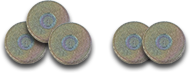
Sintered metal materials are often used as filtration media due to their controllably porous nature; however, they do not necessarily exhibit the same chemical and physical features as their wrought or cast counter parts. In this blog post we discuss the corrosion behavior of 316 stainless steel and Hastelloy sintered metal frits and how to improve corrosion resistance.
Improving the Corrosion Resistance of Sintered Materials
Powder metallurgy offers a variety of advantages over traditional wrought or cast materials. One such advantage, often used in filtration, is the ability to produce materials of controlled and uniform porosity. Corrosion and mechanical properties of sintered materials are typically worse than their wrought counterparts. In the case of stainless steels, corrosion rates can be two or more orders of magnitude worse for sintered materials.1-4 In this blog we discuss how to improve the corrosion resistance of sintered materials like fritted filters.
Have a question about this blog or material properties? Click the box below to discuss your application with one of our coating scientists.
Have a Question? Contact Our Technical Service Team
In this blog post you will learn:
- Compare the corrosion resistance of various sintered materials
- Learn how silicon coatings can penetrate sintered materials and coat fine internal surfaces with a corrosion resistant silicon barrier.
- How to improve the corrosion resistance of sintered metal filters and other products.
- How the corrosion resistance of various silicon coatings compare to stainless steel and super alloy metals.
|
Background:
Hastelloy is a specialty alloy developed by Haynes International that exhibits excellent corrosion resistance in a variety of severe environments. Its superior resistance to halides makes it an attractive material to use in the semiconductor industry where corrosive gases can attack materials such as stainless steel. As of the date of writing this, there are no reports in literature on the corrosion difference between sintered and wrought Hastelloy materials. This blog will evaluate both stainless steel and Hastelloy fritted materials, purchased from two separate companies, for their corrosion resistance to hydrochloric acid.

It was found that the sintered metal discs lost a significantly higher amount of weight than traditional wrought materials such as our typical corrosion coupons. Calculating corrosion rates also considers surface area, which is much higher for porous sintered materials. This causes the corrosion rate calculation to be much smaller than that of wrought materials, indicated that direct comparisons of corrosion rates using the same calculation (ASTM G31) may not necessarily be an apt comparison.
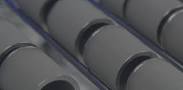
Sintered metal discs made of stainless steel and Hastelloy were purchased from two companies. To keep the experiment as consistent as possible, the discs were all ordered as 10 microns in nominal pore size and roughly the same diameter and thickness of 1.5 inches and 1/16 inches respectively. To calculate the corrosion rate of a material, the surface area that is exposed to the corrosive media must be known. Each disc type was tested at the Materials Characterization Laboratory at Penn State with the ASAP 2020 Automated Surface Area and Porosimetry System. The results of the measurements can be found in Table 1. Ideally, since these frits are all the same nominal pore size, they would have similar surface areas. The difference between Company A and Company B (roughly x2) shows the variability in processing and porosity of sintered materials.
|
316 SS Company A
|
316 SS Company B
|
Hastelloy Company A
|
Hastelloy Company B
|
BET Surface area
|
0.0514 m2/g
|
0.0976 m2/g
|
0.0327 m2/g
|
0.0505 m2/g
|
From previous experiments (both internally and externally), we know that our CVD coating will fully penetrate and coat 0.5 µm nominal pore size frit of similar thickness. The image below shows a sectioned coated frit. Coating penetration into the frit can be seen by the unique silicon coloring throughout the frit.
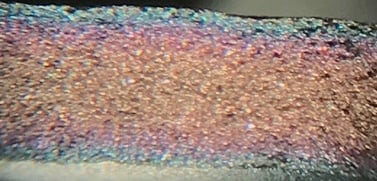
The coating has little to no effect on the pore size as measured via bubble point testing. Due to the results from these prior experiments, we can safely assume that the porosity of the sintered material does not significantly change after coating. Each sintered disc type was coated with Dursan, Silcolloy, and Silicon Nitride to test the impact the coatings had on corrosion in 6M HCl. The immersion testing followed ASTM G31 guidelines and had an exposure time of 1 week at room temperature.
316 stainless steel:
Weight loss for the stainless steel sintered discs are shown in Figure 1. Percent of weight loss can potentially tell more about the extent of corrosion rather than the raw weight loss data, so that is also included in Figure 2.
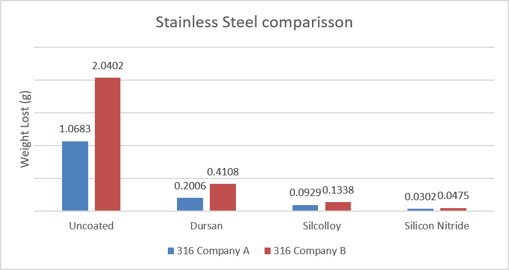
Figure 1: Absolute weight loss of sintered discs after 1-week immersion in 6M HCl.
