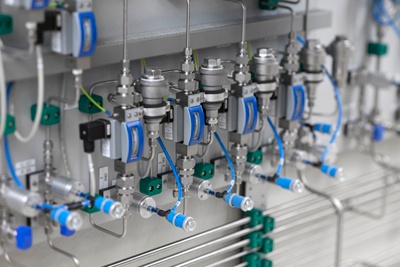
Not getting the sample quality you expect? The problem may be corrosion in the analytical sampling flow path. In this blog post we discuss ways to identify and correct critical flow path corrosion problems.
Critical flow path components (be it tubing, fittings, valves, sample cylinders, reactors, instrument components, or analytical columns) are a key link in many process control regimes. The word critical does not relate to the cost of the item, but to the impact it can have on systems or processes when it fails. An inert sample flow path, used to sample process fluids under real time process conditions, can allow companies to accurately assess the quality of products and processes; if they fail, costs rise and product quality can suffer.
If a critical component is exposed to corrosive chemicals or is contaminated, mishandled, or poorly maintained, that key link to product quality can fail. That's because a poorly maintained flow path can result in surface corrosion which can lead to contamination, test failures, product quality problems, plant system failures, or environmental compliance issues. As a result, managing corrosion is an important factor in avoiding analytical, process, and yield problems.
In this blog post you will learn:
|
Checking the flow path for corrosion
It’s not uncommon for sample cylinders or other flow path components to be exposed to highly corrosive chemicals like H2S, HF, hydrochloric, and sulfuric acid during analytical process sampling. Exposure to high concentration corrosives can “come with the territory” in industrial applications and can unfortunately compromise stainless steel surfaces. Corrosives can attack the surface and potentially result in pinholes, pitting, or generate adsorptive rust particles. What appears to be a minor amount of surface pitting can have a big impact on analytical results, especially when sampling low concentrations of reactive compounds. That's because active compounds can bind to rust particles and pitted surfaces, resulting in adsorption, cross contamination and test error.
Learn how to prevent stainless steel adsorption and improve analytical sampling. Get our ultimate guide to analytical sampling.
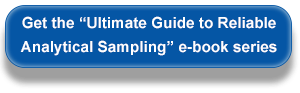
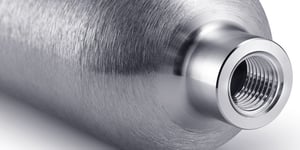
Here are a few signs that instrumentation or sampling flow path may have a corrosion problem.
- Loss of analyte. Test results or a calibration test is showing lower than expected levels of key analytes.
- Qualification sample not consistent. Variability can be a sign of adsorption and desorption skewing results.
- Particulates in sample stream. Rust particles can dislodge from the surface and contaminate down stream flow paths.
- Liquid in what should be a dry gas sample stream. This could be condensation or acid build-up in the sample cylinder or flow path. Both can result in corrosion.
- “Off color” liquid flowing from the sample system.
- Time. If the sample cylinder or sample system has been in service for a relatively long time without maintenance (this can be weeks, months, or years depending on the process environment), the surface may be suffering from corrosion.
- Valves show signs of corrosion or are not operating smoothly. This can be the result of corrosion or other contaminants.
What to do if components show signs of corrosion?
Inspect the interior, thread, and seal area thoroughly with a borescope. For sample cylinders, be sure to examine the shoulder area of the cylinder wall carefully. That area can tend to accumulate particulates and pitting. For valves, probes, or regulators, disassemble and inspect all areas, especially blind holes or crevices (places where particulates or moisture can accumulate.
- Remove sample cylinder valves and visually inspect the sample cylinder with a borescope (magnification helps!).
- Look for pitting and rust, especially at the cylinder shoulder and threads, or component blind holes and crevices.
- If the flow path is dirty, clean it with the least damaging method, i.e. mild high purity solvent or high purity nitrogen.
Read our stainless steel cleaning guidelines
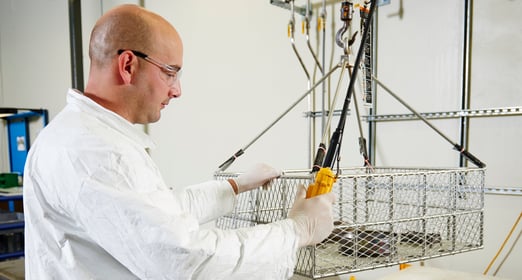
Before inspection clean the flow path. A clean surface will make inspection easier, and make it easier to identify surface pitting. Also clean surfaces periodically when in service. A clean surface can prevent analyte adsorption, and produce more reliable results.
- Be aware that many cleaners can themselves leave a reactive trace film on the surface. Test cleaning methods to assure the surface is really clean.
- Increasing the cleaning fluid temperature can also help to remove contaminants.
- Some cleaning solvents have an effective or optimal cleaning temperature range, especially engineered solvent mixes developed for ultrasonic cleaners.
OK, I’ve got corrosion. Now what?

If you find pitting or surface rust, you’re now faced with a choice, keep the sample cylinder or flow path component and try and remove the rust, or scrap and replace. Your choice has a lot to do with the risk you face if cleaning the component is not effective. For example, attempting to remove rust and reusing the sample cylinder can result in additional rust failures in the future and can compromise the pressure rating of the sample cylinder. Analysts may be risking the quality and safety of future tests by attempting to save the sample cylinder. But some analysts may feel the risk if acceptable. If you choose to remove the corrosion, be sure to follow your company guidelines for removing rust from stainless steel or follow approved handling and care procedures recommended by the manufacturer. Here are some general guidelines for removing rust from stainless steel. (click the link below)
How to Remove Rust from Stainless Steel.
Note that you may still risk the return of rust even after removal. Once rust starts, it can be difficult to stop, so the risk of contamination and adsorption can remain even after applying an inert corrosion resistant coating to the surface. That’s why we recommend replacing a corroded component rather than attempting to clean and reuse it.
Preventing Corrosion
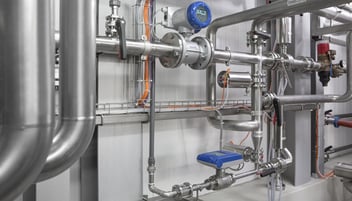
You can prolong the life and performance of critical components by applying an inert, high durability corrosion resistant coating like Dursan® to flow path surfaces and the interior and exterior of sample cylinders. Dursan® is both inert and resistant to chloride corrosion, H2S, and corrosion from most acids. Dursan® is non-reactive and corrosion resistant, improving both test quality and corrosion resistance. The summary below demonstrates the superior corrosion resistance of Dursan to common process chemicals. Immersion in high concentration corrosives show a significant improvement in corrosion resistance for Dursan coated stainless steel.
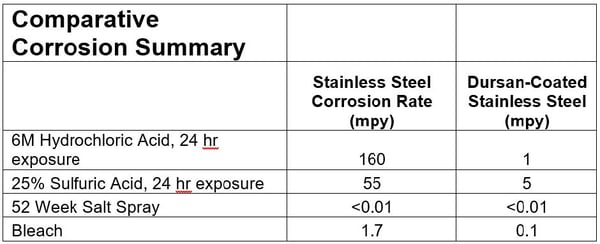
SilcoTek® inert coatings do not have a shelf life. Our coatings should deliver ultra-inert performance for years, but that’s not to say that the sample cylinder, valves, or fittings may not have corrosion or inertness issues in severe environments. They will add significant life to components and improve system performance in a cost effective manner.
Have other questions about inert coatings? Ask the experts. Contact our technical service team, visit us on linkedIn or go to our FAQ page.
Go to our Frequently Asked Questions page.
