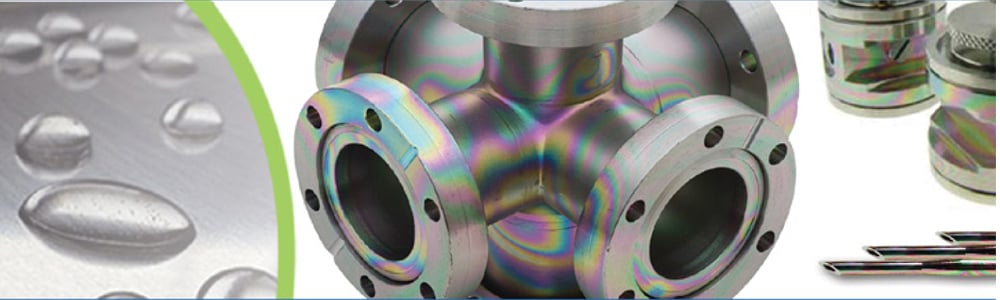
Coatings are used to improve corrosion resistance but for high purity DI water systems durability and contamination can be a concern. Learn how silicon coatings can help.
Improving the Corrosion Resistance of High Purity Water Systems
Applications for high purity water systems include metal filtration media, pumps, housings, piping, tubing, valves and fittings. Deionized (DI) and high purity water may not seem to be a major corrosion concern, especially in stainless steel systems, but corrosion can manifest itself in many ways. Including:
- Rouging
- Ion leaching and contamination of ion beds
- Pitting and damage to system flow paths
- Damage to heating elements
Typical corrosion solutions include polymeric coatings and use of more expensive metal alloys, but these options may not be compatible with high purity water system. These systems require a cost effective, high durability solution that will not contaminate the water.
In this blog post you will learn:
- How silicon coatings can improve corrosion resistance in stainless steel flow paths used in high purity water systems.
- How Dursan® and Silcolloy® can significantly reduce metal ion leaching in deionized (DI) water systems.
- How silicon coatings prevent rouging in water systems.
|
That's where silicon coatings like Dursan® make a difference. DI water, high purity water systems, filtration, and heat transfer systems benefit from Dursan coated surfaces in applications ranging from semiconductor fab systems, water, and wastewater management, analytical or process monitoring systems, midstream oil and gas processing, power generation, energy management, downstream refining and petrochemical, and gasification systems. Learn more about applications and use of coatings in filtration and heat transfer systems. Click the box below to read our e-book.

How Silicon Coating Protect Against Corrosion and Contamination
Silicon coatings like Dursan® and Silcolloy® act as an inert barrier that protect stainless steel flow path surfaces from reacting with the process fluid, be it corrosive process chemicals, high purity deionized water, wastewater, produced water or samples from chemical processes. The coatings are bonded to the stainless steel flow path by our patented chemical vapor deposition process. The silicon first diffuses into the metal surface and then layer by layer creates a corrosion resistant non-reactive barrier coating. The Auger plot below is a graphic representation of the coating layer. You can see how the silicon sputter depth remains consistent up to the well defined diffusion zone where the silicon bonds to metals from the stainless steel surface.
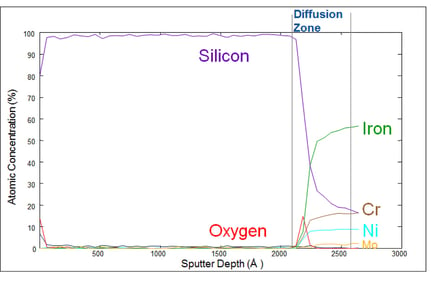
Our coatings protect metal filtration, heat exchanger systems, and sensitive high purity water processes from common process problems like corrosion, fouling, wetting, metal contamination, and surface oxidation. Processes that use our coatings benefit in many ways and without impacting thermal transfer properties of the base material.
- Improve yield by preventing process fluid contamination
- Reduce process and maintenance cost due to fewer repairs due to fouling or corrosion
- Optimize process flow by reducing fouling in filtration
- Reduce energy use due to fouling and corrosion in heat exchangers.
- Prevent rouging in water systems.

Corrosion Resistance Data
SilcoTek® corrosion resistant barrier coatings prevent flow path surface interaction with corrosives, extending component life while preventing product contamination. Our corrosion resistant coatings, Silcolloy® and Dursan®, are particularly useful for fighting corrosion in high purity or otherwise sensitive processes. In addition to extending the usable life of precision stainless steel parts, SilcoTek coatings prevent nano-scale corrosive reactions that can cause metal ion leaching and contamination, ultimately increasing process yield and reducing failure rates.
SilcoTek coatings perform in a variety of corrosive environments including acids, bleach, and other aggressive chemicals used in cleaning high purity systems. Let's review some examples of how our coatings improve corrosion resistance. The table below summarizes how Dursan can improve corrosion resistance over uncoated stainless steel.