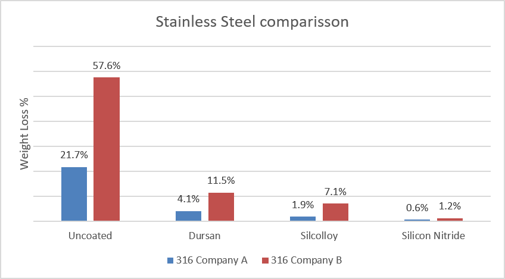
Figure 2: Weight loss percent of sintered discs made of stainless steel.
As mentioned earlier, there is a way to calculate corrosion rate based on the surface area that is exposed to the corrosive media. The equation for this calculation is:
Corrosion rate=(K∗W)/(A∗D∗T)
Where K is a constant, W is weight loss in grams, A is the exposed surface area in cm2, D is the density of the alloy in g/cm2, and T is the time exposed to the corrosive media in hours. Figure 3 shows the corrosion rate of the stainless steel sintered discs.
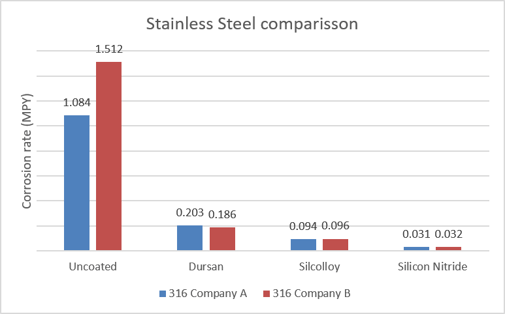
Figure 3: Corrosion rate of stainless steel sintered discs.
SilcoTek has previously showed that not all stainless steel is created equally. A study involving bleach corrosion, shown here on slide 39, found that two different heats of stainless steel had dramatically different corrosion rates. The two lots can be leveled onto the same “playing field” by coating them with Dursan. In this study, we found that Dursan, Silcolloy, and Silicon Nitride all had the same effect on these sintered discs where the corrosion rates, despite manufacturer, became similar after coating, whereas Manufacturer A’s bare disc was clearly superior to Manufacturer B’s bare disc. Read how SilcoTek coatings reduced the variation in corrosion rate of stainless steel.
Hastelloy:
Hastelloy is a superalloy developed by Haynes International specifically for corrosion resistance. The sintered discs that were purchased are made of C-22 from Company A and C-276 from Company B. Unfortunately, identical alloys were not available from the two companies. C-22 has a slightly higher Chromium content and lower nickel and molybdenum content, and is usually considered an upgrade to in overall performance. This was apparent when examining the mass loss from the sintered discs as shown in Figure 4 and Figure 5 which are the absolute mass loss and percent mass loss respectively.
It should be noted that the balance used to measure the mass of the discs before and after exposure to the hydrochloric acid can only measure to mg levels. The values measured for C-22 coated by Silcolloy and Silicon Nitride are essentially zero as they’re within the error of the measurement. Additionally, the hydrochloric acid turns from a clear liquid to yellow when corrosion starts as can be seen in this coupon immersion example below. The center coupon shows the initial onset of corrosion and ion contamination.
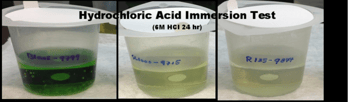
This yellow color is due to iron ions leaving the metal and dissolving in the liquid. Eventually nickel also starts to dissolve and it turns the liquid green (above left). The Silcolloy and Silicon Nitride coated C-22 discs showed no yellow tint to the liquid, indicating no corrosion occurred.
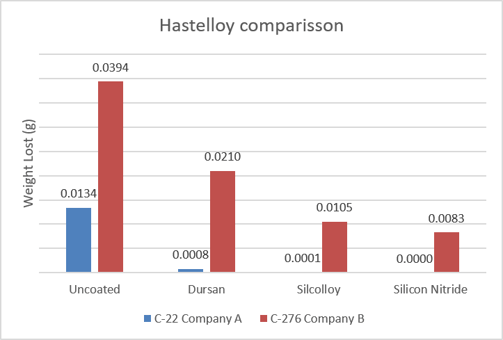
Figure 4: Absolute weight loss of Hastelloy sintered discs after 1-week immersion in 6M HCl.

Figure 5: Weight loss percent of sintered discs made of hastelloy.
