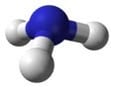
Trace ammonia sampling in automotive, refinery, and industrial applications can be tedious at best and impossible under worst case conditions. If you've ever experienced progressively erratic and irrelevant results when testing for trace ammonia, Bertrand S. Lanher, PhD. with Sensors, Inc. may have an answer to your problem. Dr, Lanher compared stainless steel, PTFE, and SilcoNert® 2000 coated tubing (noted as Sulfinert) for relative inertness, adsorption, and retention of trace level NH3.
Dr. Lanher's test results show that for even a relatively short 3 meter length of transfer tubing an adsorptive surface can result in significant delay in response and test errors.
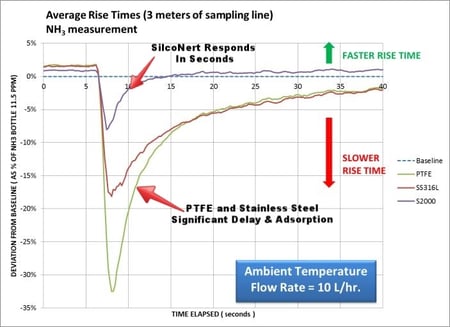
In fact, test errors can be significant, initial NH3 signal rise time results show major differences:
- 32% less response with a PTFE tubing flowpath
- 18% less with a stainless steel flowpath
- 8% less with SilcoNert flowpath
The study concludes:
"Results unequivocally show that, at equivalent operating conditions of temperature, pressure and flow rate, Sulfinert®-coated SS316L sampling lines offer the fastest response and recovery rates for the measurement of NH3 using an extractive spectrophotometric method when compared to PTFE and standard SS316L sampling lines."
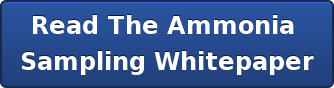
Why Response Error Matters
Reactive flowpaths like PTFE and stainless steel will hold onto an ammonia sample, causing delayed readings or artificially low readings. As the NH3 accumulates in the system flowpath, it will eventually desorb or leach into the sample stream, resulting in high readings. The back and forth adsorption and desorption ultimately makes testing less and less relevant to real world conditions. At minimum a reactive flowpath will reduce test efficiency while the analyst struggles to recalibrate or purge the flowpath. At worst, a reactive flowpath will skew test results, jeopardizing regulatory compliance or may lead to process stream contamination or reduced yield. This can be especially important for refinery and process continuous testing systems and automotive emissions testing.
Fast response means less chance of a cumulative build-up of reactive compounds in the system and fewer test errors. The key to fast response? A surface that does not retain or adsorb the analyte. The graph below shows SilcoNert® does not adsorb the NH3 analyte, so there's little resulting desorption and disruption to analytical results.
SilcoNert response time to baseline is the shortest of the 3 surfaces compared:
- Stainless Steel: 33 seconds
- PTFE: 18 seconds
- Sulfinert: 9 seconds
- Baseline: 6 seconds
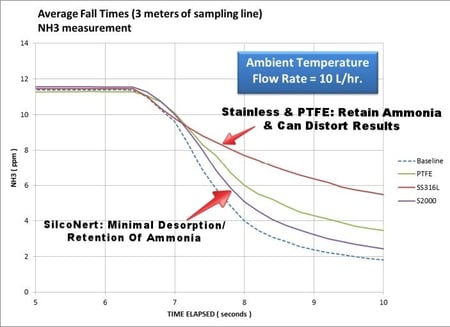
Coat The Flowpath
The fix for ammonia test problems? SilcoNert coat the entire flowpath.
A short piece of tubing may not seem like a test killer, but the results prove that seemingly little things like an inert surface in the flowpath can make the difference between garbage results and consistent, robust results. Other components you should coat are:
- Fritted filters: Each frit has a huge surface area. Not coating frits can lead to similar performance issues.
- Regulators: Although less surface area, they too can retain NH3, distorting calibration gas integrity & leading to calibration errors.
- Valves & fittings: As detection limits move from part-per-million to part-per-billion sensitivity, even small fittings and valves can retain and distort results.
- Sample cylinders: Internal surfaces of sample cylinders are quite rough, making ideal conditions for adsorption of ammonia.
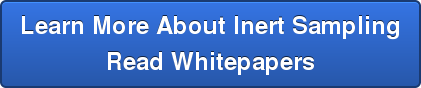