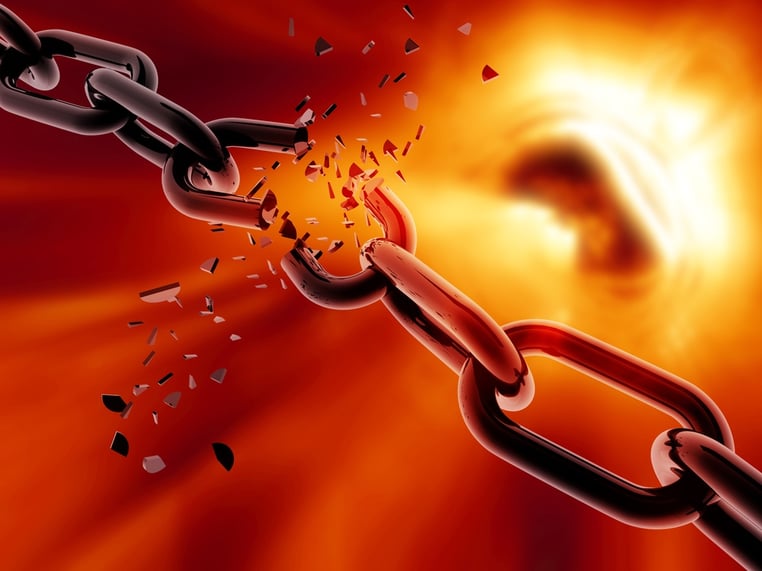
What are the advantages of preheating your parts before coating?
Many customers use SilcoTek’s coatings in high temperature applications (over 450°C). SilcoTek recommends for these customers to preheat their parts in an inert atmosphere to achieve optimum coating performance under high temperatures. Previously, we assumed the need for preheating based on the knowledge of metal sensitization, but that was based more on literature than experience. Since preheating does add an additional step for our customers and some may have to outsource this step, SilcoTek launched a study in 2022 to gather data so that we can better define the performance difference between preheated and non-preheated parts. This additional data should help you determine whether you would like to add a preheating step before sending your parts to SilcoTek for coating. The preheating service for this study was performed by a third party, Solar Atmospheres, as SilcoTek does not currently have the necessary equipment to carry out this treatment. Solar Atmospheres is a recommended resource for customers who do not have onsite preheating capability, and SilcoTek would be happy to supply the preheating parameters used in this study.
Data and Discussion
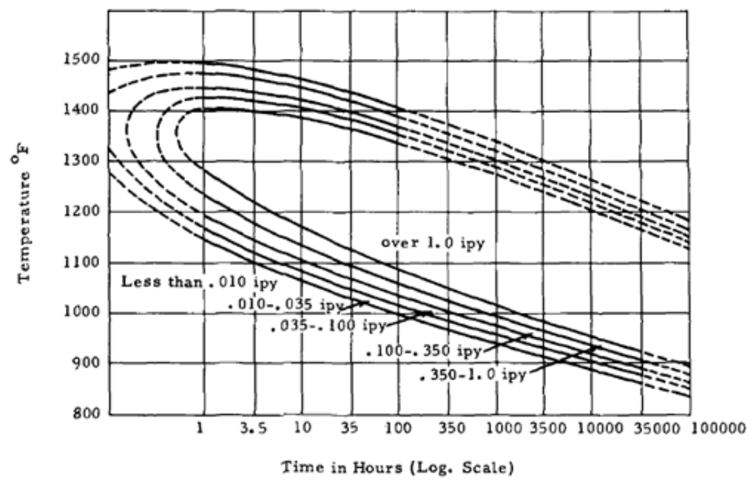
Figure 1: Time-temperature sensitization diagram of 316L stainless steel, as determined by the boiling nitric acid test.1
Clean, uncoated 316L stainless-steel coupons were sent to Solar Atmospheres to receive the preheat treatment. The time-temperature sensitization shown in diagram 1 in Figure 1 was used as a reference to choose preheat parameters, so that they would incur some sensitization in the metal. After samples were received back from Solar, they followed SOP protocols at SilcoTek for surface preparation and coating. A parallel group of coupons that did not see the preheat step were processed side-by-side as a control group.
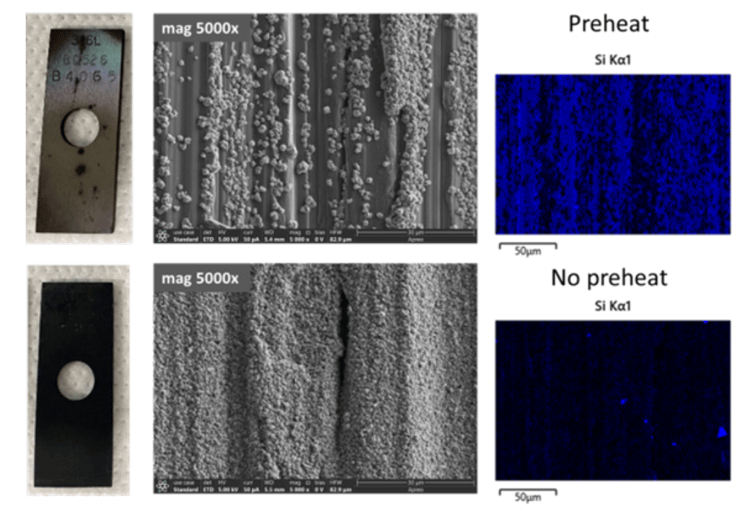
Figure 2: Silcolloy 1000 coupons after exposure to 800°C for six hours in air, with the preheated coupon (top) showing better thermal stability than the control coupon (bottom). SEM images (middle) were taken at 5000x magnification, and the silicon EDS maps (right) were taken at 2000x magnification.
