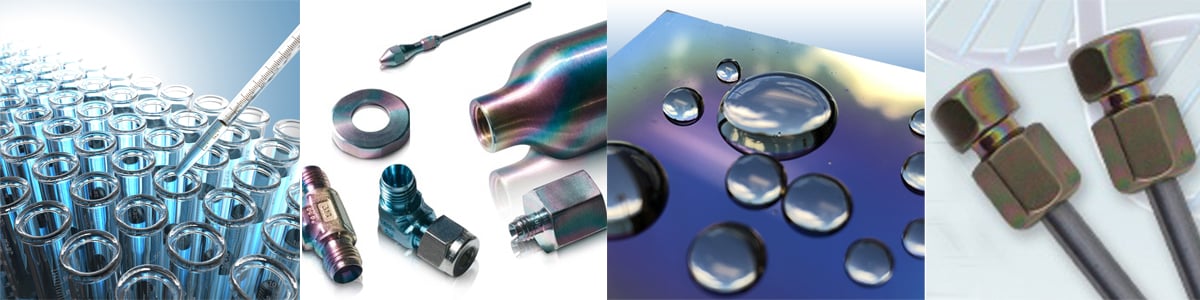
We discuss how to improve corrosion resistance in biopharmaceutical testing and learn how to improve test reliability and decrease costs.
Improving Corrosion Resistance in Biopharmaceuticals
Key words: Biopharmaceuticals, biologic, biosimilar, guanidine hydrochloride, corrosion, proteins
Corrosion in Biopharma Introduction:
Guanidine hydrochloride is a commonly used cleaning agent in the biopharmaceutical industry. It can cause corrosion issues in tubing, valving, and pumps constructed of 316 stainless steel (which is also common in that industry). A study based on 1-week and 1-month exposures show that utilizing SilcoTek’s Dursan coating process can mitigate corrosion and leading to an increase in yields and a decrease in costs.

Many biopharmaceutical producers utilize guanidine hydrochloride as a cleaning agent for their systems. The only issue with its use is that it chemically attacks the stainless steel tubing, fittings, valves and many other locations in the processing plants. Experts in the industry argue the corrosive nature of guanidine hydrochloride. Some claim the corrosion happens rapidly, others suggest with proper passivation of steel, the corrosion can be very slow. All seem to agree that over time, oxidation of the stainless steel will lead to rust. The biopharmaceutical industry refers to this as “rouging”.
In this blog post you will learn:
How Dursan coating improve corrosion resistance in biopharmaceutical applications
How basic test protocols can be used to determine the corrosion resistance of surfaces.
How CVD coatings can reduce maintenance and save money in corrosion applications.
|
Corrosive Attack in Analytical and Chemical Processes
Guanidine hydrochloride (sometimes referred to as guanidinium chloride) is a powerful protein denaturing agent. It works by disrupting the hydrogen bonding network in water which, in turn, will change the stability of the native state of other molecules that are in the water. In the biopharmaceutical world, it is often used as a cleaning agent in high concentrations. Concentrations of 6M or higher will cause most proteins to lose their ordered structure and turn into randomly coiled molecules. Unfortunately guanidine hydrochloride also corrodes stainless steel flow paths which can lead to pitting and promote areas susceptible to carryover and cross contamination in analytical and chemical process applications.
This blog post will show that when exposed to 6M guanidine hydrochloride, 316L stainless steel will show rouging while Dursan coated coupons are unaffected. You can test the performance of Dursan yourself by ordering free Dursan coated test coupons.
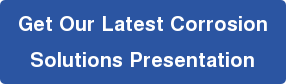
Experiment, Data and Discussion: Identifying and Preventing Metal Ion Leaching
Dursan coated and bare coupons were immersed in 6M guanidine hydrochloride purchased from BioVision Incorporated. The coupons were evaluated at 1-week and 1-month intervals. Evaluations included removing the coupons from the solution, rinsing with DI water, sonicating in DI water for 15 minutes, followed by drying in a 230°F oven for an hour.