Corrosive
|
Stainless Steel Corrosion Rate (mpy)
|
Dursan Coated Stainless Steel (mpy)
|
6M Hydrochloric Acid, 24 hr exposure
|
160
|
1
|
25% Sulfuric Acid, 24 hr exposure
|
55
|
5
|
52 Week Salt Spray
|
<0.01
|
<0.01
|
Bleach
|
1.7
|
0.1
|
Here's what exposure to concentrated hydrochloric acid does to stainless steel in 24 hours. Notice the test coupon is etched and the acid has turned green from the nickel leaching into the acid. The acid should be clear and free of contamination as shown in the Silcolloy® and Dursan® tests.
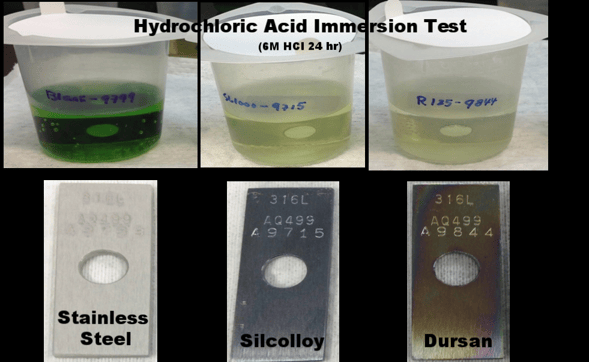
Learn more about how our coatings improve corrosion resistance, read corrosion presentation and get lots of informative data about how to improve the performance of your water filtration system.
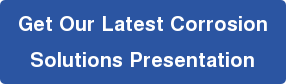
DI Water Leaching and Metal Ion Contamination
Corrosion manifests itself in many variants of material degradation. It can be aggressive and large enough to see visually such as the numerous examples in harsh acids or salt fog chamber experiments shown above, or corrosion can be at trace levels that are not detected visually or by weight loss but none-the-less can affect analytical test results or processes through metal ion leaching.
Previous blog posts have investigated metal ion leaching on common alloys used in water purification, analytical and other industrial process applications. So far, we have investigated water and methanol’s impact on stainless steel, titanium, and C-22 Hastelloy. Part one through three of this study can be found below:
In previous ion leaching studies, sintered discs made of the various alloys were exposed to pure methanol for one month. The resulting solution was then examined via inductively coupled plasma mass spectrometry (ICP-MS) for metal ion contamination. The results showed that all three coatings provided by SilcoTek® were able to stop metal ion contamination for 316 SS and C-22 alloys. Only Silcolloy® was able to provide protection for titanium ion leaching. The reasons for that were discussed in part 2 of this series.
Here we use the same experimental set-up to investigate DI water’s impact on these three alloys. Among numerous other uses, DI water is commonly used as a solvent for HPLC analysis, in food and drug production, and as a precursor in semiconductor applications. Here we show that titanium alloys do not suffer metal ion leaching in DI water, while both stainless steel and Hastelloy show large amounts of metal ion leaching, specifically an abnormally large amount of nickel leached into DI water when compared to the methanol leaching studies.
Data and Discussion:
Porous 316 Stainless Steel discs were purchased from Mott Corporation. All porous metal discs used in this study have a nominal pore size of 10 µm. Discs were coated with Dursan®, Silcolloy®, and a new test coating we're calling RD5. Each coated disc and a bare disc were placed in separate polypropylene containers with 50 mL of UHPLC grade DI water purchased from MilliporeSigma. Additionally, one polypropylene container was filled with 50 mL of water with no disc in it to act as a blank or control for the study. After one month of soak time, the porous disks were removed from the water and the samples were delivered to the Energy and Environmental Sustainability Laboratories at Penn State University. Samples were then prepared by addition of nitric acid to achieve the correct pH and were then analyzed using a Thermo Fisher iCap RQ ICP-MS.
Learn more about how our coatings can improve the performance of HPLC and other analytical systems. Click the image below to read our Applications Guide.
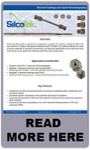
The 316 stainless steel disc results can be seen in Figure 1 below. The coatings on the sintered metal discs block the metal ions from leaching into solution. While there was substantial metal ion leaching into the solution, it was far less than experienced in the previous studies using methanol. Specifically, the iron and chromium levels were roughly an order of magnitude lower, as shown in Table 1.
The nickel concentration is relatively unaffected by the solvent choice. That's because the surface of 316 stainless steel has an oxide layer, largely consisting of chromium oxide, but also containing iron and nickel oxides. This layer provides a protective surface and is often self-healing when there is an oxygen source, such as air or water.
In this case, it can be concluded that the comparatively low levels of chromium leached into the water indicates less damage to the protective oxide layer when compared to pure methanol. With less damage to the oxide layer, there is less access to the iron to leach into solution.