Figure 2 shows two Silcolloy® 1000 coupons after exposure to 800°C in air for six hours, one received the preheat treatment at Solar prior to coating (top row) and the other one did not (bottom row). Note that Silcolloy 1000 is not our recommended solution for high temperature thermal stability; it was investigated in this experiment merely to examine the impact of preheat treatment. Even though neither coupon looked great after being exposed to 800°C, the improvements shown by preheat are still noteworthy. Whereas the control coupon was completely covered by metal elements diffused from the stainless-steel substrate (indicated by the grainy particulates in the SEM image) and showed very little coating presence on the surface (indicated by the lack of blue in the silicon EDS map), the preheated coupon showed significantly more coating presence with far less metal diffusion (indicated by less particulates in the SEM image and more blue (silicon) presence in the EDS map.
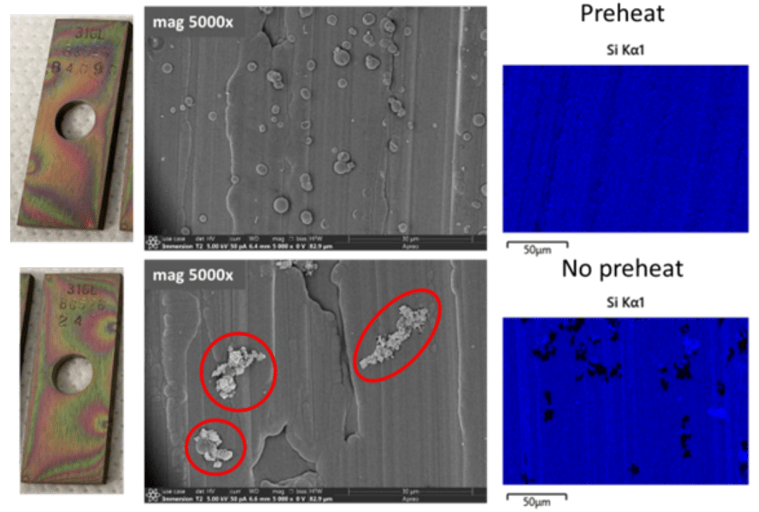
Figure 3: Silcolloy 2000 experimental coupons after exposure to 800°C for six hours in air, with the preheated coupon (top) showing better thermal stability than the control coupon (bottom). SEM images (middle) were taken at 5000x magnification, and the silicon EDS maps (right) were taken at 2000x magnification.
In a series of blog posts (can be viewed here in part 1, part 2 and part 3), we discussed how SilcoTek improved thermal stability of the Silcolloy 1000 coating (referred to as “SOP” in the blog posts) with an experimental coating referred to as “RD15” in the blog posts. None of the samples in that earlier study received any preheat treatment, and even the experimental coating started to show some void spots in the film after 800°C exposures, where silicon was replaced by metal elements from the stainless-steel substrate. In this study the preheat treatment was applied to the experimental coating, now known as Silcolloy 2000 experimental (replacement for Silcolloy 1000 for high temperature applications), and Figure 3 highlights the difference made by this treatment. Although the benefits are difficult to discern visually, the coupon that was preheated at Solar (top row) demonstrated better film integrity after the 800°C exposure, evidenced by no sign of metal in the SEM image (the particulates in the top SEM image were silicon particles generated during the film deposition) and complete silicon coverage in the EDS map. In comparison, the control coupon (bottom row) did show metal clusters (circled in red in the SEM image) breaking through the coating and bare spots in the silicon coating as highlighted by the dark regions in the EDS map. Note that the SEM images and the EDS maps were taken at different magnifications (SEM taken at 5000x and EDS taken at 2000x), to enable more surface details in the SEM image but capture a larger area in the EDS map for film coverage information. Therefore, the bare spots in the EDS map and the SEM image do not have a 1:1 corresponding relationship.
Coming Soon: Silcolloy® 2000 for High Temperature Applications
SilcoTek is launching a brand new game-changing coating very soon: Silcolloy 2000! There are many new and exciting benefits to this new performance coating, like improved thermal stability above 600°C (depending on substrate, as evidenced in this blog post), excellent anti-fouling and anti-coking properties, high-purity amorphous silicon surface, and enhanced corrosion resistance compared to untreated stainless steel and performance alloys, just to name a few. Silcolloy 2000 provides new advantages to applications such as fuel combustion systems, aerospace componentry, industrial instrumentation and flow control products, heat exchanger tubes, chemical storage vessels, and more. Contact us to ask us how we can help solve your most troublesome high temperature problems.
Conclusion
This blog post presented experimental data to show that a properly designed preheat treatment helps to boost the thermal stability of silicon coating under high temperature exposures. The experiment was conducted on 316L stainless steel, and the benefit was observed and reproduced with several different coatings (two discussed in this post and more tested internally but not published). A preheat treatment is recommended to harvest the full potential of SilcoTek’s silicon coating for high temperature services, especially if the coated parts are expected to see temperatures above 700°C. It should be pointed out that the preheat benefit is not shared across the board for all metal alloys. Inconel 625, for example, another alloy examined during this experiment, did not benefit from the preheat treatment. SilcoTek encourages our customers to reach out and discuss their high temperature application needs and metal of choice, so we can work together to find a best solution for their application challenge.
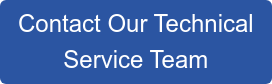
References:
1. Ebling, H. F. and Scheil, M. A. “Time-temperature-sensitization (TTS) diagrams for types 347, 304L and 316L stainless steels”, ASTM International, 1965