As expected, C-22 lost less weight than C-276 and the Hastelloy sintered discs outperformed 316 stainless steel products. Corrosion rates were calculated for the Hastelloy discs as well for a true comparison. These values can be seen in Figure 6. It was interesting to see the corrosion rate for uncoated C-276 was slightly superior to C-22, but the coated C-22 material were clearly superior including zero corrosion on SIlicolloy and Silicon Nitride coated discs.
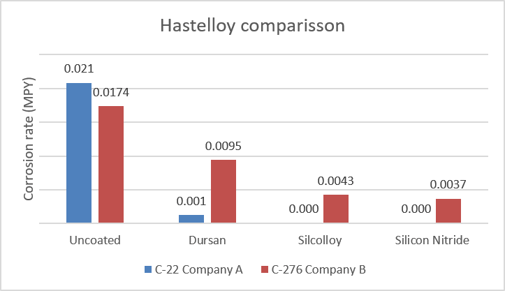
Figure 6: Corrosion rate of stainless steel sintered discs.
Previous studies on wrought 316 stainless steel and C-22 Hastelloy shows that Hastelloy had about 160 times lower corrosion rate compared to 316 stainless steel. Here, we see it is closer to about 60 times lower. This could be due to the sintering process for 316 stainless steel being a very mature technology, whereas companies continue efforts to optimize Hastelloy sintering, but that is speculative.
Figure 7 shows uncoated stainless steel, coated stainless steel, and uncoated Hastelloy as a point of comparison. While Hastelloy offers benefits over stainless steel, there are often long lead times and higher expenses involved with Hastelloy materials. Some may choose to utilize coated stainless steel to achieve similar performance. Here, coated sintered porous materials can come close to the corrosion performance of uncoated Hastelloys by utilizing our coatings including our newest corrosion coating: silicon nitride.
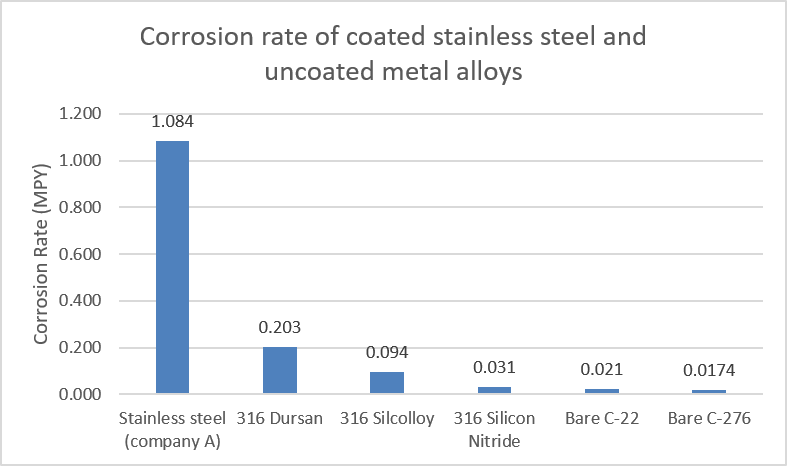
Figure 7: Stainless steel (coated and uncoated) compared to Hastelloy sintered materials.
Conclusion:
Sintered materials are often used as filtration media for numerous industries including the petrochemical, analytical, medical, marine, and semiconductor industries. This study shows that coating 316 stainless steel sintered material can provide protection against chloride corrosion and onto a similar playing field to Hastelloy material. The ultimate in corrosion protection involves utilizing C-22 Hastelloy combined with Silcolloy or Silicon Nitride. This combination showed zero corrosion when exposed to hydrochloric acid for a full week. This can provide the protection necessary for equipment that is in an aggressively corrosive environment and very sensitive to metal ion contamination such as the semiconductor industry.
Have a question about improving the corrosion resistance of your products? Contact our technical service team or ask the experts on LinkedIn.
References:
- E. Otero, A. Pardo, E. Saenz, M.V. Utrilla, P. Hierro, A study of the influence of nitric acid concentration on the corrosion resistance of sintered austenitic stainless steel, Corros. Sci. 38 (1996) 1485–1493.
- T. Raghu, S.N. Malholtra, P. Ramakrisnan, Corrosion behavior of sintered austenitic stainless steel filters in sulphuric acid solutions, Br. Corros. J. 33 (1988) 109–116.
- E. Angelini, P. Bianco, F. Rosalbino, M. Rosso, G. Scavino, Sintered austenitic stainless steels: corrosion behavior in sulphate and chloride media, Werst. Korr. 45 (1994) 392–401.
- E. Otero, A. Pardo, E. Saenz, M.V. Utrilla, F.J. Álvarez, Corrosion behavior of AISI 304L and 316L stainless steels prepared by powder metallurgy in the presence of sulphuric and phosphoric acid, Corros. Sci. 40 (1998) 1421-1434.