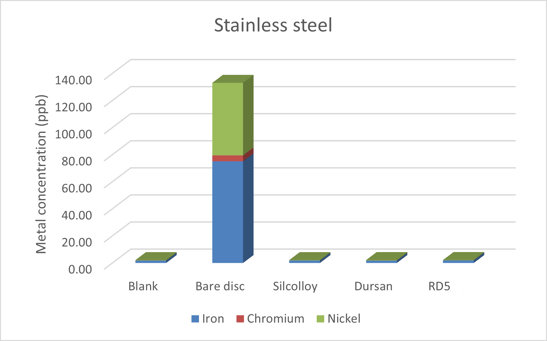
Figure 1: Stainless steel metal ion leaching into ultrapure deionized water.
|
Iron
|
Chromium
|
Nickel
|
Methanol extraction
|
812.81 ppb
|
33.55 ppb
|
61.48 ppb
|
DI Water extraction
|
75.13 ppb
|
4.34 ppb
|
53.62 ppb
|
Table 1: Metal ions extracted from an uncoated frit into solution after 30 days of soaking in methanol and DI water.
What remains unclear is to whether the nickel and iron metal contamination is a passivation effect or if it is truly corrosion of the material. The nickel and iron, along with their respective oxides, are much more easily extracted compared to the chromium oxide in the passive layer.3 It is possible that the contamination seen here is simply the removal of the nickel and iron from the passive layer, and no underlying metal was attacked, leaving a purer chromium oxide surface. Subsequent studies will be necessary to evaluate which mechanism is at play in this situation.
UHPLC grade DI water has shown it can cause corrosion events on 316 stainless steel. For 316 stainless steel, the corrosion seemed comparable to previous methanol studies; the three coatings provided protection to the sintered metal discs from any corrosion event.
I
Prevent Rouging in Water Systems
Rouging can be found in a variety of water systems or water containing systems including pure water, ultra-pure water, steam, treated potable water or untreated process water systems.
Preventing rouging and corrosion in high purity water, and process systems is preferred to costly component replacement or the associated maintenance and risk of product contamination. Options for preventing rouging range from:
- Selecting materials that are resistant to oxidation and chloride attack.
- Adjusting the pH of the water system to reduce the rouging potential.
- Adding a strong surfactant to the rinse solution to remove chlorides.
- Coating the stainless steel surface with a corrosion resistant and inert barrier coating like Dursan.
Of the prevention options listed, coating the surface with a high purity, non-line-of-sight, precision, corrosion resistant coating like Dursan®, is a simple and cost effective way to reduce or eliminate rouging.
To test the effectiveness of Dursan as a rouging prevention option we compared coated and uncoated 316L stainless steel coupons. When exposed to 6M guanidine hydrochloride, 316L stainless steel showed rouging while Dursan coated coupons were unaffected.
Since there was no loss of mass for the coupons after the 1-week trial (scale accuracy is 0.1 mg), they were returned to the 6M guanidine hydrochloride solution to soak for 3.5 more weeks (1 month total exposure). Again, there was no change in the mass of the coupons, but the minor rusting and rouging effects were much more dramatic as seen in figure 2 below.
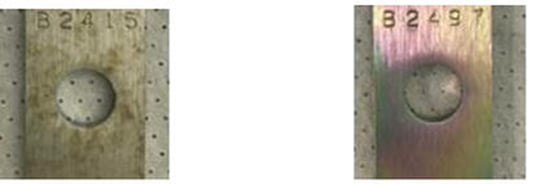
Figure 2: A bare stainless steel coupon (left) and a Dursan coated stainless steel coupon (right) were exposed to guanidine hydrochloride for one month. The rusting on the bare coupon is more severe than the 1 week exposure. As seen previously, the Dursan coated coupon is unaffected by the exposure.
In addition to the increased rouging, there was also a discoloration in the guanidine hydrochloride solution with the uncoated coupon immersed in it for one month. This color change, seen in Figure 2, was not seen at the one-week point of the experiment. The yellow tint to the liquid indicates that iron has leached out of the coupon and into the solution. This is a potential issue for many high purity applications, as iron ions can interact with product and cause impurities and/or low product yield.
Figure 3: Guanidine hydrochloride solutions after a bare (left) and a Dursan coated (right) coupons were immersed for one month. The yellow tint in the solution that contained the bare coupon is a sign of corrosion, whereas the solution that contained the Dursan coated coupon showed no color change over the immersion period.
Conclusion
SilcoTek® coatings are proven to improve corrosion resistance in a variety of applications. In high purity water systems and DI water systems, our silicon coatings act as a non-reactive barrier that protects stainless steel from corrosion. Inert coatings also help to prevent metal contamination and help to protect DI resin beds from contamination. The ultimate benefit is higher quality process water and lower maintenance cost.
Stay current with the latest in corrosion protection in process systems. Subscribe to our email and blog or follow us on LinkedIn.

References:
- F. Mansfeld, J., The Effect of Water on Passivity and Pitting of Titanium in Solutions of Methanol and Hydrogen Chloride. Electrochem. Soc. 118 (1971) 1412.
- M. De Pra, G. Greco, Krajewski, M.P., Martin, M.M., George E., Bartsch N., Steiner, F., Effects of titanium contamination caused by iron-free high-performance liquid chromatography systems on peak shape and retention of drugs with chelating properties. J. Chromatogr. A. 1611 (2020) 460619.
- Menon GR, "Rough and Its Removal from High-Purity Water Systems," BioPharm 7 (1990) 40—43.