How do you know if your coating is still performing as it should? We get this question quite often and the answer is... not that simple. Each situation is different, which makes it difficult to pinpoint when your parts need to be re-coated. Let's explore why this isn't a one-size-fits-all type of question and answer.
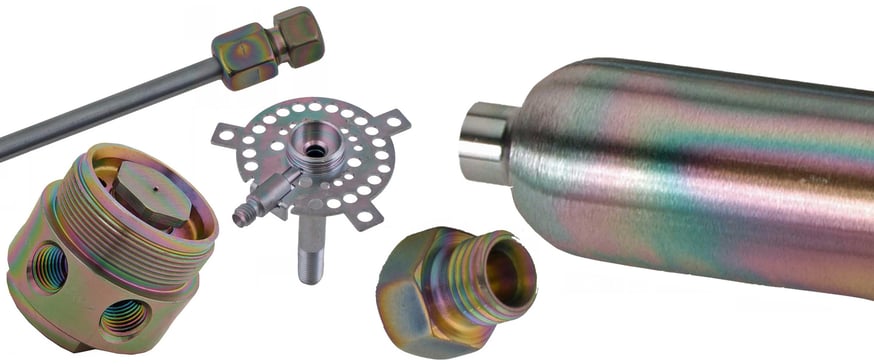
What are CVD coatings and how are they different than other coatings?
SilcoTek's chemical vapor deposition (CVD) coating process produces a very thin layer on your part's entire surface, including complex geometries and hard to reach areas. It is a gas phase coating process that introduces vapor (gas) into a high heat environment to allow the gases to adsorb onto the surface of your substrate. SilcoTek's patented CVD coating process is great for stainless steel, high nickel alloys, ceramics, and glass. Since coated parts will see high temperatures (up to 450 degree Celsius), we would not recommend coating on some substrates like carbon/tool steels or other materials that cannot withstand high temperatures. The non-line-of-sight application process allows us to keep the coatings as thin as possible while still delivering excellent barrier properties, as opposed to traditional spray, dip, or paint on protectants that are much thicker. By applying our super thin coatings, manufacturers are not forced to alter tolerances or other mechanical design features to accommodate thicker coatings.
SilcoTek is a company that is dedicated to the development and application of CVD coating services for customers in high-technology industries like semiconductor, analytical chemistry, life sciences, and energy. We often get questions about whether a customer's coating is still intact and performing to its fullest. This depends on several factors which almost always vary from one user to the next. For example, even a 5 degree temperature change can have a significant impact on the performance of any coating in certain environments. Let's discuss the major factors associated with coating lifetime and performance.
Environment
It only takes a bit of elbow grease and a scotch-brite pad to remove the coating from parts that you don't want coated. If your coated parts saw any sort of abrasive process or came into contact with anything during use, it is possible that the coating could wear. We understand that sometimes it can be difficult to tell if the coating has worn off. If you're unsure about your coating's performance or thickness, please contact us to talk about how we can help. We are able to evaluate your parts to determine the thickness of the coating, if needed. Check out our coating care resources to make sure you're keeping your parts in tip-top shape.

Temperature
Our coatings are less than 2 microns thick. Even coatings with low thermal conductivity will not offer significant thermal protection if they’re extremely thin. The other issue regarding thermal performance is that our coatings are designed for specific performance/benefits to the user. Some coatings are hydrophobic, some are inert or non-reactive, others are corrosion resistant, etc. Because the coatings are designed for specific performance parameters, the coating formulation or additives will vary. The variation in formulations can limit the thermal performance of our coatings. The recommended maximum temperature for each of our coatings is:
SilcoNert 2000 |
450 ° C, 400 ° C (oxidative atmosphere) |
SilcoNert 1000 |
720 ° C |
Silcolloy |
720 ° C |
SilcoGuard |
720 ° C |
SilcoKlean |
450 ° C(functionalization loss), 400 ° C (oxidative atmosphere), 1410 ° C (melting) |
Dursan |
500 ° C, 450 ° C (oxidative atmosphere) |
Dursox |
500 ° C |
Notak |
300 ° C |
Chemical Exposure
Chemical compatibility is important when assessing whether our coatings will hold up to your application. SilcoTek's researchers have If you're not sure if the coating will withstand your application's chemical exposure, please check our chemical compatibility chart. Silco- coatings are stable in pH 0-8 and Dursan coatings can withstand pH 0-14.
Here's an example showing HCl exposure at different temperatures.
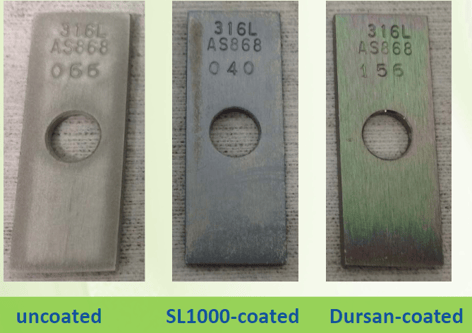
Above is corrosion data showing 6M HCl at 50° C for a 7-hour immersion. As evidenced by the graph, the coating greatly delayed and reduced corrosion of the 316L stainless steel coupons. Both Dursan and Silcolloy 1000 out-performed the uncoated coupons.
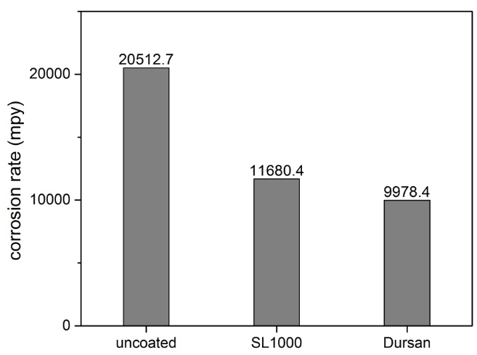
Above we have the same solution at 80° C. As you can see, the corrosion rate at the elevated temperature was significantly higher.
This is just one example showing how chemical exposure doesn't necessarily mean your coating will or won't perform as intended. There are several factors that should be accounted for when determining if your coating is still intact.
Wear
As with anything, use will cause wear over time. If you're noticing that there are spots that are worn more than others, it is a good indication that your coating may not perform as well. Some of our coatings can be removed with a little abrasion, so any contact points may wear more quickly.
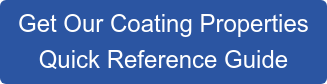
Colorful Appearance
If your coated parts aren't quite as shiny and rainbow-like as they used to be, that doesn't necessarily mean that your coating isn't useable anymore, but it could be an indication that the coating is wearing off. With the exception of our Notak coating, our coatings have a rainbow-like hue when applied. Depending on which coating your parts received, it might be a good idea to inspect your parts for any bare metals or evidence of wear.
If your application goes beyond these recommendations, there are ways to mitigate adverse effects. Thermal pretreatment of the part will reduce the potential of coating failure when exposed to elevated temperatures.
What can you do if your coating needs to be re-applied?
If your coating has degraded or you simply want to re-coat your parts to ensure maximum performance, please contact us. You can learn more about our re-coating process in this previous blog post that explains removing and re-applying coating.
Have questions about your parts' performance?
Contact us to discuss with one of our coating experts!
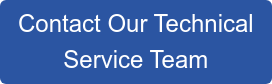