
Can SilcoTek coatings prevent deposit formation and coking in analytical and process applications? Read on and get some pretty impressive results!
Fouling can severely impact the performance of processes and instrumentation in just about every industry. The effects of the accumulation of substances, be it binding of proteins in medical diagnostics or carbon particulates in aerospace, can have a range of impacts:
- Increase weight
- Causes contamination
- Reduces flow
- Increases drag
- Encourages corrosion
- Increases emissions
- Increases maintenance requirements
- Creates false results
- Costs money!
|
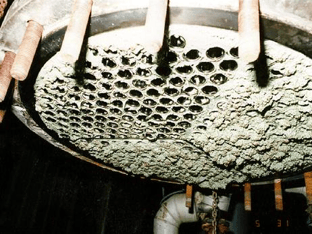 |
A High Price
Dealing with the impacts of deposits and build-up of unwanted materials depend on the application and importance of the process. Regardless, the cost can be high. Here are some examples of the impact of material build-up on critical surfaces:
- Medical / bio analytical
- -Annual costs of false results in USA >$3 billion annually
- Automotive
- -10%+ increase in fuel consumption due to fouling
- Refining
- -$0.5 billion spent to overcome coking issues (2002)
- Heat exchangers
- -50% of maintenance costs are caused by deposits, causing billions of dollars to industry.
Read our presentation on preventing coking and fouling
Potential Solutions
There are many possible solutions to the problem. Some expensive, some not realistic, most are costly and can result in redesign or added maintenance. Here are a few examples:
Solution |
Result |
Increase energy / power / fuel consumption (basically brute force idea) |
Expensive and does not solve the problem |
Control the incoming media that’s causing deposit build-up |
Rarely an option in industrial applications |
Material selection |
Several options, difficult to optimize performance & cost |
“Surface engineering” through advanced anti-fouling coatings |
Flexible and cost effective
Modify the existing part’s surface to make it behave how you need it to
|
The Benefits of Coatings to Prevent surface interaction
Inert Coatings can be an effective solution for multiple applications and industries because they enhance the performance of the surface while preventing interaction of the base material with the interacting substance. The result? A better surface without changing the part design or physical property of the base material. There are, however, several factors to consider when selecting the right coating for the application. Such as:
-Do I have to re-engineer to account for tolerance changes? In most cases no change in tolerance needed. But consider for super high tolerance applications.
-Is there an environmental impact? The amorphous silicon surface has very little environmental impact both during processing and as a product.
-Can the anti-coking coating withstand temperature, abrasion, corrosion, etc. in the application? In many cases, yes but consult with a SilcoTek representative to be sure.
-How long will it last? Depends on the application, but the coating should provide superior performance for years. Contact a SilcoTek representative to discuss your application.
Want to learn more about our coatings and how they improve the performance of your product? Get our webinar on demand.
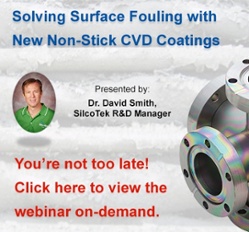
How SilcoTek Coatings Prevent build-up
SilcoTek coatings act as an inert barrier, preventing catalytic or chemical interaction with the underlying surface. For example nickel containing substrates catalytically form carbon deposits (coke) from petrochemical media. Causing build-up on the surface. Coatings like SilcoKlean® or Dursan® bond to the surface and change the surface energy and inertness, preventing chemical adhesion and adsorption of the substrate. The coating's low energy surface prevents the attachment of flow path chemicals to the surface. Applications include:
SilcoTek Solutions & Applications |
|
|
|
|
|
Problem |
SilcoTek Coating Solution |
|
Carbon deposit, coke, formation from incomplete burning of fuel |
SilcoKlean barrier coating reduces catalytic coking and carbon deposit formation |
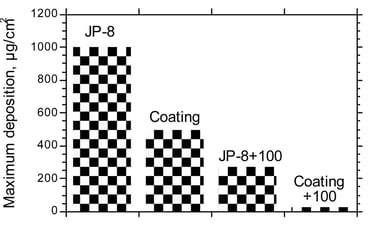 |
Bio-fouling in food applications. Spores from sour milk suspensions stick to testing equipment |
Dursan prevents sticking by up to 76% |
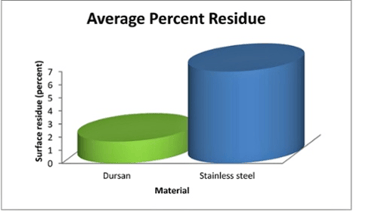 |
Protein binding in medical diagnostics |
Dursan prevents surface interaction and sticking |
 |
Carryover in GC & HPLC chromatography |
Dursan corrosion resistance prevents pitting & sticking to flow path surfaces |
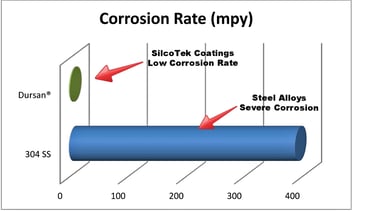 |
SilcoTek offers many solutions to the problem of sticking, corrosion, deposits and carryover. Go to our solutions page to learn more about our coatings.
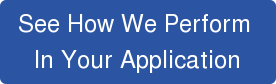