Corrosion can be quantitatively calculated by the change in mass before and after exposure to the corrosive media. In this study it was found that there was no mass change both after 1 week and 1 month of exposure for coated and uncoated coupons. This shows that guanidine hydrochloride is not nearly as corrosive as other media that SilcoTek Corporation has tested such as hydrochloric acid, sulfuric acid, or bleach which is another cleaning agent used in the biopharmaceutical industry. ASTM G31 immersion testing (below) shows that Dursan significantly reduces corrosion in common applications found in analytical testing.
Read more about how SilcoTek coatings can improve corrosion resistance in analytical flow paths.
/Bleach%20ss%20vs%20dursan.jpg?width=463&name=Bleach%20ss%20vs%20dursan.jpg)
Visually, there was a difference between the coated and the uncoated coupons at the 1-week mark of the experiment as shown in Figure 1. The uncoated coupon on the left shows that there are pockets across the surface that are starting to show oxidation, rust, or rouging. The coupon on the right shows that a Dursan coated piece of steel does not experience the same effect.
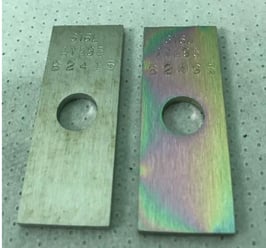
Figure 1: A bare stainless steel coupon (left) and a Dursan coated stainless steel coupon (right) were exposed to guanidine hydrochloride for one week. The bare steel shows minor rusting across all faces of the coupon where the Dursan coated coupon appears to be unaffected.
Since there was no loss of mass for the coupons after the 1-week trial (scale accuracy is 0.1 mg), they were returned to the 6M guanidine hydrochloride solution to soak for 3.5 more weeks (1 month total exposure). Again, there was no change in the mass of the coupons, but the minor rusting effects were much more dramatic as seen in Figure 2.
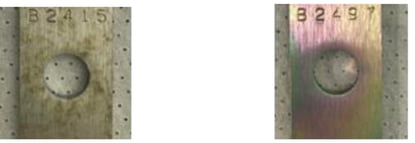
Figure 2: A bare stainless steel coupon (left) and a Dursan coated stainless steel coupon (right) were exposed to guanidine hydrochloride for one month. The rusting on the bare coupon is more severe than the 1-week exposure. As seen previously, the Dursan coated coupon is unaffected by the exposure.
In addition to the increased rouging, there was also a discoloration in the guanidine hydrochloride solution with the uncoated coupon immersed in it for one month. This color change, seen in Figure 3, was not seen at the one-week point of the experiment. The yellow tint to the liquid indicates that iron has leached out of the coupon and into the solution. This is a potential issue for many biopharmaceutical companies, as iron ions can interact with their various drugs and cause impurities and/or low yields.
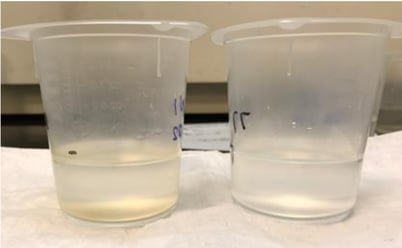
Figure 3: Guanidine hydrochloride solutions after a bare (left) and a Dursan coated (right) coupons were immersed for one month. The yellow tint in the solution that contained the bare coupon is a sign of corrosion, whereas the solution that contained the Dursan coated coupon showed no color change over the immersion period.
Conclusion:
Guanidine hydrochloride is a commonly used cleaning agent in the biopharmaceutical industry. It can cause corrosion issues in tubing, valving, and pumps constructed of 316 stainless steel (which is also common in that industry). Utilizing SilcoTek’s Dursan coating process, these issues can be mitigated leading to an increase in yields and a decrease in costs.
Have a question about how SilcoTek coatings can improve the corrosion resistance of your products? Follow us on LinkedIn or contact our Technical Service Team.
