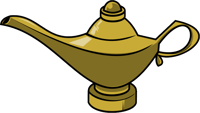
The US election and change in Presidential Administration will most likely bring about unprecedented change in US regulatory statutes. Your guess is as good as mine as to how far regulatory change will go and how long it will take to roll back existing environmental regulations that are seen as a drag on the US economy. One thing is clear. It's going to be messy.Putting the genie back in the bottle may not be easy. Just take a look at US EPA Tier III gasoline standards. By January 2017 refiners will be required to reduce sulfur in gasoline from the tier 2 level of 30ppm to an average of 10ppm. Refiners not in compliance have the option to purchase credits to offset gasoline production that exceeds the 10ppm standard. Non compliant refiners anticipate they'll need to expand hydrotreating processes, especially in naphtha produced in fluidized catalytic cracking (FCC) units. They expect to shell out up to $10 billion in upgrades and an additional $2.1 billion per year in operating costs. Overall project duration of 2+ years is expected.
By now refiners have plotted their course, be it to achieve compliance now or purchase credits and plan for upgrades later. Contracts have been signed and plans made. Now what? For those not in compliance and not planning on making upgrades, they may be in the clear. For those operations that have already modified their processes or secured more expensive low sulfur feedstock, they may be out a significant expense or may become less profitable. Will the US continue to be an outlet for higher sulfur gasoline streams? Or will import regulations also change? My head hurts just thinking about all this!
Taking a long term view it appears that economics and market forces, not regulations, will drive industry (as it really has all along). To be sure, there will be regulatory oversight of oil and gas operations and industry in general, but the compelling argument for either monitoring or change to product will be based on financial or liability concerns. There may be a regulation to minimize sulfur, but if there's a contract with a customer for lower sulfur in their feedstock, you can bet the capability to monitor low level sulfur will be essential and sulfur inertness built into critical flowpath surfaces will be the key factor in successful process control.
At this point there will be winners and losers, as there are in any big change, and there will be opportunity. To take advantage of opportunities follow these simple tips:
- Keep up on the news
- Read industry related social media
- Pay close attention to industry specific trade magazines
- Check US EPA sites for updates and proposed changes to regulations
- Buddy up with your congressman
The Old Sulfur Management Ways Won't Cut It.
Regardless of any potential changes to sulfur regulations, industry continues to move forward. It's more true now than ever, the old sulfur management ways won't cut it. Cost pressures and plant efficiency require reliable efficient process control and sulfur analysis. To achieve better control of your process, stop surface reactions from slowing or distorting analyzer or instrumentation results. Here are a few tips on how to improve the performance and quality of your process monitoring system:
- Stop priming systems. No amount of priming will fix a super adsorptive system.
- Use inert coated fittings? One uncoated fitting will adsorb a significant amount of H2S.
- Rusty sample cylinders? Active compounds will be adsorbed by rust particles, making sampling an exercise in futility.
- Steam cleaning with dirty steam? Particulates in steam will adsorb active sample compounds.
- Make filters inert. Fritted filters have a huge surface area. Making filters non reactive will prevent distortion of analyzer test results.
- Uncoated, reactive regulators? Even components with a brief exposure to the sample will impair quality.
- Protect analyzer tubing with an inert & corrosion resistant coating. Just a few inches of uncoated stainless steel tubing can result in loss of sample.
SilcoNert® 2000 and Dursan® are proven to improve sensitivity and response. Making sampling flowpaths inert will assure compliance and allow operators to focus on operations, not troubleshooting an unreliable sampling system.*
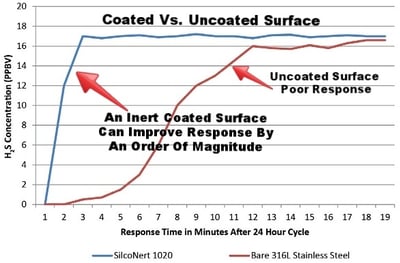
Get more tips on how to improve process control and response:
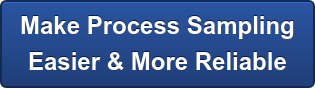
*Data Courtesy of Concoa